レース参戦の意義 新DTMエレクトリックの車両コンセプトおよび駆動システム
Dr. Jochen Schröder | Daniel Kohl | Dominik Störkle
シェフラーは、DTMの競技団体ITR (Internationale Tourenwagen Rennen e. V.) レースシリーズ・イノベーションパートナーとして、「DTMエレクトリック」と呼ばれる完全電動レーシングカーレースの実現に大きな役割を担っている。シェフラーは、電動駆動システムとステアバイワイヤシステムの開発だけでなく、総合的な車両コンセプトと性能目標の策定にも参画している。DTMエレクトリック参戦車両は、シェフラーの標準駆動システムとステアリングシステムを搭載する。これには、モータ、パワーエレクトロニクス、トランスミッション、サーマルマネージメントシステム、集中車両制御ユニットの駆動機能、そして「Space Drive」ステアバイワイヤ技術が含まれる。車両レベルで可能な限り最高のパフォーマンスを達成するために、シェフラーは総合的なアプローチの一環として、DTM エレクトリックレースカーの開発プロセスから設計しました。 物理的および技術的な基本検証から始めて、車両全体のシミュレーションと走行テストの結果を車両のシステム要求に反映し、サブシステムと統合コンポーネントの要件を導き出す。 シェフラーは現在、ITR と協力して、2024 年以降の DTM エレクトリックで使用される車両のプロトタイプ バージョンを開発中である。
電動レーシングカーによるモータースポーツでの成功
シェフラーは長年にわたり、国際的モータースポーツに不可欠な存在であり続け、パートナーチームに電動駆動システムとシャシーの革新的なシステムおよびコンポーネントを提供している。シェフラーにとって、レースの意義は表彰台に上がることだけにとどまらない。レーストラックは開発プロセス全体にわたるイノベーションの究極のテストベンチなのである。開発とは、駆動ユニットとシャシーのコンポーネントやシステムなど個々の開発から、車両レベルでの統合にいたるまでのトータルなプロセスである(図1)。シェフラーがモータースポーツで獲得した知識は、関連の専門部門との緊密な連携を通じて、量産のための研究開発に活用される。逆に、研究開発で得た知識がモータースポーツに応用される場合も多い。たとえば、Schaeffler は、2021年に初めてDTMに「Space Drive」ステアバイワイヤシステムを投入した[1]。これは、GTCシリーズとNürburgring 24時間耐久レースで成功をおさめたことに続くものである。「Space Drive」システムの技術は、身体障害者用の車両にその起源をもち、その信頼性はすでに10億kmを超える総走行距離で実証されている。レースでも、その高いドライビングダイナミクスのポテンシャルが証明されている。
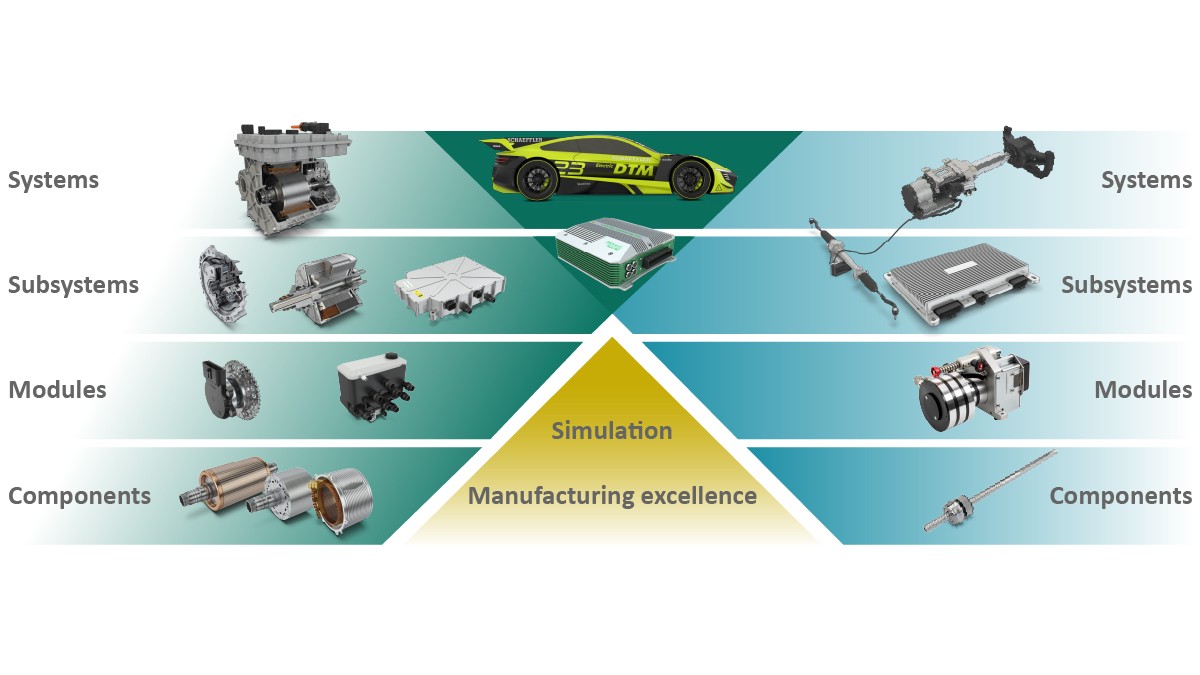
電動レーシングカーによるモータースポーツは、これまでABB FIAフォーミュラE(通称フォーミュラE)と密接に結びついていた。シェフラーは、2014年から2021年まで、フォーミュラEに積極的に参戦し、2015年以降はCompact Dynamics社およびABT Sportsline社と提携してフォーミュラEレーシングカー用の革新的駆動システムを開発してきた。2017/2018年シーズンからは、アウディと技術提携し、Audi Sport ABT Schaefflerチーム用に駆動システムの開発を推進してきた。最適化された駆動システムは、5シーズンにわたって成功をおさめ、多数の勝利に貢献した。フォーミュラEでの共同実績がそれを物語る。Audi Sport ABT Schaefflerチームは、2022年初頭(第8シーズン開幕前)、フォーミュラEシリーズの歴史上、どのチームよりも多く表彰台に上り、獲得ポイントも最多である。Audi Sport ABTチームも、フォーミュラEの第3シーズンではドライバーズ選手権で総合優勝、第4シーズンではチーム選手権で総合優勝を果たしている。
DTMエレクトリック向けの総合的車両開発
シェフラーは、DTMの競技団体ITR(Internationale Tourenwagen Rennen e. V.)のレースシリーズ・イノベーションパートナーとして、「DTMエレクトリック」と呼ばれる完全電動レーシングカーレースの実現に注力している。シェフラーは、技術パートナーとして駆動システムとステアバイワイヤシステムの開発に参画するだけでなく、総合的な車両コンセプトと性能目標を構築するという責任も負っている。2020年には、すでにフォーミュラEで使用している駆動ユニットを4つ搭載したデモカーを製作した。シェフラーは現在、ITRと連携して2024年以降にDTMエレクトリックで使用する車両のプロトタイプ開発に取り組んでいる(図2)。
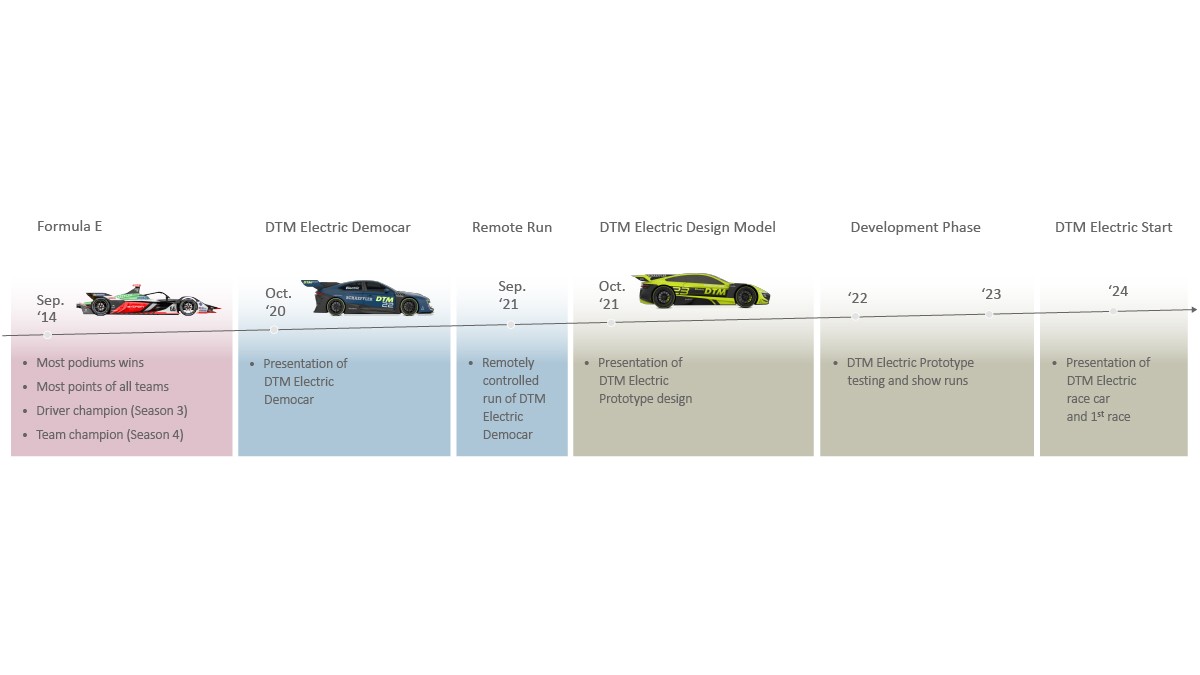
DTMエレクトリック向けの電動レーシングカー開発は、パワフルな車両とエキサイティングなレースを可能とする革新的駆動系技術とシャシー技術のベンチマーク確立を目指している。独立したホイールの駆動構成による簡単な実装と最大 1,000 kW までの電気駆動の利点を十分に活用して、運転するのにも挑戦的な車両を構築していく。
DTMエレクトリックの電動レーシングカーの仕様を決定する作業は、観客やレースチーム、ドライバー、スポンサーの誰にも魅力的な総合コンセプトを一連の技術要件に落とし込む作業である。前記の独立したホイールの駆動ユニットと最大1,000 kWのパワーにより技術要件が確保され、時速320 kmを超えるトップスピードと、5秒以下で0~200 km/hに達する加速時間が実現される。ラップタイムは、これまでの電気自動車レースよりも大幅に速くなるだけでなく、現在のGT3 DTMレースのラップタイムよりも速くなるはずである。最後に重要なことは、電気自動車モータースポーツでは当たり前のレース戦略である「リフト&コースティング」(コーナーでブレーキをかける前の惰行)は、観客が期待するレースの魅力をそぐだけであるから禁止される。その結果、ドライバーは最低でも25分間、制約なく走行に集中することができる。
このような高性能プラットフォームは、競技者に対して高額な参加費用の支払いを強いることなく実現可能である。管理が容易で予測可能なコスト構造が明らかにされると同時に、車両間での差別化を可能にする機会も提供される。コストに関していえば、DTMエレクトリックはレースの参戦車両について標準化された駆動システムとシャシーの使用を義務付ける予定である。ただし、OEMにとって技術的に関連する分野(蓄電技術、急速充電能力、その他関心領域)は、競争による技術発展を促すために開発の自由が維持される予定である。詳細は今後公開される予定である。
ホリスティックな開発プロセス
バッテリ駆動の電動レーシングカーに対する要求レベルは非常に高い。理由は2つある。1つは、高電圧バッテリのエネルギ密度が内燃機関用の化石燃料と比較して低いこと。もう1つは、過酷なレース条件により平均出力が非常に高いレーシングカーには、要求の厳しい走行プロファイルが必要とされるからである。これらの要求事項を満たす開発目標を達成するためには、両立困難な多数のパラメータを検討して、優先度を正しく見極める必要がある。バランスよく、すべての要求仕様を満たす車両システム実現に向け、シェフラーは車両全体レベルでの包括的開発プロセスを採用している。まず、物理的・技術的な基本原理の検証を実施後、シミュレーションや性能試験の結果などをシステムレベルへ移行・反映させてゆく。こうした検討を基に、サブシステムや統合部品への要求を設定する。図3(左)はVモデルを利用した開発プロセスを示す。シェフラーの開発領域(緑)は、部品設計から車両搭載と検証にいたるまで技術の全レベルを対象としている。図3(右)は、シェフラーが車両設計に盛り込んだ高レベルの開発目標を示す。このうちのいくつかについては、以下でさらに詳しく述べる。
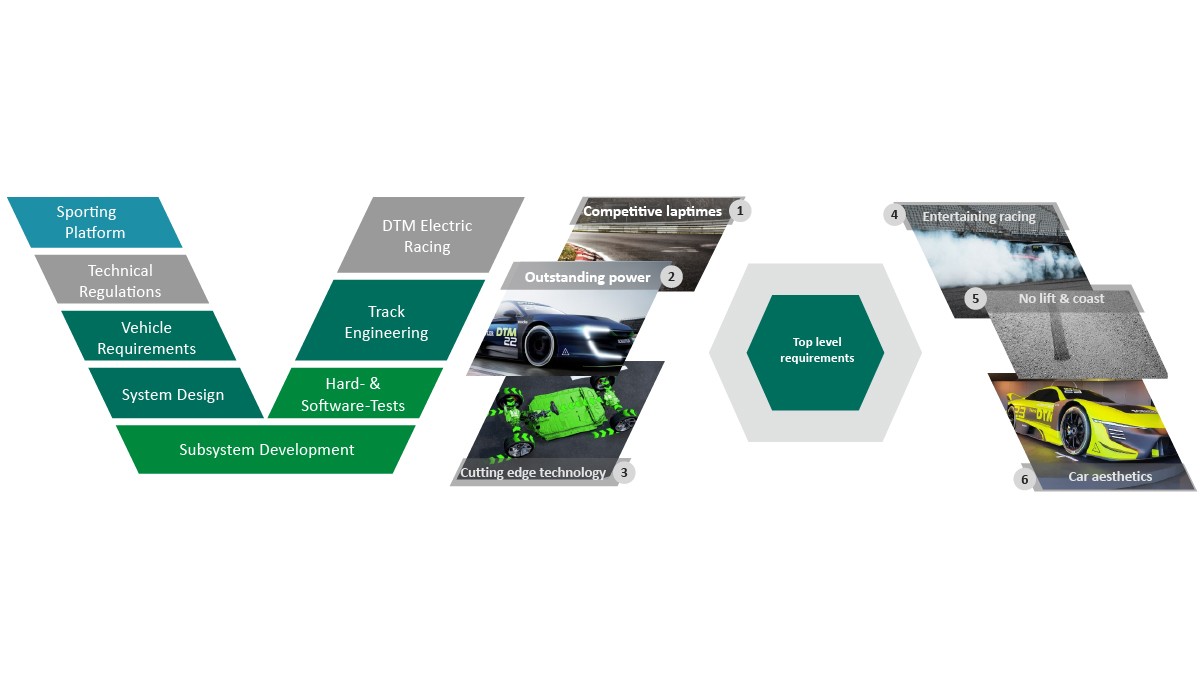
車両設計
レーシングカー開発においては、車両性能に最も大きく影響するのは、駆動力、車両重量、エアロダイナミック設計(空気抵抗の変化に伴うダウンフォースの変化)、およびタイヤのグリップ力である。これは特に、バッテリパックのエネルギ密度が比較的低いため、ラップあたりのエネルギ出力が制限されているレーシングシリーズに当てはまる。
ラップタイムにもエネルギ消費にも好影響をもたらすという理由で、レーシングカーでは車両重量を極力軽量化する。しかし、エアロダイナミック設計、タイヤグリップ、駆動力という車両重量以外のパラメータについては、理論的に可能なラップタイムを短縮すると、必要駆動エネルギが増大する場合がある。これは総駆動力を高めた場合に当然起こり得ることである。シェフラーは、感度分析の一環として、タイヤグリップ、駆動力、エアロダイナミック設計を変化させたときの標準的レースでのラップタイムへの影響を調査した。パラメータの変更によってラップあたりのエネルギ消費が変化した場合は、バッテリ容量と車両重量を適宜に調整してレースタイムは変わらないようにした。
3つのパラメータの影響を以下に例を挙げて説明する。一つ目は3つのパラメータとエネルギ消費の関係、もう一つは、3つのパラメータとラップタイムへの影響を観察した。図4(上段)のように、ダウンフォースを25%、駆動力を15%、またはタイヤグリップを10%下げることにより、エネルギ消費は等しく10%削減できる。これだけをみると、タイヤグリップが効率を最適化する最善の方法だと思える。しかし、図4(下段)のラップタイムへの影響をみると、正反対の結果がみえてくる。タイヤグリップを下げて効率を上げると、ラップタイムが大幅に遅くなる。一方、各運転ポイントでのダウンフォースは、ラップタイムに大きな影響を与えずに相当変化させることができる。これは、ダウンフォースを下げるとコーナリング速度は低下するが、ドラッグとのトレードオフで走行抵抗が最小限に抑えられて直線での走行速度が増すためである。搭載するバッテリの容量と重量を下げることもできる。つまり、ダウンフォース/空気抵抗のパラメータは、効率向上の総合的な余地が大きいといえる。シェフラーは、こうした検討を行ったうえで、タイヤグリップ、ダウンフォース、駆動力の仕様を個別に設定して車両開発を進めている。
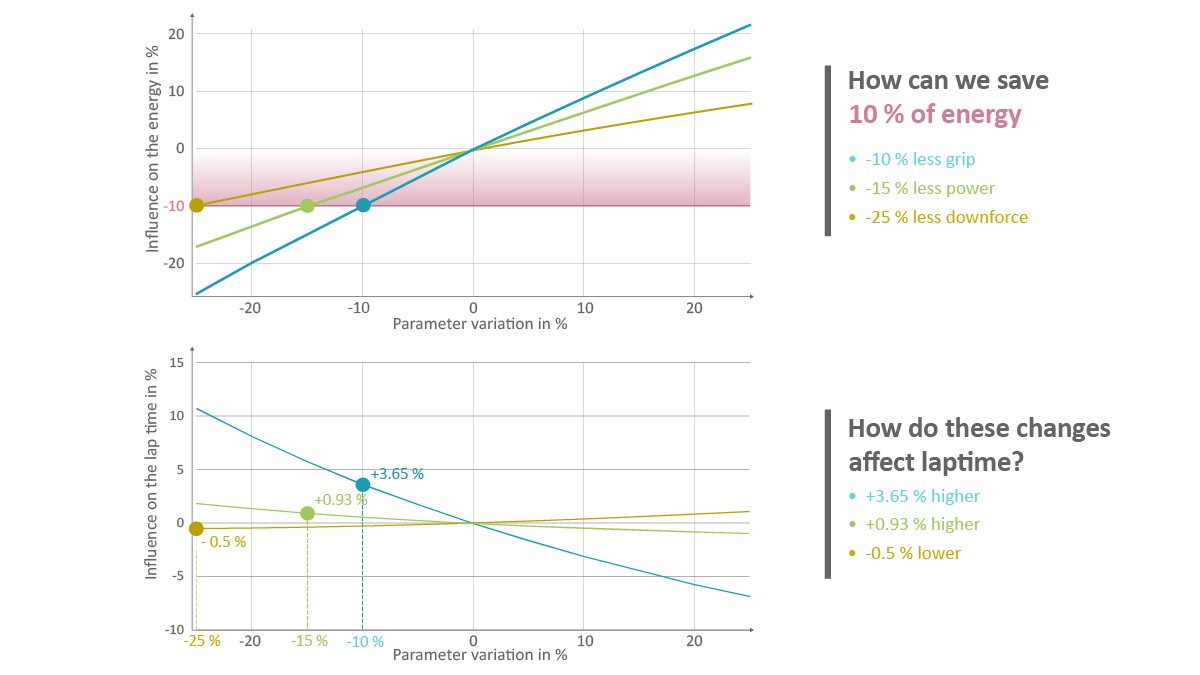
エアロダイナミクス/ダウンフォース
上述のように、ダウンフォースと抗力は相互に影響し合い、ダウンフォース係数を増加させると抗力係数も増加する。ダウンフォースが大きいとタイヤの接地力が増して、タイヤはより大きな縦方向と横方向の力を伝達できるのでコーナリング速度は向上する。しかし、大きくなった抗力は全体的な走行抵抗を増大させ、直線での速度が低下して車両が必要とするエネルギは増大する。DTMシリーズとDTMエレクトリックシリーズとではコンセプトが異なるため、エアロダイナミック設計についての優先順位の設定を変えなければならない。従来のエンジン車では、ダウンフォース増加のメリットが、空気抵抗が大きくなるという欠点にまさるが、DTMエレクトリックシリーズ車では効率の観点から空気抵抗を下げることをより重視する必要がある。図5(左)は、クラス1(内燃機関搭載の旧DTMプロトタイプ)とDTMエレクトリックのレーシングカークラスの空気抵抗とダウンフォースをグラフにしたものである。クラス1車両の数値は、グラフの右上の狭い領域にある。しかし、DTMエレクトリック車には効率上の制約があるため、セットアップはグラフ左下領域を目指して行われる。ラップあたりの必要エネルギ分析では(図5中央)、抗力係数が約0.35となる設計を目標にするとエネルギ消費を大幅に削減できる。図5(右)は、他車両コンセプトと比較したときのDTMエレクトリック車の抗力係数とダウンフォースを示す。DTMエレクトリック車では、エアロダイナミック設計の最適化により、走行性能を制限することなくバッテリを約10%軽量化することが可能である。その結果、DTMエレクトリックシリーズでは従来のクラス1車両と比べて低いダウンフォースと抗力係数値で、ドイツ・ホッケンハイムサーキットでの最適ラップタイムである94秒程度を実現可能である。
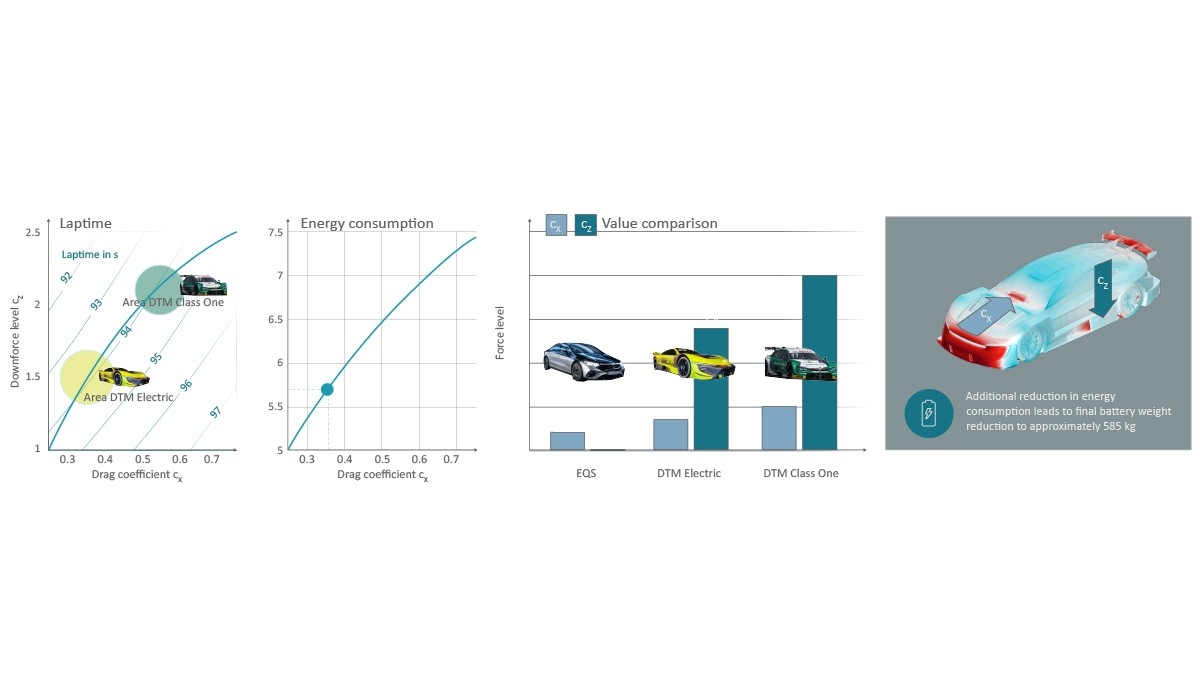
こうした結果をプロトタイプ車のエアロダイナミック設計の目標値として、流体力学シミュレーション(CFD)を実施する。エアロパーツは、DTMシリーズ規則に従い、すべてのチームで統一される。エアロパーツには、リアディフューザー付きアンダーパネル、フロントスポイラー、リアスポイラー、フロントスプリッター、サイドスカートがある。
ブレーキエネルギの回生
DTMエレクトリックシリーズでの1,000 kWを超える高システム出力と、最短でも25分というレース時間によって、駆動システムの開発には高度の要求が課される。現在最先端の高電圧バッテリでさえ、エネルギ密度は従来の内燃機関用の液体石油燃料に比べて、60分の1と著しく低い。双方のエネルギ要求量を同一と仮定すると、電気自動車の重量は相当に重くなり、レースでのドライビングダイナミクスは大幅に低下し、ラップタイムが遅くなる。そうなると、DTMエレクトリックは従来レーシングカーのレースほどの魅力がないということになる。電動モータの2つの特長が、エネルギ保存に関するデメリットを補う。第一は、95%を上回る電動モータ効率である。これは40%程度が上限の内燃機関よりはるかに優れている。それでも、エネルギ密度に換算すると、まだ25分の1という本質的な難点は残る。第二は、電動モータは発電機としても使用できることである。このように使用すると、レース中のコースティング(惰行)やブレーキ操作時に運動エネルギを回収してバッテリの充電量を上げ、航続距離を延ばすことができる。
モータやバッテリの設計時には、技術的にどの程度の回生出力が可能かという点が重要である。重要な要素としては、車両全体のパワートレインアーキテクチャである。減速時、フロントアクスルの荷重が増大する為、より高い回生出力を実現できるのは、フロントホイールということになるが、同時にリアアクスルにも悪影響を与える。DTMエレクトリック車ではこのような特性を活かすため、シェフラーは4つの電動モータを使用する四輪駆動コンセプトを採用した。各モータは他のモータとは独立して動作する。つまり、各モータは1つのホイールだけを駆動する。この方式により、特定の走行状況でのホイールの接地力分布とヨーモーメントへの影響に関して、駆動トルクを完全に可変的に配分できる。図6は、ドイツ・ホッケンハイムリンクのヘアピンカーブ手前で強くブレーキをかけたときに達成できる回生レベルの例で、シミュレーションで求めたものである。
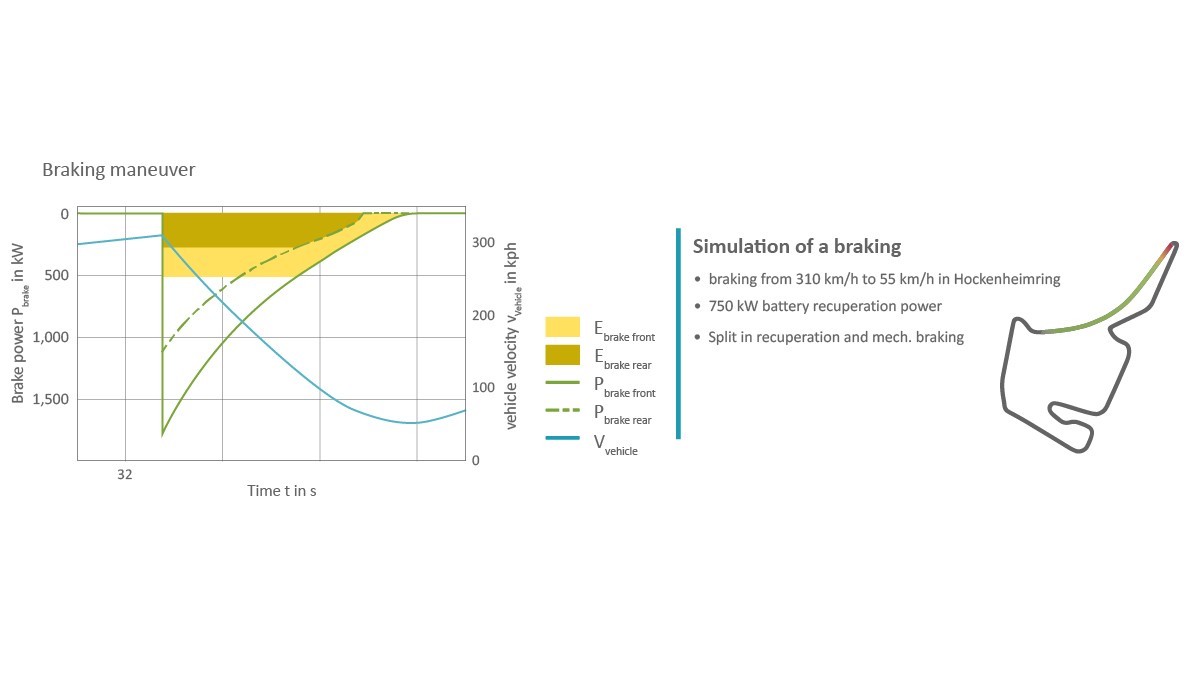
図7は、ドイツ・ホッケンハイムリンクを走行したレーシングカーの総エネルギ回収量の算出結果である。図7(左)は、1ラップで達成可能な最大回生出力を横軸にプロットしている。この出力は、当該車両のパワートレインの技術的構成によって決まる。縦軸は、ラップでの車両正味エネルギ必要量である(ラップの前後でのバッテリ充電状態の差)。回生率ゼロ時は、エネルギが全くバッテリに戻されないため、エネルギ必要量は約10 kWh である。回生率が高くなるほど、正味エネルギ必要量は少なくなる。回生出力750 kW時の必要量は5.7 kWhで、回生率ゼロ時のほぼ60%に相当する。図7(中央)は、この関係を、必要とされるバッテリ容量に置き換えたものである。ここでも、達成可能な最大回生出力を横軸にプロットしている。左の縦軸は、1回のレース(目標:25分+最低1ラップ)に必要なバッテリ容量である。回生を行わずにこのレース距離を走行するには、約200 kWh のバッテリ容量が必要となる。現在の標準的なリチウムイオン電池を使用すると、バッテリ重量は1,000 kgを超える。これがモータースポーツに適さないことは言うまでもない。一方、回生出力が1,000 kWであれば、バッテリ容量は100 kWhですみ、サイズも2分の1に小型化できる。
特にモータとバッテリの設計を行うときは、回生出力と必要重量とのバランスを見つける必要がある。強力なモータと充電速度の速いバッテリーシステムはエネルギ回収の可能性が高く、必要正味バッテリ容量は少なくてすむ。ただし、図7から分かるように、効果は直線的ではない。回生出力が増すほど、回生可能エネルギのゲインが減少するためである。逆に、充電電流を要求仕様の範囲内におさめるために必要なセル数が多くなると、バッテリ重量は再び増加する。したがって、それぞれの負荷プロファイルに最適な回生出力を求めることが必要である。DTMエレクトリックシリーズの場合は、使用可能なセル仕様と負荷プロファイルの枠内で、約750 kW の回生出力が確認された。これにより、必要なバッテリ容量を113 kWhに減らすことができ、それに伴って駆動システム全体の重量も低減できた。図7(右)に、電動ブレーキと機械式ブレーキ間のブレーキエネルギの配分、フロントアクスルとリアアクスル間のブレーキエネルギの配分を示す。ホッケンハイムサーキットでは、この設計で総ブレーキエネルギの約3分の2を回収できることがわかる。これらの結果は、機械式ブレーキシステム開発用の設計パラメータを決定する上で有用である。機械式ブレーキシステムは、電動制動力が大きく、熱負荷も従来レーシングカーよりも相当に低くなる。
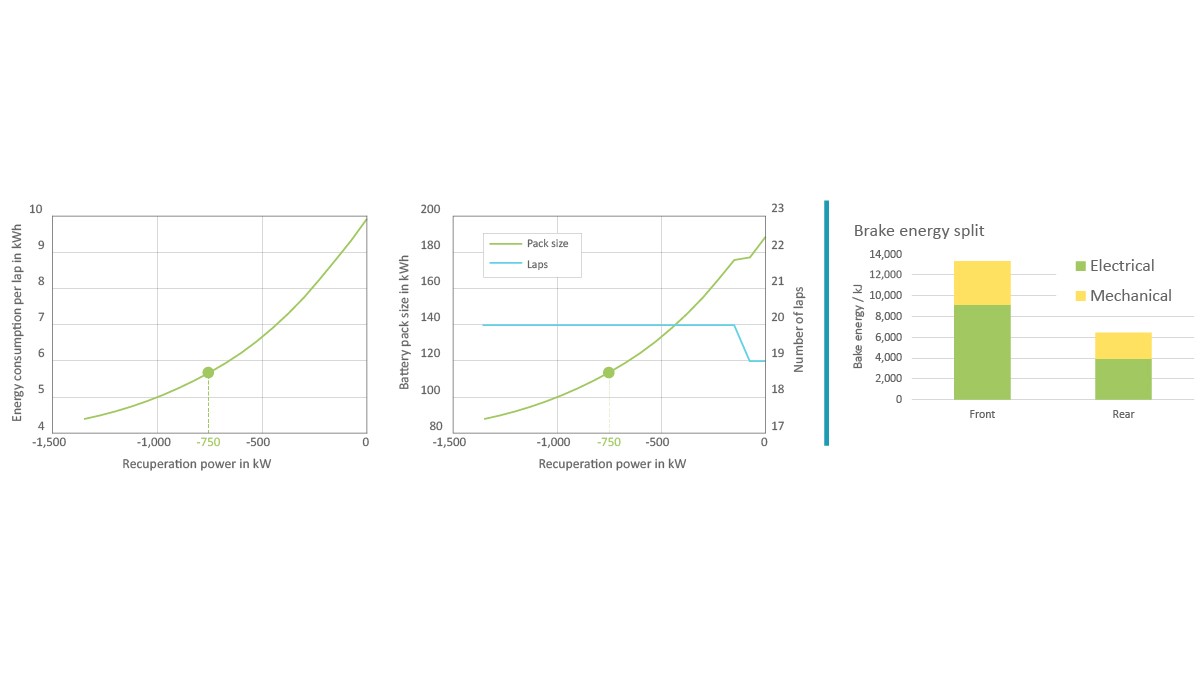
急速充電戦略
ピットストップは、レースに戦略的要素を加え、観客の興趣を高める。また、走行距離を変えずにレース時間を延ばす事も可能である。図8は、ピットストップの違いがレース時間に及ぼす影響を示したものである。ピットストップを行わないレース戦略に比べ、低速でピットに入るだけでもレース時間は延びる。さらに、実際にピットで費やす時間がこれに加わる。その時間はバッテリの短時間充電に利用できる。充電エネルギは、車両の航続距離を延ばすとともに、レース距離の延長にも寄与する。750 kWで90秒間充電すると、6分以上レース時間が延びる。ピットストップのない20分間のレースをベースにすると、DTMエレクトリックレースの目標とする総走行時間である最低25分は、急速充電戦略で問題なく実現できる。これは高電圧バッテリの仕様に要件として盛り込まれている。
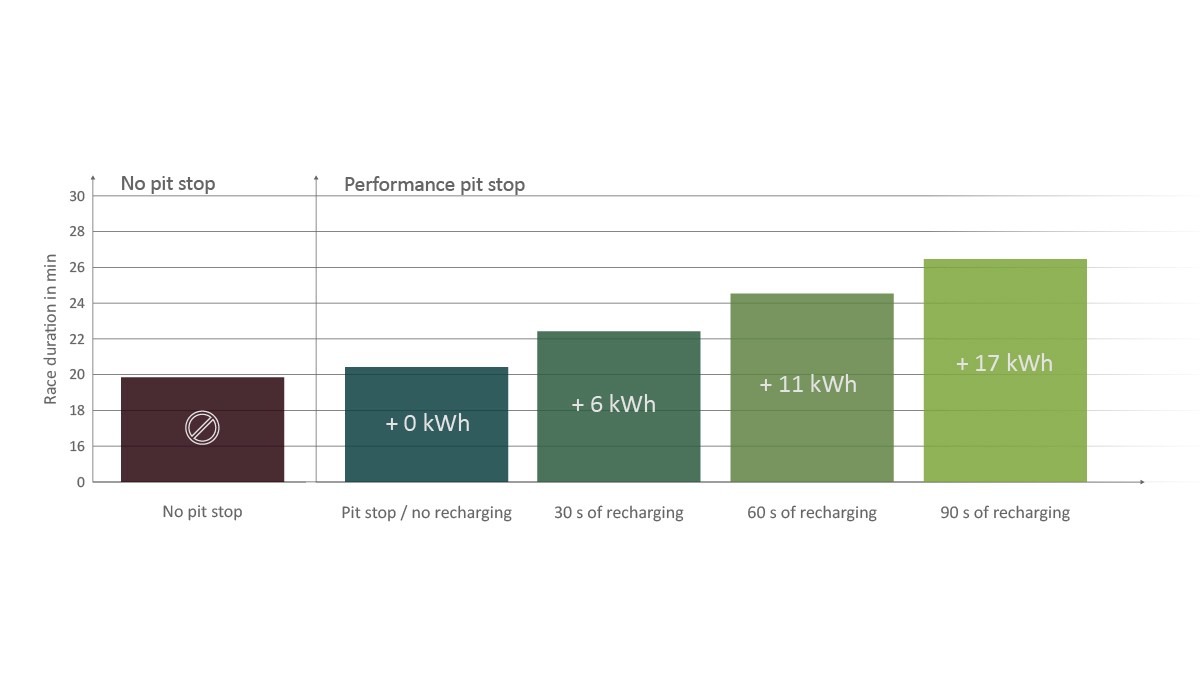
駆動システム
DTMエレクトリックには、シェフラーの標準駆動システムが搭載されている。これには、モータ、パワーエレクトロニクス、トランスミッション、サーマルマネージメントシステム、集中車両制御ユニットの駆動機能、ステアバイワイヤ技術が含まれる。部品や全体システムの開発では、フォーミュラE車両の駆動ユニットに関する豊富な経験と、シェフラーの開発部門の専門知識が活かされた。こうして、カスタマースポーツシリーズとしてのDTMエレクトリックの全体的経済コンセプトと融合する高性能パワートレインの開発が可能となった。
モータ
モータ(図9)は、高回転仕様で最大回転数は30,000 rpmである。中負荷域に重点を置く量産用途と比較して、モータースポーツ用電動モータは、駆動時もまたモータを発電機として使用するブレーキ回生時も全負荷状態となることが非常に多い。それにより設計の観点からみると、放熱やモータ制御など数多くの課題がある。モータ冷却システムは、モータ内部の熱を効率的に放熱させ、連続出力がピーク出力に近くなるように設計しなければならない。シェフラーは、オイルがステータのコイルの周りに直接流れるように設計し、コイルを直接オイルで冷却するシステムを搭載した。
シェフラーは、DTMエレクトリックの車両に4つの駆動システムというコンセプトを採用している。駆動トルクをホイールごとに配分してかけられるので、ホイール接地力が対称的でない場合には、1つないし2つの大型モータを使用する従来の方式より優れる。現行のコンフィギュレーションでは、4つのモータはそれぞれ以下の技術定格である。
- ピーク出力 > 300 kW
- トルク > 280 Nm (低温時)
- モータ最大回転数: 30,000 rpm
- モータ/パワーエレクトロニクス重量:約30 kg
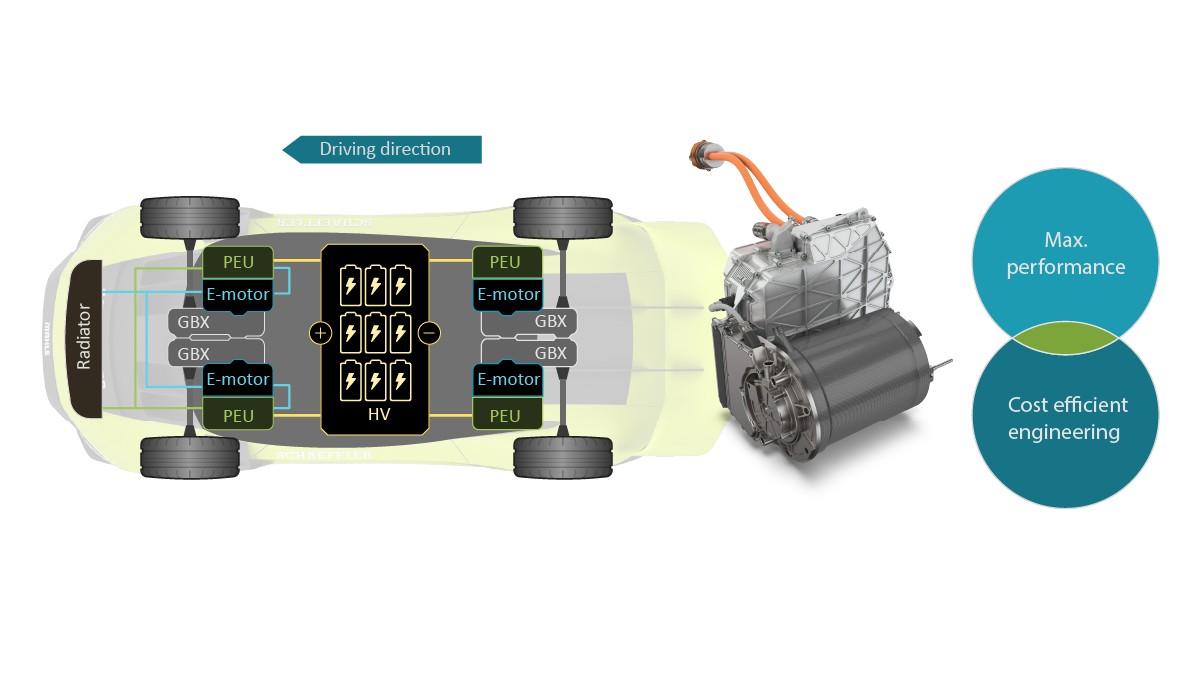
トランスミッション
ホイール毎にあるモータがトランスミッションを介して駆動力をホイールに伝達する(図10)。前後のアクスルは、2つのトランスミッションが単一モジュール化されているが、機械的には全く個別に動作する。ホイール間で可変的なトルク配分が可能で、すべて電子的に制御される。トランスミッションはモータとともに、システムの一部として設計される。モータの最大回転数とギヤ段数は、運転サイクルで高効率となるように調整される。フォーミュラEのパワートレインでの経験から、最大30,000 rpmまでのモータ回転数のシステムでは、2段変速トランスミッションが効率とパワーの最適な妥協点であることがわかっている。入力回転数が高いため、どのトランスミッション部品もモジュールとして設計する必要があり、ギヤと軸受も用途に合った特殊設計とする必要があった。シェフラーは、モータースポーツ用に特別に開発された「低損失ギヤリング」と呼ばれる方式を採用している。シャフト軸受には、高性能ハイブリッド軸受を採用した。セラミック製ボールと超高強度鋼を組み合わせることで、高い耐面圧と低摩擦を実現している。1モジュール(トランスミッション2つ)の重量は40 kg以下で、システム全体も非常に軽量である。
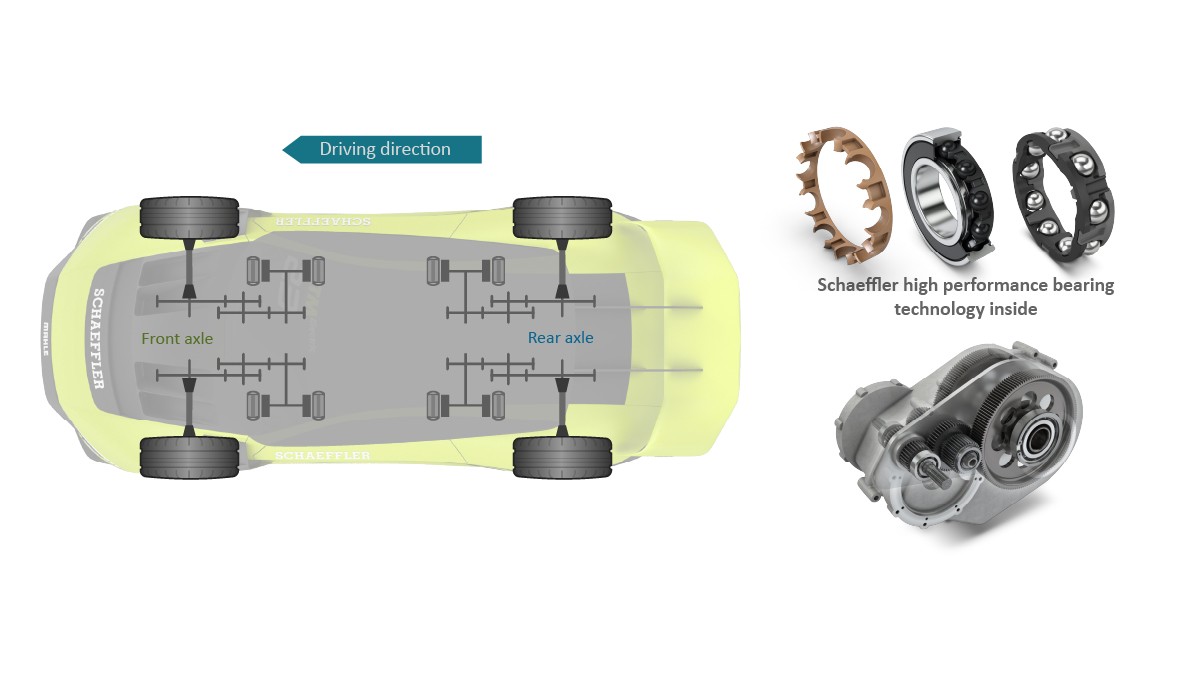
サーマルマネージメント
シェフラーは、システム全体レベルでのサーマルマネージメントシステムを開発し、その技術力に磨きをかけてきた。サーマルマネージメントには、個別部品から除去すべき熱量と個別部品に供給すべき熱量のバランスをとることのほか、システムアーキテクチャの設計、システム温度のマネージメント、冷却装置に必要な空気量の確保など、さまざまな要素が含まれる(図11)。車両全体の効率については、達成すべき冷却能力とエアロダイナミクス上の難点(空気抵抗が増すこと)との間でバランスをとる必要があった。すでにモータ冷却に導入されているオイルがクーラントとして冷却回路全体を循環するので、オイルから水性クーラントへの熱の伝達は必要なくなる。各モータ、トランスミッション、パワーエレクトロニクスアセンブリは共通の冷却回路をもち、この冷却回路はアクスルごとに連結されている。外気との熱交換は、車両前部にある2つの中央ラジエータ(フロントアクスル用とリアアクスル用に1つずつ)を通して行われる。アクティブ温度制御機構がコンポーネントを常に最適な動作温度に保つ。クーラント側の制御バルブのほか、ラジエータ入口の調節式エアフラップも使用して、フラップを開いたときには高い冷却能力を確保し、それ以外のときは閉じてエアロダイナミック効率を向上させる。バッテリの冷却は別回路で行われるため、駆動ユニットとは別に温度調節が可能である。

車載ソフトウェア
E/Eシステムのアーキテクチャは、中央制御ユニットがすべての車両機能を制御・管理している。中央制御ユニットは、ブレーキトルクの管理(回生ブレーキと機械式摩擦ブレーキの調整を含む)のほか、サーマルマネージメント、エネルギ消費や航続距離の予測、駆動制御とホイールトルクの分配も行う(図12)。「スマート」アクチュエータのコントローラは、アクチュエータ機能の制御、ローカルレベルでの診断、中央制御ユニットとの通信など、下位タスクを実行する。車両機能はソフトウェアだけで表示されるので、ソフトウェアのアップデートやパラメータの変更を全車両に容易に転送できる。セーフティカーが入った結果として残りラップ数が変わった場合などは、車両との無線リンクを利用してレース中に走行戦略を変更することも可能である。制動時の回生出力が非常に高いため、モータの回生モードや機械的ブレーキトルクと電気的ブレーキトルクの調整は、機能安全に関しては特別な要求が課される。故障が重大事故に直結する恐れがあるため、シェフラーはこの点を考慮して最先端技術を反映した複数のシステムセーフガード機構を実装している。
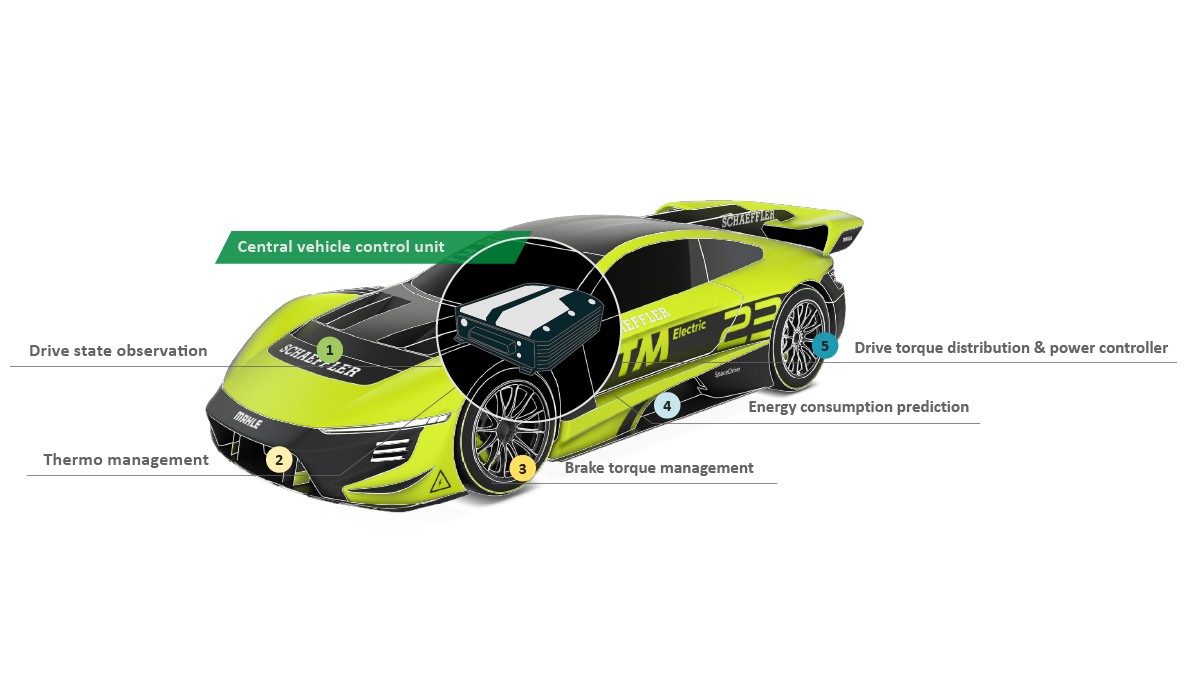
ステアバイワイヤ
シェフラーは、DTMと同様にDTMエレクトリック車両にも「Space Drive」ステアバイワイヤシステムを採用している。モータースポーツでのメリットは、車輪からステアリングホイールによってドライバーに伝わる衝撃を減衰させることにある。従来の機械式ステアリングシステムでは、衝撃が横方向のダイナミックコントロールを損ねる可能性がある。この現象が起きるのは、ドライバーがコーナリング中に縁石を超えるときである。ステアリングレシオを自由に設定できるのもメリットである。低速域での車両の俊敏性と高速域での走行安定性とを両立させることができる。ステアリングラックもソフトウェアを用いて、いつでもサーキット特性に合わせて調整可能である。
DTMエレクトリックのリモートラン
シェフラーのDTMエレクトリックのデモカーは、2020年秋に初めて披露された。2021年には、オーストリアのレッドブルリンクで印象的なデモンストレーションが行われた。このデモカーはレース速度でデモンストレーションラップを終えたが、この走行は無人で行われた。DTMチャンピオンのTim Heinemannが80 kmほど離れたグラーツから遠隔操作で車両を操縦したのである。彼がドライビングシミュレータに入力したコマンドは、光ファイバー接続とレッドブルリンクの携帯無線ネットワークを通じてサーキットのデモカーに送信された。車両制御が可能になったのは、ソフトウェアによる制御機構のほかに、ドライブバイワイヤ・ステアリングシステムによるところが大きい。さらに、ドライバーから見たサーキットビューを提供するカメラシステムと、車両ブレーキ用のバイワイヤ・ペダルシステムがこれに加わった(図13)。
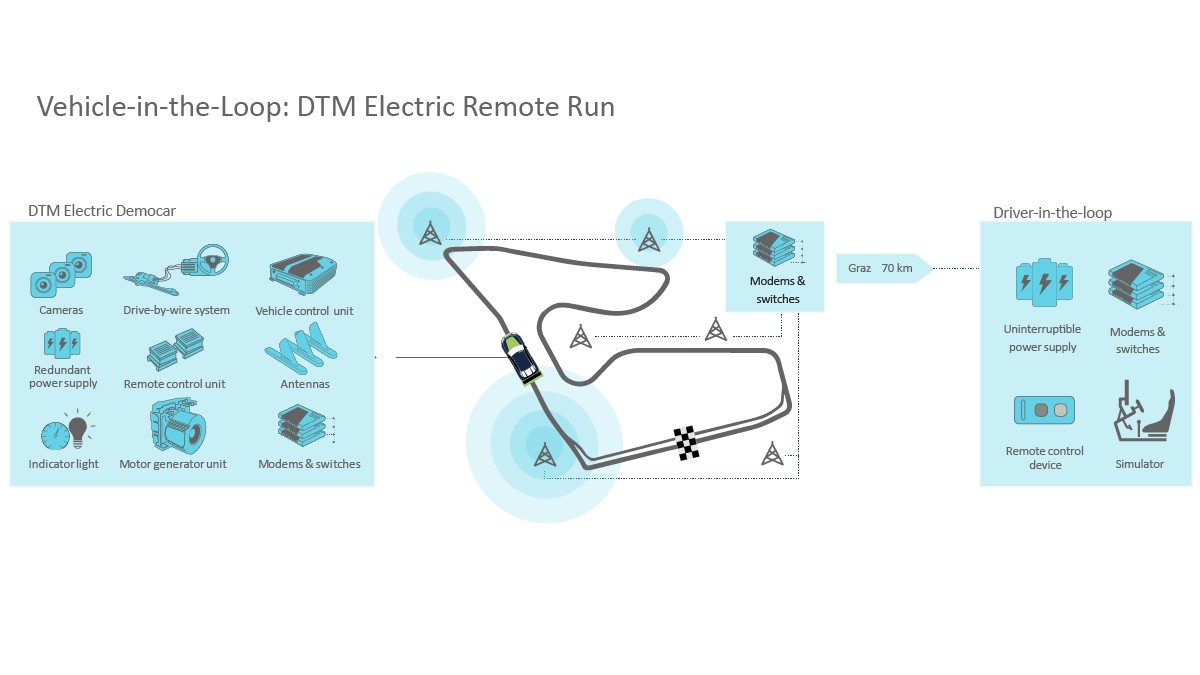
まとめ
シェフラーは過去何十年ものあいだ、さまざまな国際的なモータースポーツに関わってきた。モータースポーツと量産自動車部品開発の関わりは深く、これら2つの分野におけるノウハウや技術の共有が常に行われている。2020年後半以降、シェフラーはDTM(ドイツツーリングカー選手権)の公式シリーズ/イノベーションパートナーとして、DTMが計画する新たなレースシリーズ「DTMエレクトリック」の成功に向け、シェフラーが持つ技術や経験を積極的に活用してきた。シェフラーはこれまで、「DTMエレクトリック」向けの車両コンセプトを構築するため、駆動システム、ステアバイワイヤシステム、駆動系機能部品などの開発を手掛けてきた。将来的には、DTMエレクトリックシリーズに参戦するすべての車両に標準化した駆動システム、ステアリングシステムを供給する予定である。現在、公道を走行する電気自動車では搭載されるバッテリの航続距離延長が課題となっているが、電気自動車レースにおいてはバッテリ性能が直接レースの結果につながることとなり、さらに厳しい要求が課されることが予想される。この開発目標を達成するためには、非常に多くのパラメータを検討することが必要となり、優先度を正しく見極めながら開発を進めなければならない。バランスに優れた車両システムの実現に向け、シェフラーはDTMエレクトリックシリーズの開発では包括的開発手法を採用している。まず、物理的・技術的な基本原理の検証を実施した後、シミュレーションや性能試験の結果などをシステムレベルへ移行・反映させてゆく。こうした検討を基に、サブシステムや統合部品への要求を設定する。シェフラーは、タイヤのグリップ、駆動出力、および空力設計のパラメータを変化させた場合に、標準的なレース時間枠で達成可能なラップタイムに与える影響を調査し、その結果に沿って車両をさらに開発しました。
シェフラーはDTMエレクトリックの初代デモカーを2020年秋に発表し、2021年には「DTMエレクトリックリモートラン」イベントで2代目となるデモカーを披露した。この際には、実車走行によるライブデモンストレーションを行い、レース速度での無人走行を成功させている。この車両のリモートコントロールには「Space Drive」ステアバイワイヤ技術が活かされている。この新しいレース車両に搭載された各種システムは現在、開発・試験段階にある。2024年に開幕する新しいDTMエレクトリックレースシリーズに向け、2023年には最終コンセプトを発表する予定である。
[1] Feltz, C. et al.: Chassis Systems ─ Heading Toward Steer-By-Wire. Bühl: Schaeffler Kolloquium, 2022