電動ドライブトレインのNVH最適化 快適な音環境を演出する
Dr. Carsten Mohr
グライダーが滑空するような静粛走行は、電気自動車の重要なセールスポイントの一つである。しかし、電気自動車は設計上、電動パワートレインからの高周波ノイズが発生する。そこで、電動部品が車内音響環境にどのような影響を与えるのか、開発の初期段階で予測する必要がある。開発が進んでからの「トラブルシューティング作業」には時間と手間がかかるため開発初期に音響性能を最適化することが望ましい。そこでシェフラーは、問題解決のためのツールを開発した。これらのツールにより、早い段階で騒音を予測し、音響パターンの原因を特定することができる。ツールの有効性は、シェフラーの電動アクスルを搭載したデモカーで検証した。部品音響測定に基づく騒音合成のほか、バックグラウンドノイズを取り込んだ総合的なシミュレーションと車内騒音の音響レンダリングを実施した。シミュレーションと車内騒音実測値とは高レベルで一致し、この先取的手法の基本機能と情報価値が確認できた。今後は、この手法ですべての開発プロジェクトをサポートする予定だ。
シェフラーの音響設計開発
すべての騒音には意味がある。騒音を耳にした人は無意識に発生源について想像を働かせる。その音は良い意味をもつのか、それとも欠陥に関係するのか。我々は、経験を基に音の種類を区分している。電動モータの駆動により生じる高周波音が車内騒音とならないよう、とくに電動パワートレインの音響性能の最適化に注意が向けられている。
シェフラーは過去にも、デュアルマスフライホイール(DMF)などのトランスミッション部品やCVTトランスミッション開発時に同様の問題に直面した。現在では、30年以上に及ぶシミュレーションと計測経験から得た音響専門的知見を体系的に電動パワートレインに応用している。関連システムについての体系的知識集積により、各種仕様を満足する高ロバスト性の限界曲線を開発の初期段階で明確に確定できる(図1)。限界曲線のロバスト性は、量産時における寸法外れや生産車両のばらつきを許容可能な程度に抑制し、車両全体として望ましい音響性能を保証する。
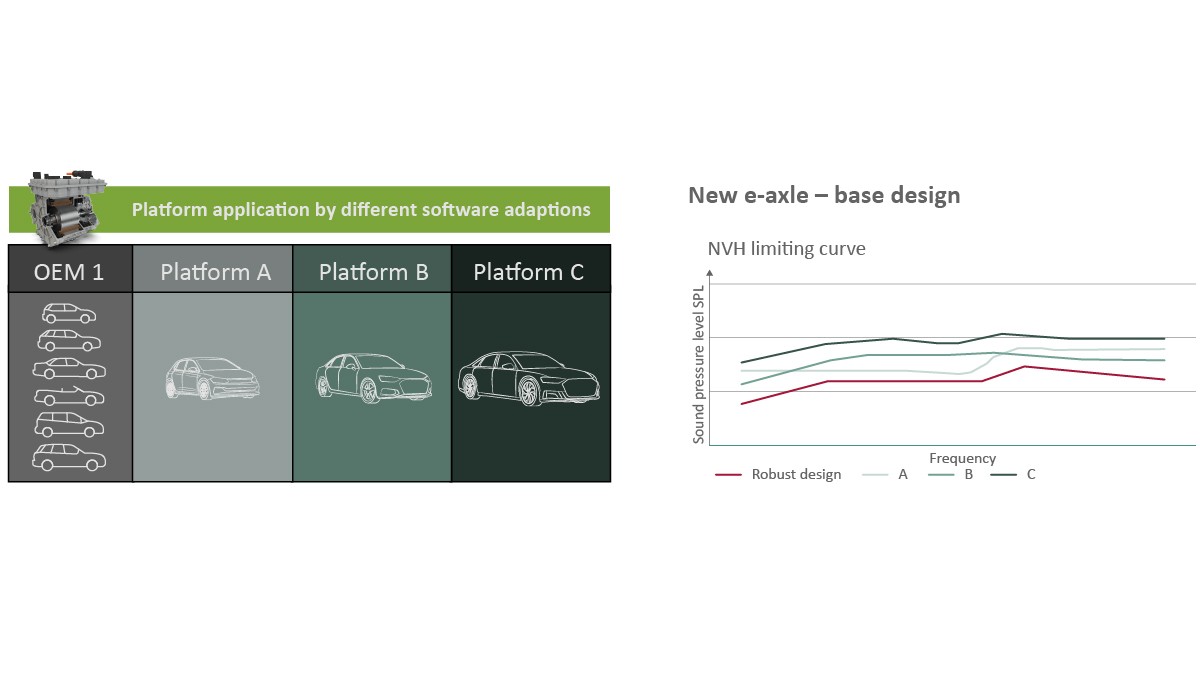
こうした方法で、時間とコストのかかる不具合対策を最小限化することできる。理想としては、さまざまなソフトウェアの組合せを介して、車両プラットフォームに適応させ、モジュール化を通して全車種やメーカーへ拡張して自動車メーカーにコスト面でのメリットをもたらすことが望ましい。
全く新しい車両コンセプトのドライブシステム開発において、従来の限界曲線があてはめられない場合がある。このような場合においては自動車メーカーとドライブシステムサプライヤーの緊密な連携が重要である。車両の全体像がまだ見えない場合や、情報が部外秘とされている場合でも、シェフラーは絶えず蓄積する豊富な知見と各種データベースを活用して、開発の初期段階でNVHに関するおおよその結論を引き出し、開発プロセスの正しい針路を示すことができる。
システムサプライヤーにとって重要な部品の限界値を、車内騒音に関する顧客要求による音響変数として求めるためには、騒音を生み出している物理現象の連鎖全体を探求することが必要である。こうして、車両全体の騒音目標値を個々のサブシステムや部品に個別に割り振ることができる。図2に、その手法の概要を示す。
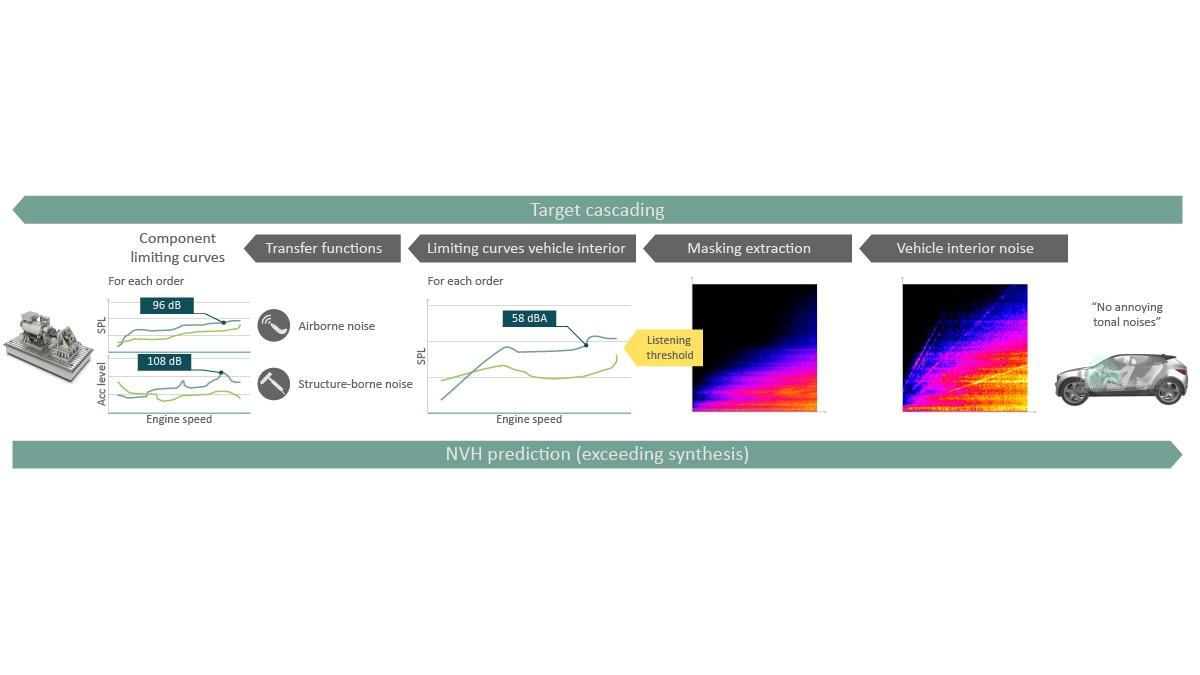
開発プロセスの出発点は車内騒音である。既存車両用に新ドライブシステムを開発する場合、測定値を使用できる。車両もパワートレインも新規に開発する場合は、比較的特性の近い基準車両(旧モデルなど)を使用できる。基準車両のバックグラウンドノイズも、必要に応じて変更できる。新世代車両で風切り音低減の必要性がすでにわかっている場合などである。まず、電動モード走行時に発生する風切り音やタイヤ音など、すべてのマスキングバックグラウンドノイズを対象車両や基準車両の車内騒音から抽出する。マスキングノイズは、電動モータ、トランスミッション、パワーエレクトロニクスなどからのノイズが、運転への集中を妨げないために使用される。マスキングバックグラウンドノイズの抽出は、マスキング閾値を定義することによって行う。マスキング閾値とは、例えば「ブーン」というバックグラウンドノイズのなかで、個々の音が聴こえる(知覚可能とみなされる)点を表わす閾値である。シェフラーは、独自評価基準を採用している。すなわち、この種の可聴音が引き起こす不快感のレベルに応じて騒音をグループ化し、顧客と事前に取り決めた車室内の静音性を保証している。車室内の音響許容レベルが決定されれば、ドライブシステムと車室間の伝達機能を用いて、試験装置で測定するコンポーネントの空気伝搬音と車体構造に伝わる固体伝搬音の限界曲線を求めることができる。
この手法を逆順に応用して、部品騒音が車室内の音響パターンに与える影響を開発の初期段階で予測することも可能である。部品ごとに環境とは無関係な騒音放出があるかどうかを判断し、各部品騒音の伝搬挙動について、空気伝搬経路と固体伝搬経路を区別することで把握できる。固体伝搬音の経路では、構造物の振動が広がらないように隔離するか、または振動エネルギーを消散させて減衰させる必要がある。空気伝搬音の経路では、部品の放出する空気伝搬音が「部品騒音」として伝わる。この場合も、隔離・減衰によってエネルギー伝達中の周波数に応じた減衰を達成することができる。このプロセスから、個別部品の車室内騒音を定量化できる(音響合成とも呼ばれる)。最終的には、現実のバックグラウンドノイズ(風切り音やタイヤ音)をマスキングノイズとして考慮しない限り、全体的な車内騒音についての結論や、騒音の知覚または部品を原因とする不快感についての判断はできない。
応用例
ハイブリッド専用トランスミッションの最適化
シェフラーは、ハイブリッド専用トランスミッション(「マルチモードトランスミッション」ともいう)等の、ハイブリッドパワートレインのさらなる発展に取り組んでいる[1](図3)。
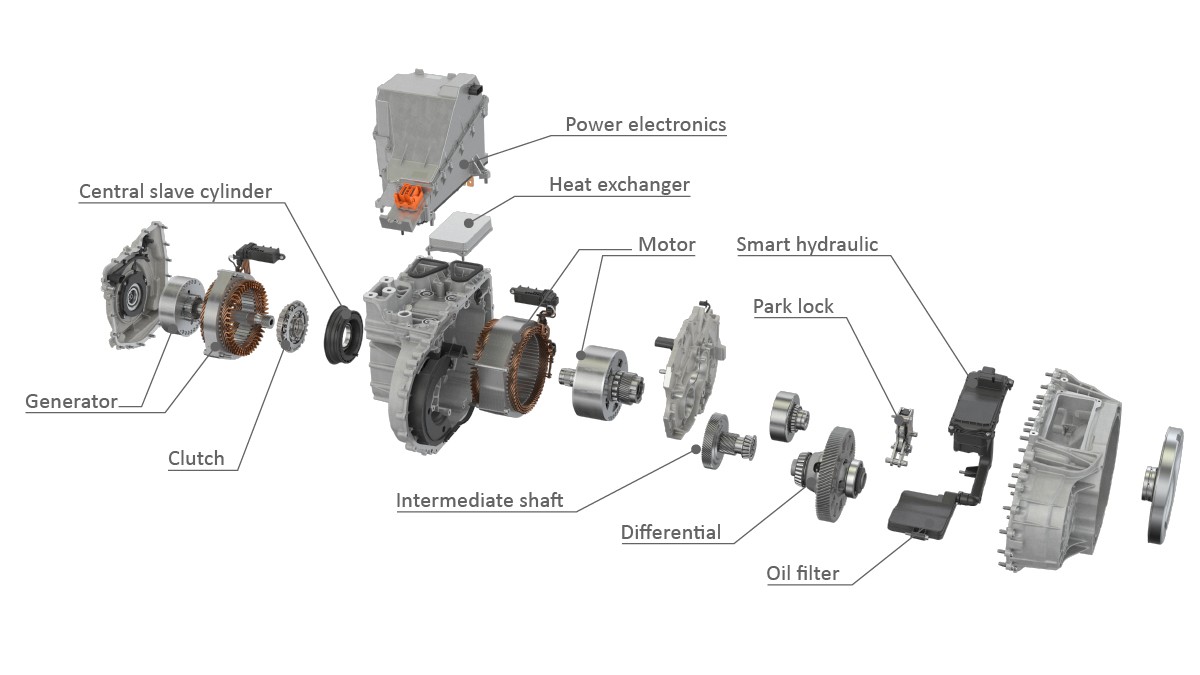
構造的には、2つの電動モータとセンタークラッチで構成される固定減速比トランスミッションで、以下の運転モードが可能なように選定されている。
- 内燃機関による直接駆動
- P1位置のジェネレータを内燃機関で駆動し、P3位置のモータを駆動
- バッテリ電源を使用してP3モータを駆動
振動技術の観点からみた重要課題は、3D設計データを利用できない段階において、発生電磁力が構造物の振動に及ぼす影響について判断を下さなければならないことだった。
シェフラーがステータ設計専用に開発した解析プログラム「VibStaSim」では、スロット数や極数などのパラメータが変動するときに、電磁力モードと構造の振動モード間に発生しうるカップリング効果について判断することができる。
設計の初期段階で、電動モータ(EM)構成と構造寸法を正しく組み合わせることで、共振カップリングをドライブシステムの動作範囲外となる高速域にシフトさせることができる。この自社開発ツールは、解析用の数式を用いて、数百種類の電動モータを音響評価も含めて瞬時に比較できる。
スロット数と極数に関して電動モータ(EM)構成決定後、電動モータ振動の最適化が開始される。ユニット全体の振動挙動に対する電磁力の影響をみると、低速域では接線方向の力が大きく影響し、高速域では径方向の力が支配的である。(図4)。
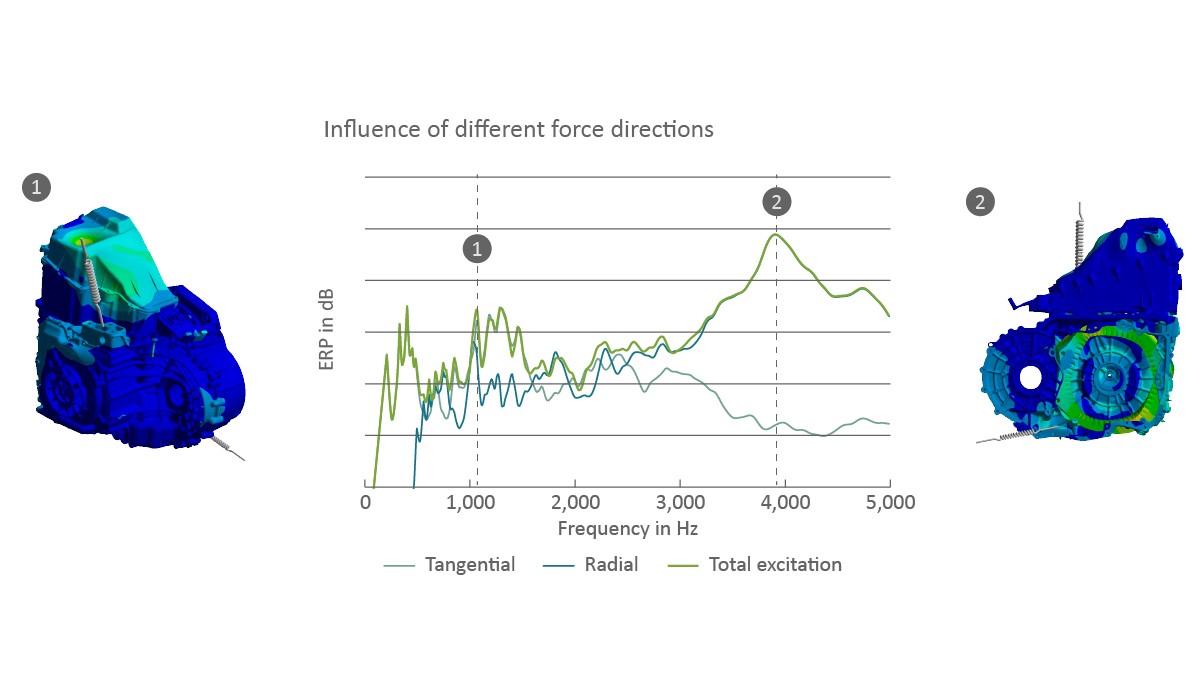
電動モータ振動の最適化には、速度の異なる2つの力の方向を解析する必要がある。更に、変更を加える際には効率と性能要件をそのまま保つことが必要である。作業は多次元的なマルチフィジックス最適化となるが、メタモデリングによって効率的に実行できる。多数の個別最適化パラメータを組み合わせることで、音響性能と高効率との間に発生する矛盾をある程度まで解決できる。
電動モータの振動挙動の最適化後、力による振動、すなわちハウジング構造の振動挙動について検討する。ここでは、先に定義した限界曲線が必須の評価基準となる。この曲線を超える場合は、原因である構造上の変位特定が必要である。その後、構造体の形状を局所的に補強する(図5)。感度解析を実施し、リブ補強などの修正パラメータを予備段階で綿密に制限して、質量や設計寸法に影響を与えずに改善策を実施することができる。
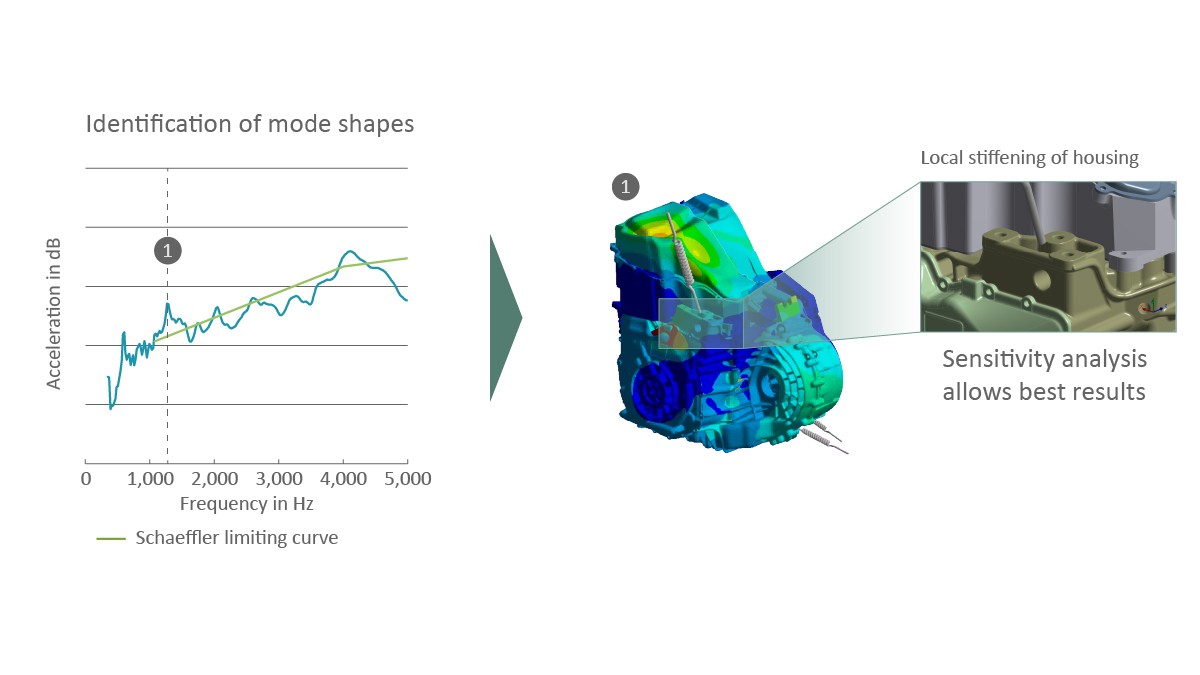
電動モータの振動が構造体に伝播することを抑制した後に、空気伝搬音を低減する。流体モデルとハウジングの表面振動を組み合わせて、空気伝搬音を推測し、周波数に対する限界曲線と比較する。構造の最適化と同様、ハウジングに局所的な対策を施すためには、どの面からの騒音が限界曲線を超えているのかを明確に特定することが重要である(図6)。これにより、補強面を広げるなど、小規模な形状変更で空気伝搬音を低減して、限度値を守ることができる。
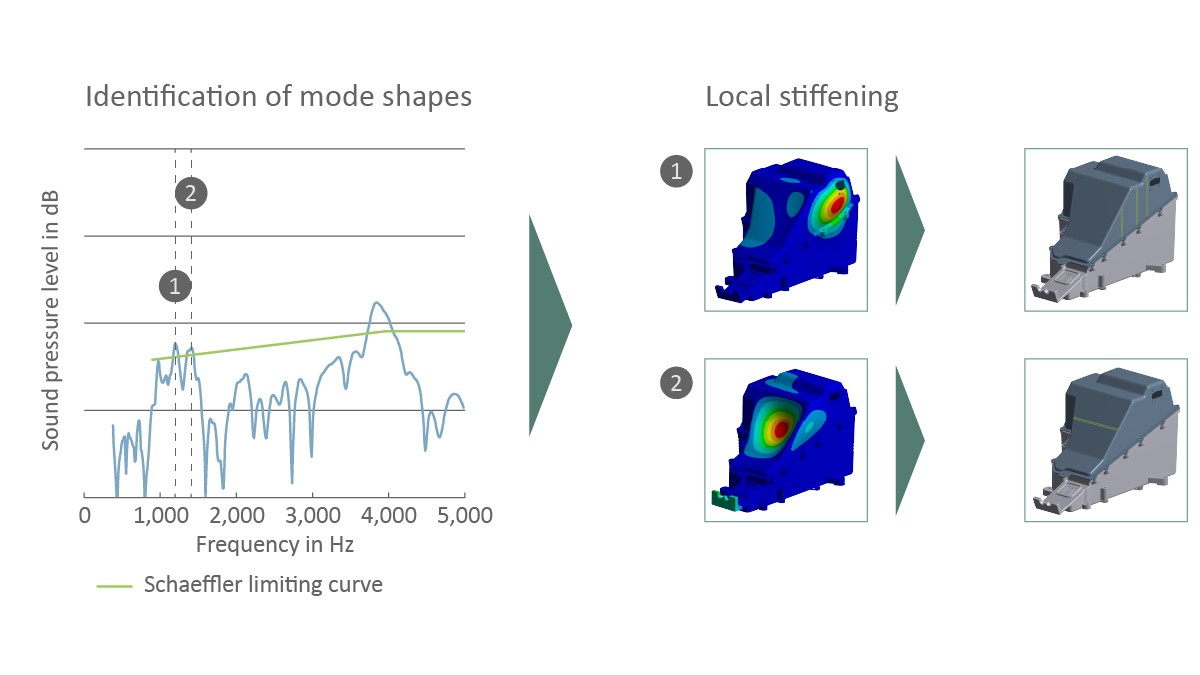
アクスルのギア歯の最適化
シェフラーの電動アクスルは、電動モータ、パワーエレクトロニクス、トランスミッションが一体化されている。エンジン車ではエンジン音によりマスキングされるギヤノイズが、フル電動の電気自動車トランスミッションではマスキングされないばかりか、より快適で静粛性の高い車室内環境を求める自動車メーカーの要求に対応する必要がある。ギヤの音響最適化に使用するパラメータとしては、歯形かみあい率から歯面形状の変更にいたるまで多数のパラメータがある。しかし、かみあい率を任意に大きくすることはできず、歯面形状を変更しても最適効果が得られるのは特定の負荷領域に限定される。電動ドライブの伝達系に対するNVH面での高い要求を満足させるためには、振動を最適化するだけでは十分ではない。
形状のマクロ的・ミクロ的最適化後に残る伝達系の伝達誤差は、マルチボディシミュレーションの振動入力変数として役立ち、トランスミッション構造全体の動的挙動を表わすのに利用できる。この場合も、最小振動、最適トランスミッション、最小限ノイズのシステム全体の解析が重要である(図7)。開発目標は必ずしもギヤノイズを可能な限り低減することではなく、ノイズがドライバーに聞こえなくすることである。バックグラウンドノイズを含む車室内全体の騒音を考慮することが不可欠なのはこのためである。
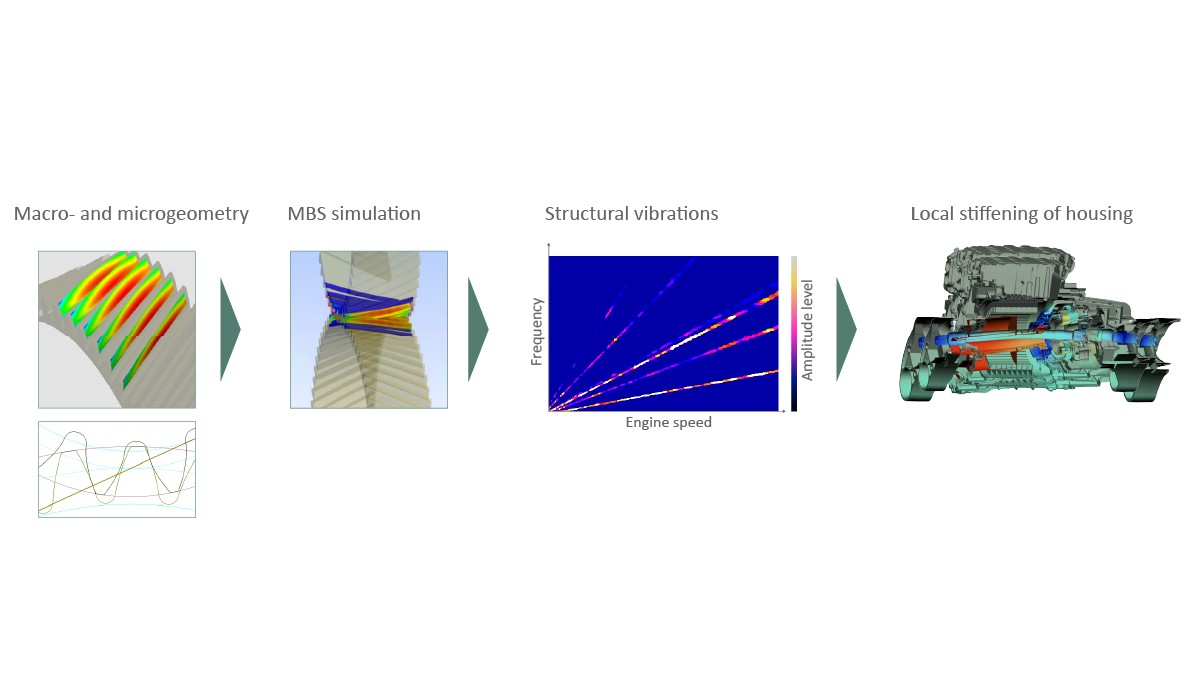
アキシャルフラックスモータの設計
シェフラーは、高出力密度の電動ドライブ用に、現在一般に使用されているラジアルフラックスモータに代わるアキシャルフラックス電動モータを開発中である[2]。このモータは音響性能に問題があり、これまで自動車には採用されてこなかった。そこで、シェフラーはコンセプト開発段階でパラメータスタディを行った。その結果、2つのステータ間にロータを挟み込んだI型構造が、2つのロータがステータを挟み込むH型構造よりも、騒音と振動の点で優位性をもつことが明らかになった(図8)。これは、ロータの補償力がエアギャップの影響を最小限にするからである。また、ロータの軸受固定方式により公差と磁束通路を短くすることが可能となる。ハウジングの径方向のねじ止めは、できるだけ内側に配置することで、簡単かつ効果的に振動を切り離すことができ、ハウジング表面への固体伝搬音を最小限に抑えられる。アキシャルフラックスモータは、フランジ接続部がインプットシャフトの軸受サポート付近にあるので、軸方向の外力による振動に対して一定のロバスト性があり、NVH挙動に有害なエアギャップへの影響も最小限に抑えることができる。
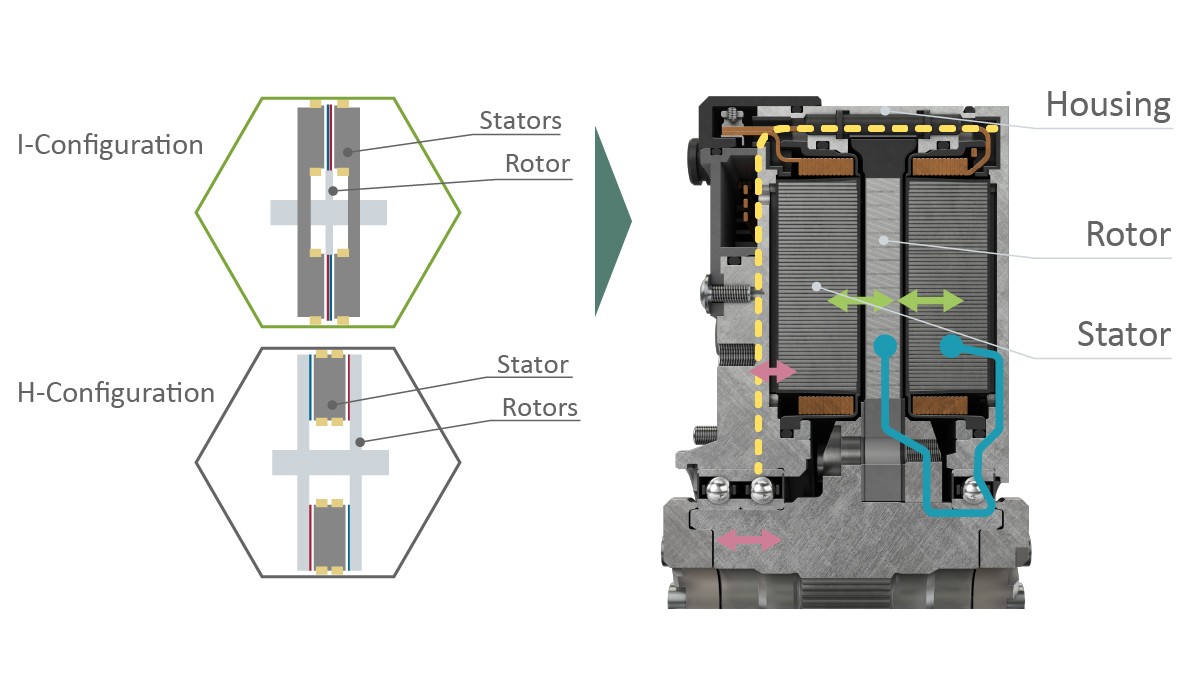
目的はアキシャルフラックスモータをベースに最適な出力重量比の高性能ドライブを設計することだが、低対向質量の小振動が比較的大きな振動を発生させ、音響挙動に悪影響を及ぼすこともありうる。こうした振動は、音響的に最適化された制御システムである” Harmonic Current Injection”(HCI)を用いることで、ある程度まで電動モータ内部で減衰できる(図9)。HCIにより、NVHに大きくかかわるトルク振動や、ある種のアキシャル荷重(ラジアルフラックスモータの場合はラジアル荷重)をともに大幅に低減できる。シェフラーは、制御と応用のノウハウだけでなく、実機搭載に必要なシステム知識も備えている。
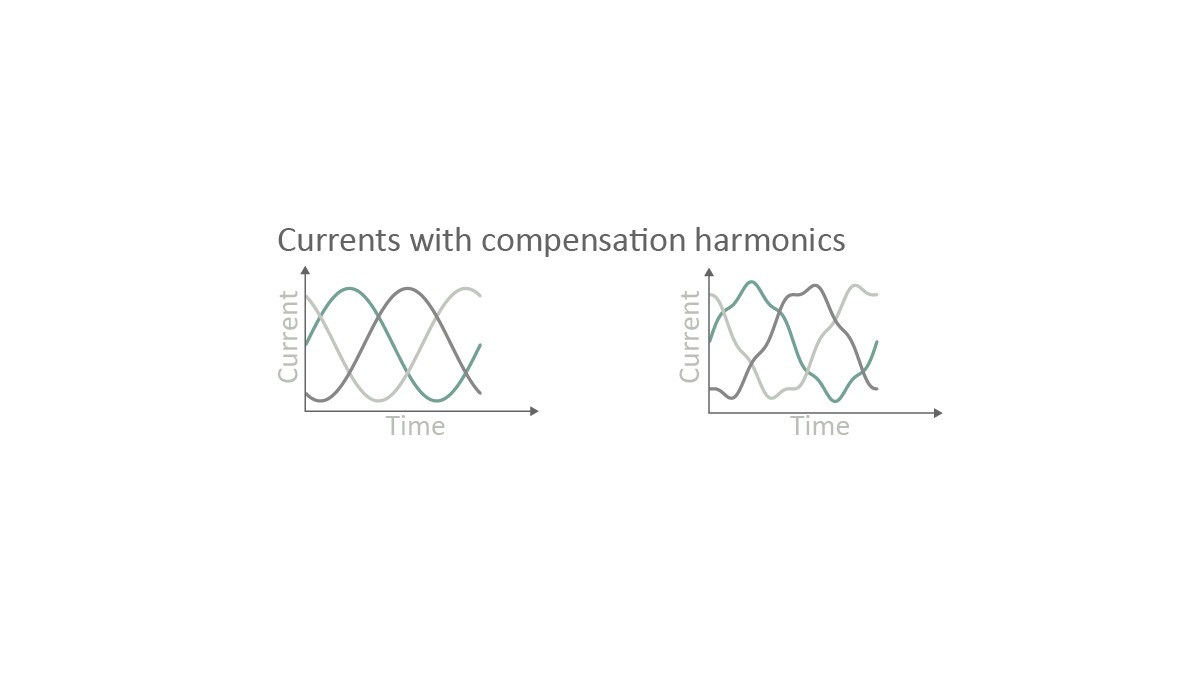
HCIでは、ステータに正確な正弦波電流を供給するのではなく、高調波電流を与えて任意の次数の高調波を減衰させる。シェフラーは、この電動モータ制御の基礎をカールスルーエ工科大学との共同研究により開発した[3]。機能の詳細な説明は文献[4]にある。第36次高調波の例から、HCIにより音響挙動を大きく改善できることがわかる。この手法の利点は、効率には何ら影響を与えずに実施できる点にある。
車室内騒音の予測
ドライバーが実感する車室内騒音を、シェフラーは一連のツールを活用し開発の初期段階で予測できることをデモカーで証明した。この手法を用いて部品結合部に伝わる入力を的確に予測し、更に空気伝播音と組み合わせた入力データとして、車両の音伝搬経路モデルへ適用する。空気伝搬音と固体伝搬音をそれぞれの伝達経路で別個に解析し、車室内騒音に寄与するものとして合成する。その後、データベースからのバックグラウンドノイズと速度を同期させて重ね合わせて、車室内の音響状況に関する現実的なシミュレーションとする。この手法により、発生する音を明確にし騒音の質や騒音が引き起す不快感の程度を個別の要素ごとに評価することも可能である。
車室内騒音予測のレベルを上げるためには、部品振動と車室内への伝搬だけでなく、車速に応じたタイヤ音や風切り音を詳細に表現することも重要である。予測された車室内騒音と実測値とを比較すると、きわめてよく一致していることがわかる(図10)。
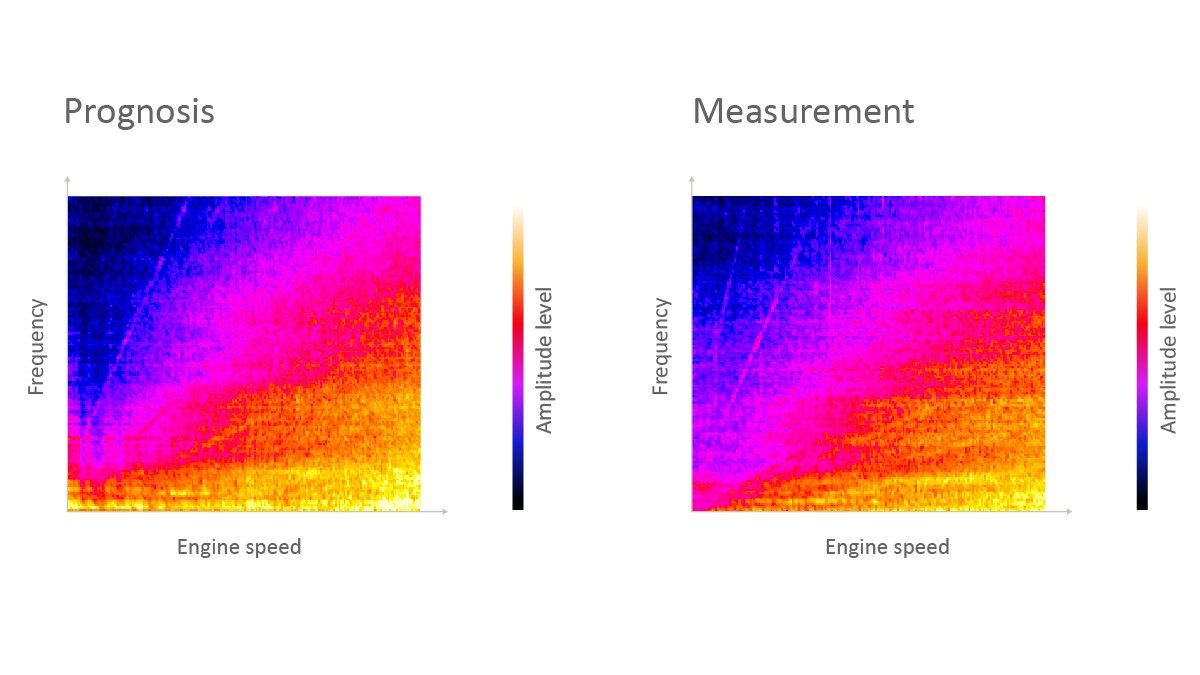
冒頭で述べた開発ツールを使用すれば、各種製品の比較が可能となり、各駆動部品の音響性能開発におけるパラダイムシフト、すなわち、「可能な限り高い静粛性」から「必要な静粛性」へのシフトを実現できる。こうしたアプローチは、電動ドライブがその資源効率の良さから市場を拡大するための一助となる。
まとめ
お客様にとって、音響快適性は、ハイブリッド車や電気自動車の重要な品質性能の1つであるが、そのなかでも車室内でドライバーが感じる音響ノイズ性能は特に重要な性能である。運転中に各部品から生ずる騒音がドライバーに聞こえるのは、他の騒音や運転音にかき消されていないときだけである。シェフラーはこの音響性能を向上させるという課題に対して、車両全体で包括的に解決する手法を採用し、関連技術の開発と社内試験設備の拡充を図っている。
特に個々の部品やサブシステムに対して各々の周波数領域の騒音限界曲線を定義すること、それが要求される車室内騒音レベルを達成する有効な手段であることがわかっている。
開発プロジェクトにおいて、音響性能を満足するために、特定の仕様、コスト基準に基づいて設計される各部品が設計仕様内に収めることができなくなった場合、最初に着手するのは振動の発生源を特定し、可能な限り振動を抑制することである。次に、物理現象に従って伝搬する振動音響の経路と、ハウジングなどの部品の音響応答挙動に注目し、騒音レベルの最適化を図る。騒音に関係している部品を特定できれば、要求される質量や設計寸法内に収まる最適解を得られるケースが少なくない。部品が原因となって発生する車内騒音は、ハウジングなどの振動が空気を介して伝達される空気伝搬音と、部品の振動が接続部を経由して車体構造に伝わる固体伝搬音の2つに分けられる。最終的には、車内騒音を現実感覚としてとらえ、騒音品質の予測を正しく行うためには、すべてのバックグランドノイズを考慮する必要がある。
本稿では、シェフラーが開発しているアキシャルフラックスモータ、ハイブリッド専用トランスミッション(DHT: Dedicated Hybrid Transmission)、電動アクスルなど、幅広い電動ドライブトレインを例に、車両レベルの騒音仕様を各部品レベルの仕様に落とし込み、音響設計の観点で最適化する手法を示した。この手法を用いることで車室内の騒音を正確に予測することが可能となり、車両側の音響設計の開発効率の向上にも寄与する。
[1] Eckenfels, T. et al.: Innovative Hybrid Transmission With Electric DNA. Bühl: Schaeffler Kolloquium, 2022
[2] Homm, M.: Fascination Electric Powertrain. Bühl: Schaeffler Kolloquium 2022
[3] Langheck, A.; Doppelbauer, M.: Harmonic current injection for torque ripple reduction with optimum current trajectory for minimum induced voltage. 22nd IEEE International Conference on Industrial Technology (ICIT), 2021, doi: 10.1109/ICIT46573.2021.9453480
[4] Rathke, G.; Stehle, B.: Bits Meet Metal ─ Optimal Electric Drive Trains by Integrating Innovative System and Software Functions. Bühl: Schaeffler Kolloquium, 2022