燃料電池に関する取り組み 量産化への道
Benjamin Daniel, Dr. Mathias Reum
022年シンポジウムで、シェフラーはフォルクスワーゲン社の「e-Crafter」をベースとするデモカーを初公開する予定である。固体高分子形(PEM)燃料電池の普及に向けては、コストの大幅削減が鍵を握り、構成部品やサブシステムの量産化が前提となる。その実現のため、シェフラーは、構成部品のうち、金属製バイポーラプレート(双極板)モジュールの量産を、自社で一貫して行っている。
水素がモビリティに最適な理由
再生可能エネルギーへの移行は、世界各国で急速に進んでいる。国際エネルギー機関IEAは、2026年には世界の発電所への新規投資の95%近くが再生可能エネルギーによる発電への投資になると予測している[1]。これらの発電所は、ほぼすべてが太陽光発電と風力発電をベースとしている。このため、いかにして最大効率で蓄電し、24時間確実に給電するかが喫緊の課題となっている。エネルギー媒体として化学物質を用いることは、コスト効率の高い長期貯蔵手段としては理想的である。そのようなエネルギー媒体の中では、水素が最も高い変換効率を有する。水素は電気分解によって70%~80%の効率で生産できる。現在、化学工業や製鉄業界で使用されている化石燃料由来の水素とは異なり、この「グリーン」水素は完全にカーボンニュートラルであり、世界のエネルギー転換の重要要素となっている。
モビリティの動力源としてのグリーン水素利用は、グリーン電力の直接利用と比較し3つのメリットがある。
第一に、高いエネルギー貯蔵密度によって長い航続距離を実現できる点である。バッテリ技術の進歩は著しいが、図1に示すように、水素燃料電池自動車(FCEV)は、貯蔵できるエネルギー密度において、依然としてバッテリ電気自動車(BEV)よりも優れている。FCEVの水素タンクシステムの体積エネルギー密度は、同程度の航続距離を持つBEVのリチウムイオン電池の約2.4倍である[2]。また、水素タンクシステムの重量エネルギー密度は1.84 kWh/kgであるが、リチウムイオン電池はその15%にすぎない。BEVの駆動効率が向上しても、この差を埋めるには至らない。車両が大型化するほど、また長距離走行性能を重視するほど、このエネルギー密度のメリットは際立つ。
![図1 水素タンクとリチウムイオン電池の体積エネルギー密度(左)と重量エネルギー密度(右)の比較。国際エネルギー機関(IEA)による[1]。](https://www.schaeffler.co.jp/remotemedien/media/_shared_media_rwd/06_press/press_kits_events/kolloquium_2022/digital_conference_book/fuel_cell/16_9-schaeffler-kolloquium-2022-fuel-cells_01_rwd_1200.jpg)
水素の第二のメリットは、充填時間が短いことである。これは商用車にとって特に重要である。何故なら、事業者にとって商用車は工作機械と同様に稼働率が損益に影響するからである。大型トラックの燃料補給時間を比較すると、ディーゼル車では100 km走行に必要な給油時間は約22秒である。水素をFCEVに充填する場合は90秒である。一方、BEVの場合、350 kWの超高速充電器で充電しても1,400秒すなわち20分以上かかる。話題になることの多いメガワット級充電器を使っても、約500秒かかる。また、充電時間が長いほど、一定時間内に充電できる車両数は減少する。例えば、1台の350 kW超高速充電器では、1日に満充電できるBEVトラックの台数は5台程度にすぎない。それが、水素充填用のディスペンサになると約70台のFCEVトラックの充填が可能だ。
第三に、電力インフラへの影響を抑えられるメリットが挙げられる。国際エネルギー機関(IEA)は、持続可能な開発シナリオにおいて、電動モビリティのために197 TWhの電力量が必要になると予測している[3]。この一部を水素でまかなうことができれば、電力インフラへの負担を抑えることができる。市場調査会社Frost & Sullivan社は、2030年までにグリーン水素生産量が190 TWhのエネルギーに匹敵する5.7 Mtに達すると予測している[4]。
こうした理由から、FCEVはBEVと競合するものではなく、むしろ運輸部門における持続可能で気候中立なエネルギー供給への転換を加速させるのに役立つと考えるべきである。燃料電池パワートレインは、まず都市間輸送用の商用車(トラック、長距離バス)で利用されるだろう(図2)。さらに、水素の製造・流通インフラが整備されれば、比較的長距離を走行する大型乗用車やワゴン車も水素燃料電池パワートレインのメリットを享受できるようになる。
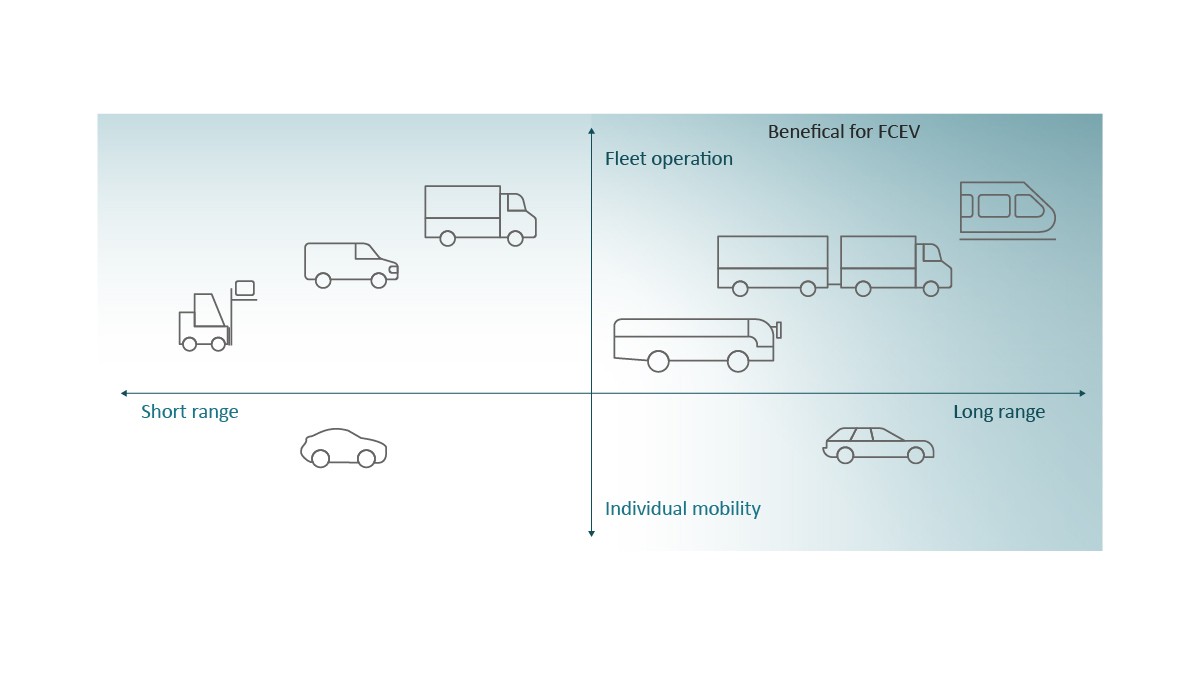
量産化に向けて
燃料電池は製造コストが高く大量生産できないことが自動車に採用する上でネックとなっている。製造コスト低減の鍵は、重要部品やサブシステムの効率的な生産規模拡大である。図3はシェフラーによる製品開発ポートフォリオを示す。シェフラーは、システムやパワートレインレベルの開発プラットフォームで得たシステム統合ノウハウを生かし、お客様の要求に合わせた部品やサブシステムの製品開発を進めることができる。また、シミュレーションを各レベルで実施することで、設計の最適化や生産性の向上を支援することができる。
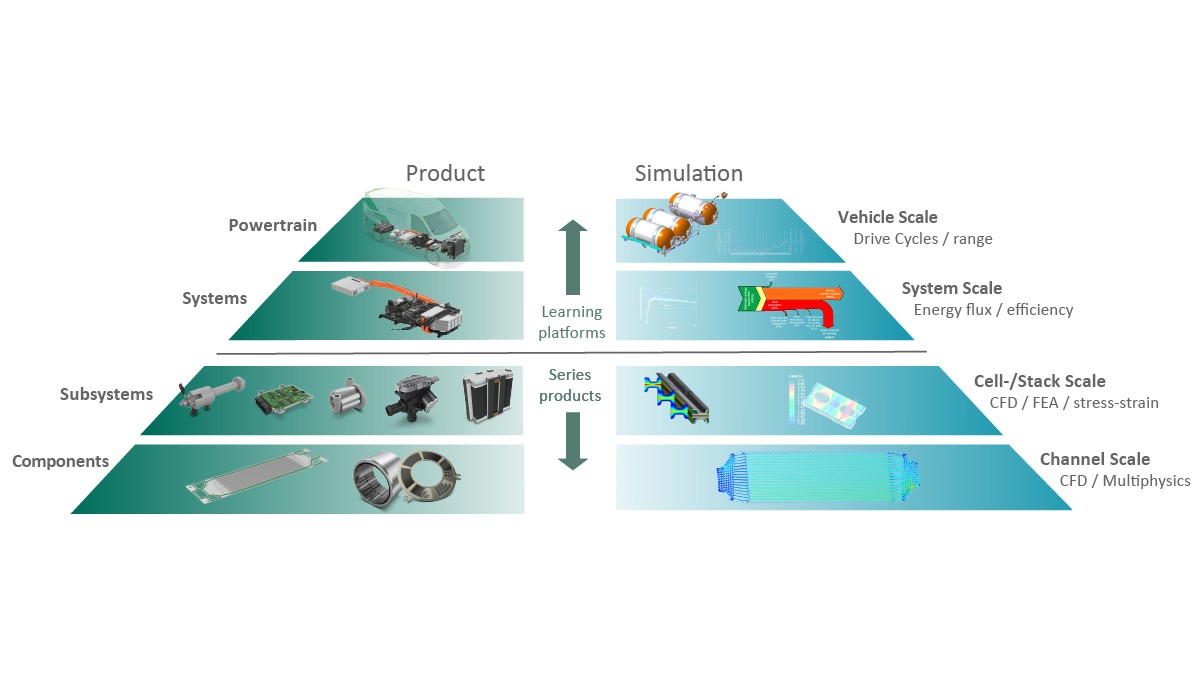
燃料電池スタックは、膜/電極接合体(MEA)、バイポーラプレートモジュール、エンドプレート、マニホールド、およびクランプ装置で構成される。スタックを機能させるには、水素、空気、冷却水の3つの流体制御が必要である。各流体系統には一連のサブコンポーネントがあり、電子・電気部品と合わせてバランスオブプラント(BoP)と呼ばれる。以下に開発中のBoP部品やモジュールについて紹介する。
高効率スタックを実現するバイポーラプレート
バイポーラプレートは、PEM燃料電池の重要部品である。スタック重量の80%、容積の65%を占め、スタックの出力密度に影響を及ぼす。また、バイポーラプレートの重要な機能として、生成水の除去、発生電流のセル間伝導や、冷却水の均一分配が挙げられる。
バイポーラプレートには、一般的にグラファイト製または金属製の2種類が市場に存在する。シェフラーは、金属製に以下3つの観点での優位性があると考えている。
第一に、セルの厚さを薄くできる点がある。スタック全体の容積は主にバイポーラプレートの板厚によって決まる。グラファイト製では、チャネル構造間の板厚は700~800 mmとなり、セル間距離は3 mm以上となる。金属製なら、これを50~100 mmまで薄くすることができ、セル間距離を1 mm未満にできる。
第二に、金属の特性による利点が挙げられる。金属製の方が、グラファイト製より導電性が高いため、電気抵抗によるロスを最小化することができる。さらに、金属製の方がプレート内の水素透過を防ぐことができる(図4)。
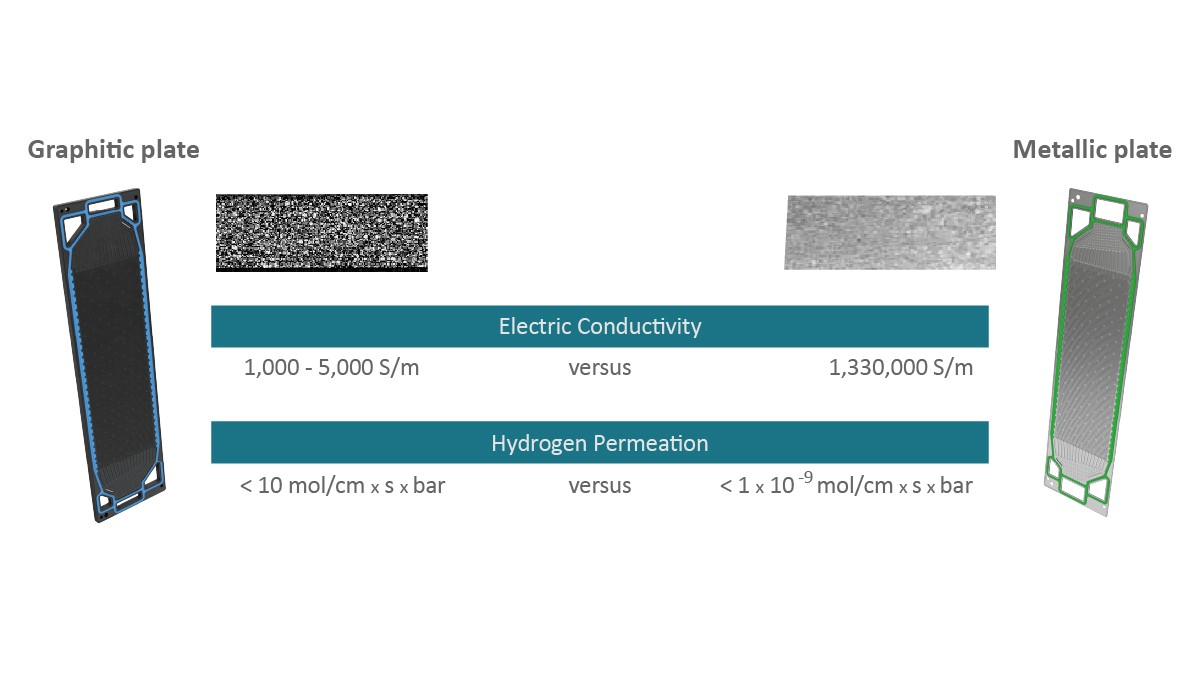
第三に、取り扱いや生産性の優位性が挙げられる。グラファイト製は衝撃に弱く、取り扱いに注意が必要なため、生産工程における制約が生じる。また、生産サイクルタイムの観点からも、1部品(コーティングを含む)あたりの製造時間を1分未満にするには、グラファイト製は金属製より大きな生産スペースを必要とする。
シェフラーの金属バイポーラプレートモジュールの技術的特長は、独自のコーティングにある。コーティングの目的は、使用期間全体を通じて高導電性を維持し、金属イオンの溶出を防止することである。金属イオンは、活性触媒やプロトン交換膜に経時的に蓄積し、MEAを劣化させる。シェフラーは現在、バイポーラプレートモジュール用に複数のコーティング方式を「Enertect」シリーズとして開発している。白金族金属(PGM)を母材とし、高い耐用年数要件に対応するものと、低コスト炭素コーティングをベースとするものがある(図5)。シェフラーは、要求性能とコストのバランスを図りながら、顧客の用途に応じたコーティング方法の開発・提案を行っている。コーティングは、物理的気相成長法(PVD)を用いおり、この技術は既に高負荷を受けるバルブトレイン部品にて量産の実績がある。
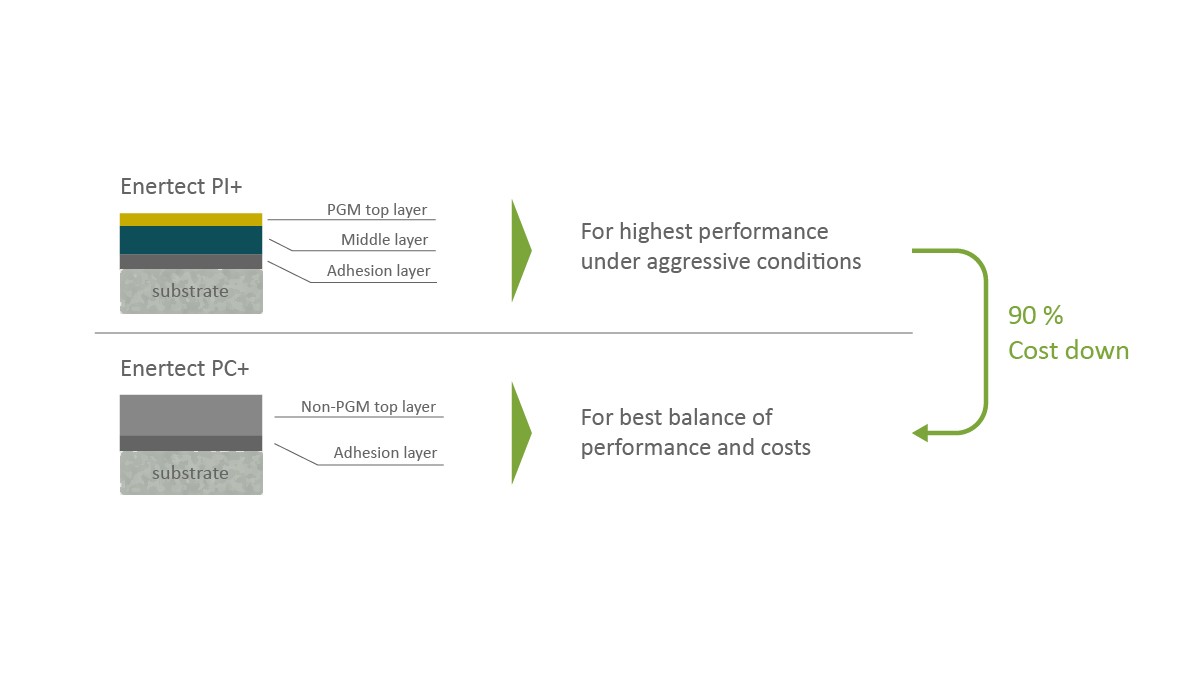
現在のバイポーラプレートモジュールのサプライチェーンは複雑である。燃料電池メーカーは内外のサプライヤーに依存しており、サプライヤー各社が担当するのは製造工程全体の一部にすぎない。バイポーラプレートは、自社生産設備で工程をリンクさせることで、高品質の製品をスケーラブルに安定して製造することが可能となる。
シェフラーは、自社ソリューションによるバイポーラプレートの量産性を実証するため、2022年にヘルツォーゲンアウラッハ(ドイツ)本社にパイロットプラントを立ち上げた。同プラントの車載用燃料電池バイポーラプレートモジュールの年間生産能力は、700,000個を上回る。また、同プラントは水電解スタック用の大型バイポーラプレート(最大寸法1800 x 600 mm)も生産可能である。シェフラーの特殊機械部門が設計した同プラントでは、各工程はほぼ完全自動化されている。
燃料電池の効率を支えるサブシステム
燃料電池の効率は、主としてスタックとBoPによって決まる。
空気の供給
燃料電池への空気供給は、高速電動ターボコンプレッサで行われる。自動車用燃料電池の空気経路におけるコンプレッサでは、最高200,000 rpmで数千時間の寿命が要求される。また、燃料電池に供給する空気には清浄度が要求され、オイルやグリースによる潤滑ができないため、軸受損傷の防止方法が重要となる。シェフラーは軸受製造のノウハウを活用して、コンプレッサ用のエアフォイル軸受を開発した[5]。空気軸受の設計では、軸受リングとシャフト(コンプレッサ駆動部ロータ)間でリング側に突起フォイルを取り付ける(図6)。フォイルは比較的高速でシャフトから浮き上がるので、無摩擦・無潤滑の運転が可能である。しかも、この設計原理ではあらゆる運転状態で(ロータが静止しているときでも)ロータとステータが機械的に接触することはない。
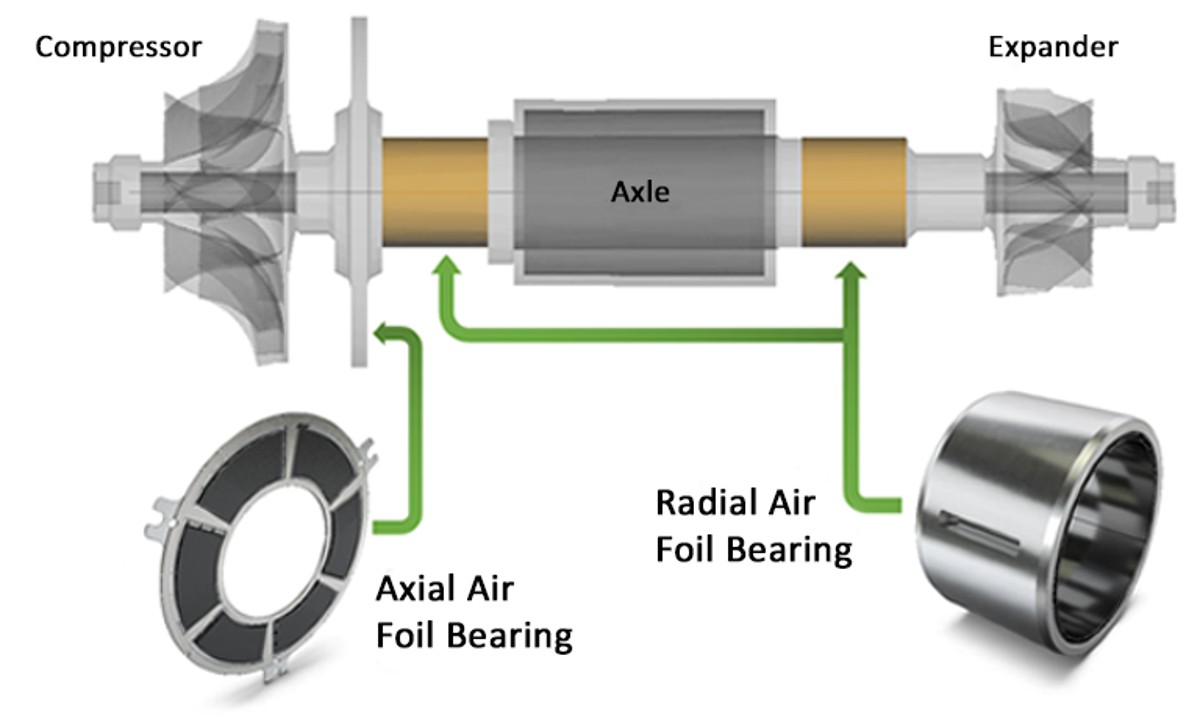
シェフラーは、自社軸受ノウハウと電気的知見を総合的に活用することで、電動モータとパワーエレクトロニクスを統合したコンパクトで高品質なドライブユニットを実現した。シェフラーは、パートナーであるTTI社よりコンプレッサホイールのノウハウ提供を受けており、コンプレッサ完成品を設計・製造することも可能である(図7)。現在、60 kWと120 kWの2種類の燃料電池出力に応じたコンプレッサを開発中で、2023年半ばに最初のプロトタイプが完成予定である。
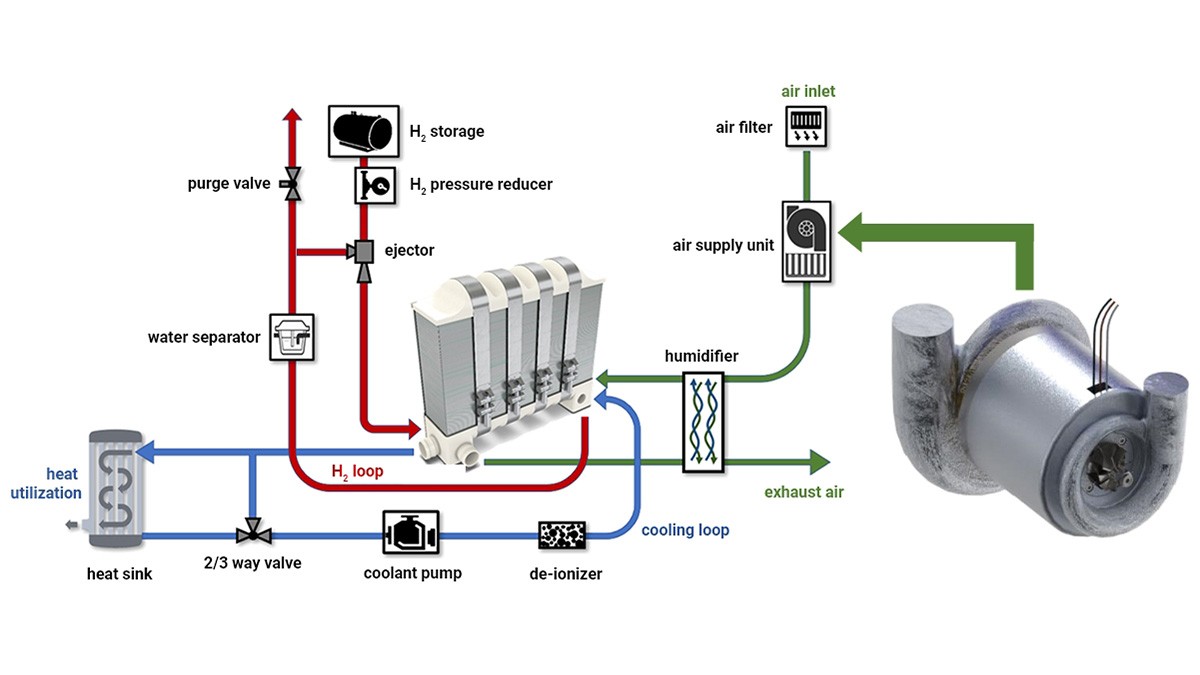
水素の循環
水素経路では、未使用水素を燃料電池の入口に戻す循環の効率が重要となる。理論的にはポンプを連続運転して多量に循環させればよいが、その場合、エネルギー効率が悪化する問題がある。シェフラーは、ノズルを調節してベンチュリ効果で受動循環させる、エネルギー効率がよく、スペースもとらない水素循環エジェクタを開発中である。残留水素の循環には、運転負荷に応じた設計ソリューションがあり、これまで、多段ノズルや調節式ノズルに関する研究が行われてきた。シェフラーで、集中的なCFDシミュレーションを行い、図8のような調節式2段ノズルで最も高い費用対効果が得られることを確認した。また、ノズルは内燃機関における高圧燃料噴射と同様、長期間にわたり安定して精密な流量制御を行う必要がある。シェフラーが顧客の協力を得て実施した台上試験において、前記ノズルがこの要件を満たすことを確認した。
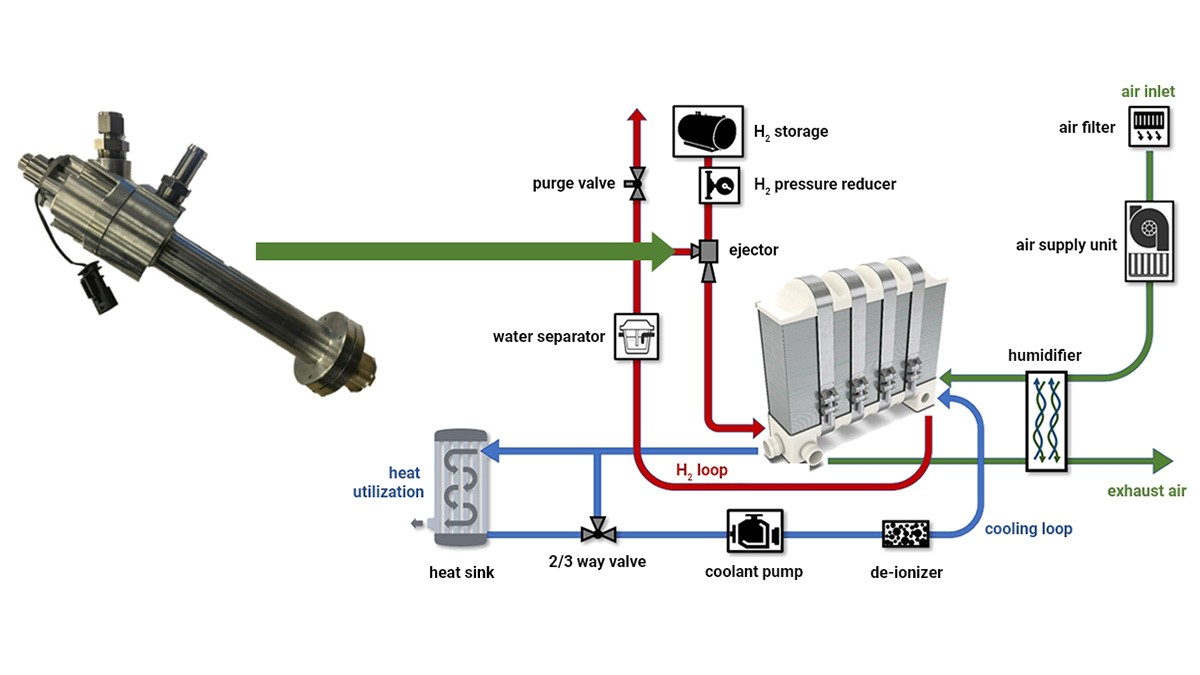
冷却水の管理
T電気化学プロセスの効率は、温度が一定の範囲内にあるかどうかに左右される。燃料電池の使用温度範囲はリチウムイオン電池よりも広いが、それでも多量の熱を放出する必要がある。燃料電池パワートレインで冷却水管理が非常に重要なのはこのためである。図9に示すように、標準化された切り替え式バルブを使用することで、冷却回路の構造を大幅に簡素化することができる。
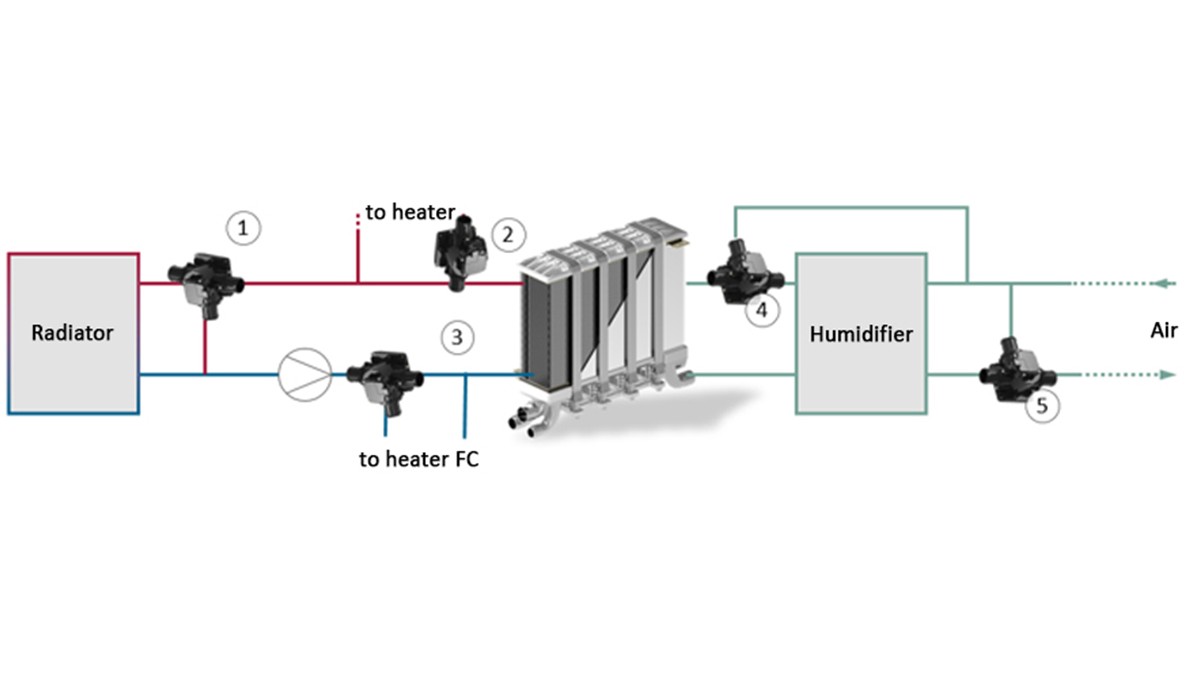
シェフラーは冷却水管理のために、エンジン車向けに100万個以上の供給実績を持つサーマルマネージメントモジュール(TMM)、またはシングルスマートバルブ(SSV)を提供している。また、加湿器やインタークーラをバイパスする空気経路向けに、同様のコンポーネントを提供することも可能である。
制御
最終的な燃料電池の効率は、個別サブシステム設計の他、システム制御によっても決まる。シェフラーのPROtroniC TopLINEは、プロトタイプや少量生産に最適であることが実証されたスケーラブルな制御装置ハードウェアである。さらに、シェフラーは、水素漏れ監視など、燃料電池特有の機能を盛り込んだファームウェア用のソフトウェアモジュールも開発した。
開発プラットフォームとしての燃料電池システム
部品やサブシステムは最初から燃料電池システム全体の機能に合わせて設計するのが合理的である。そこでシェフラーは、学習プラットフォームとして車載用燃料電池の完全なシステムを自社開発した。完全なシステムを使って試験を行うことで、シミュレーションツールを最適化することができる。とくに摩耗や経年劣化等の挙動を確実に予測することは、重要な研究課題である。
シェフラーは、フォルクスワーゲン社のデリバリーバン「e-Crafter」をベースに、図10に示すようなデモカーを製作した。デモカーには、50 kWの連続運転が可能な燃料電池システムと、フォルクスワーゲン社の他モデルから流用した最大出力85 kW、13 kWhのバッテリを搭載している。駆動系にはシェフラーの機電一体型電動アクスルを使用し、最大出力140 kWを誇る。
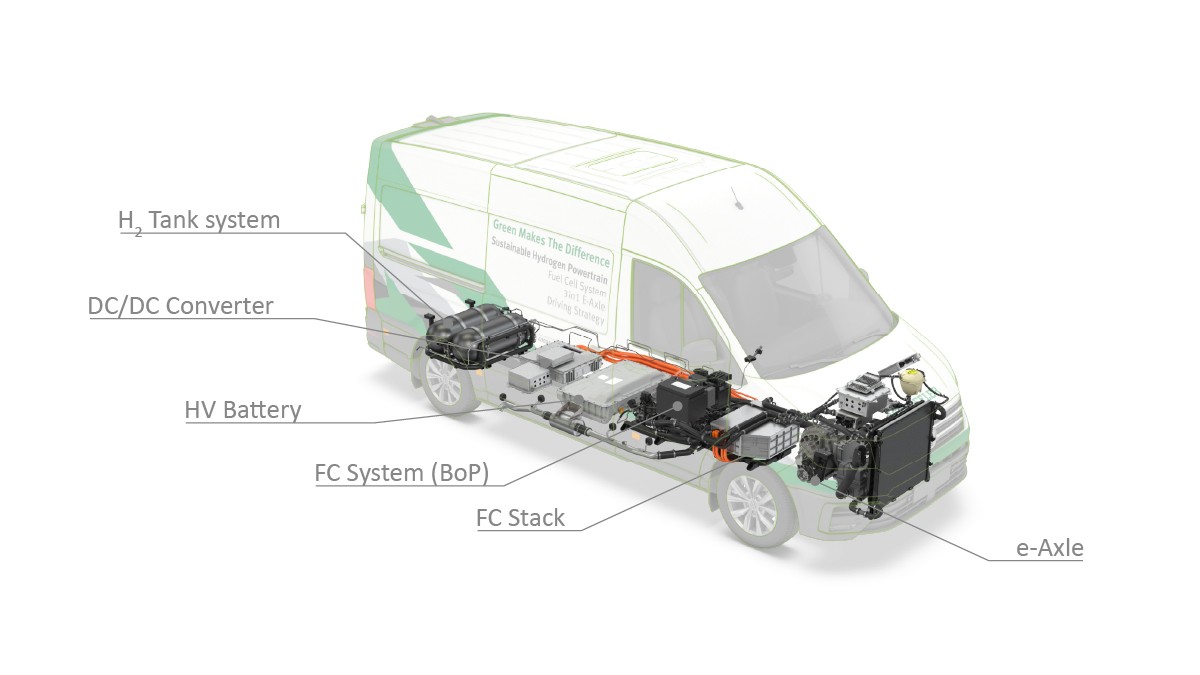
商用車では車両重量の増加にともなって公称出力と連続出力の要求値の開きが大きくなり、出力変動の少ない燃料電池を用いた構成が有利となる。シェフラーは今後、提示したコンセプトをさらに最適化する予定で、例えば電動アクスルドライブを車両のリアアクスルに移動させて、フロントエンドに燃料電池システムを搭載することを検討している。こうすることで、アンダーボディにさらに水素タンクを搭載するスペースが生まれる。また、燃料電池の性能を向上させることで、バッテリをさらに小型化しながら、高い動的性能要件を満たすことも可能になる。
まとめ
高いエネルギー密度と短い充電時間というメリットを持った水素燃料電池は、エネルギーインフラの将来像を踏まえると、バッテリ式電動パワートレインを補完する有望な技術になることが期待される。重要部品やサブシステムの量産化により、シェフラーは燃料電池システムの製造コスト低減に確実に貢献していく。
部品レベルでは、量産仕様のバイポーラプレート(双極板)モジュールを開発している。この金属製プレートの大きな特徴は、シェフラーが独自に開発したコーティングシステムにあり、高導電性を維持し、金属イオンの溶出を防ぐことで、製品寿命の延長を可能にする。また、サブシステムレベルでは、燃料電池の性能や耐久性を大きく左右する流体の制御に関わる部品を開発しており、空気経路について、シェフラーは摩擦のない、潤滑剤不要のエアフォイル軸受を搭載したコンプレッサを手掛けている。水素経路については、高精度な流体制御を実現する水素循環エジェクタの開発が進行中である。このほか、シェフラーは燃料電池システムのサーマルマネージメントや電子制御ユニット、プロトタイプスタックモジュールの開発にも取り組んでいる。さらに、開発プラットフォームとして、シェフラー製スタックを備えた燃料電池システムを、フォルクスワーゲン社「Crafter」をベースにしたデモカーに搭載した。
シェフラーは、バイポーラプレートモジュールの量産から、システムを搭載した車両実験にいたるまで、開発のあらゆる要素に対応する能力を備え、燃料電池の迅速な量産化を支えている。この規模拡大が成功すれば、クライメイト・ニュートラル(気候中立)なモビリティの選択肢がまたひとつ増えることになる。
[1] International Energy Agency (Hrsg.): Renewables 2021: Analyses and forecast to 2026. Revised version. Paris, 2021. https://iea.blob.core.windows.net/assets/5ae32253-7409-4f9a-a91d-1493ffb9777a/Renewables2021-Analysisandforecastto2026.pdf
[2] Handwerker, M. et al.: Comparison of Hydrogen Powertrains with the Battery Powered Electric Vehicle and Investigation of Small-Scale Local Hydrogen Production Using Renewable Energy. In: Hydrogen (2021) Nr. 2, S. 76-100, doi: 10.3390/hydrogen2010005
[3] International Energy Agency (Hrsg.): Global EV Outlook 2021. https://www.iea.org/reports/global-ev-outlook-2021/prospects-for-electric-vehicle-deployment
[4] Frost & Sullivan (Hrsg.): Global Green Hydrogen Production Set to Reach 5.7 Million Tons by 2030, Powered by Decarbonization. https://www.frost.com/news/global-green-hydrogen-production-set-to-reach-5-7-million-tons-by-2030-powered-by-decarbonization/
[5] Schutzrecht EP 3099951B1: Aerodynamisches Luftlager und Verfahren zu dessen Herstellung. 2019
[6] Rosenfeld, D. C. et al.: Comparison of advanced fuels. Which technology can win from the life cycle perspective? In: Journal of Cleaner Production 238 (2019), doi: 10.1016/j.jclepro.2019.117879
[7] Sternberg, A. et al.: Greenhouse Gas Emissions for Battery Electric and Fuel Cell Electric Vehicles with Ranges over 300 Kilometers. Freiburg: Fraunhofer ISE, 2019. https://www.ise.fraunhofer.de/content/dam/ise/en/documents/News/190815_LCA-BEV-FCEV_Results_EnglishVersion.pdf
[8] FVV (Hrsg.): Zukünftige Kraftstoffe: FVV-Kraftstoffstudie IV. Frankfurt am Main, 2021. https://www.fvv-net.de/fileadmin/user_upload/medien/download/FVV__Future_Fuels__StudyIV_The_Transformation_of_Mobility__H1269_2021-10__EN.pdf