革新的モータおよびパワーエレクトロニクスの効率的な生産 コストパフォーマンスと汎用性の両立
Thomas Pfund
ハイブリッドモジュール、ハイブリッド専用トランスミッション、電動アクスルなど、すべてに使用可能な標準モータの実現。これは、しかし、各部品の使用条件が大きく異なっており決して現実的とはいえない。シェフラーは、幅広い車両と多くの市場に対応できるモータを生産するためのフレキシブル&低コストの技術プラットフォームを開発した。このプラットフォームによって、量産化に対応した生産設備の迅速な増強が実現できる。同時に、モータのアジャイル生産技術を試すためのパイロットプラントを世界に先駆けてビュール(ドイツ)に建設中である。プロセスのイノベーションと製品イノベーションは相互に補完・促進し合う。本稿で述べるように、それはアキシャル型モータのような新型モータだけでなく、99%以上の効率を誇るパワーエレクトロニクス技術の開発によるところが大きい。
生産規模拡大の現状
シェフラーは2018年のシンポジウムにおいて、電動パワートレイン向け統合プラットフォームを提案した。2018年の技術論文[1]で、「電気自動車の今後10年内の生産量急増、機械工学と電子工学の著しい融合と進化」を予測した。当時すでに出現していた多種多様なパワートレインに対応して、開発が進んでいたモータ、パワーエレクトロニクス技術、ソフトウェア、総合的システムソリューションについても紹介した(図1)。もっとも、4年前は全電動パワートレイン量産に向けた生産規模の拡大はまだ始まったばかりだった。
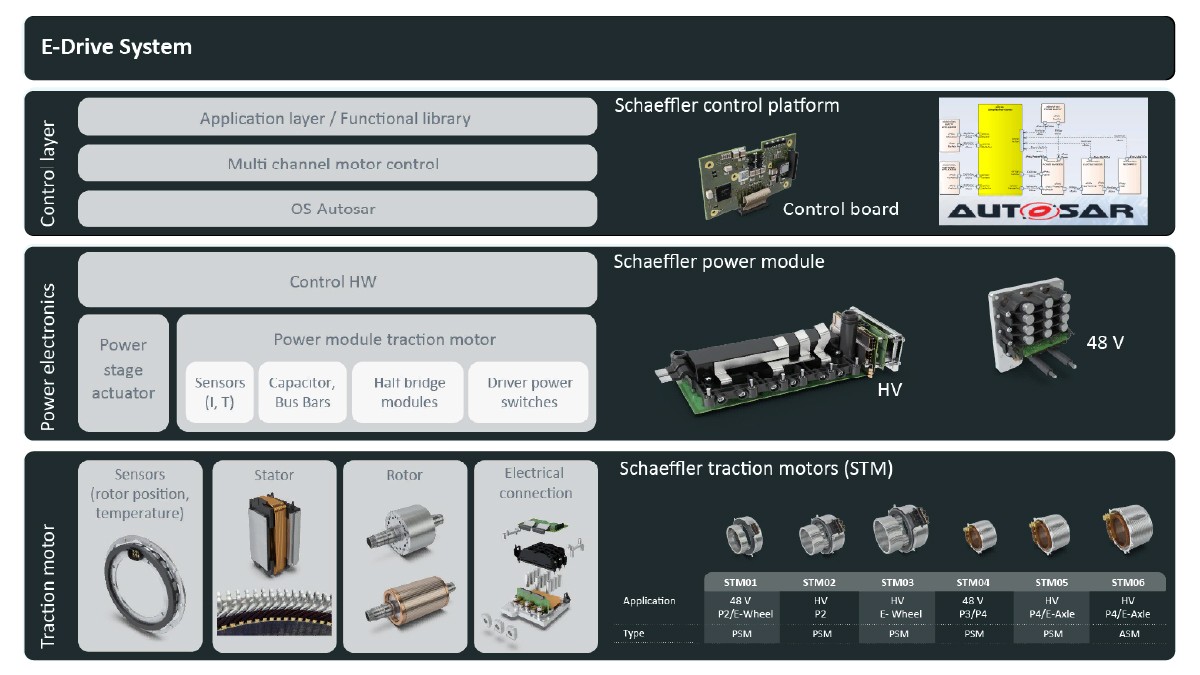
シェフラーは過去4年間にわたり、革新的製品の開発およびコンポーネントやシステムの生産プロセス効率化に注力し、電動パワートレインのフレキシブルな量産実現を目指してきた。生産ステップごとに適切な技術が選択・試験され、生産技術プラットフォームに投入される(図2)。
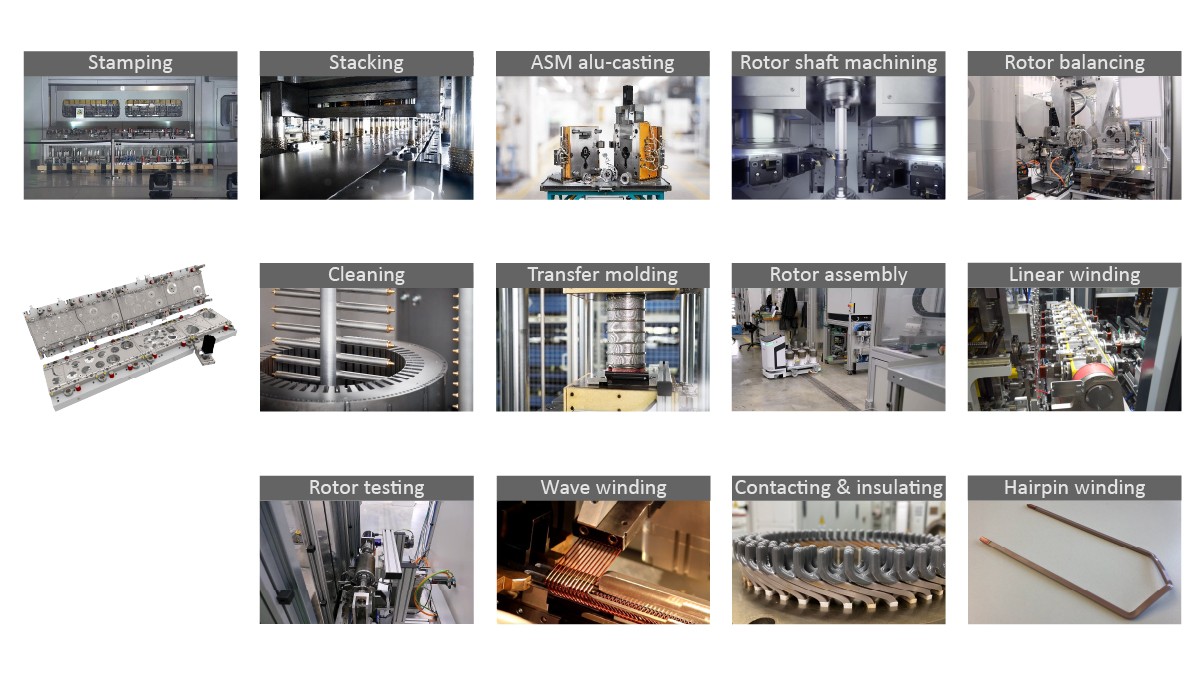
高度に自動化された生産設備の「効率化」と「柔軟性」を同時に達成する方法として、プレス加工に関するツーリングコンセプトをあげることができる。あらゆる種類の製品について、高度な資源再利用と段取りプロセスの自由度を実現するため、シェフラーは、社内ツール制作部門の支援を得てモジュール方式の複列コンセプトを開発した。いわゆる累進プレス加工法を用いて、モータのロータとステータの積層鋼板の1サイクルプレス加工を実現し、板金使用の最適化によりスクラップ発生を最小限にすることができる。巻線プロセスにも高度の柔軟性が要求される。集中巻(single tooth winding)だけでなく、セグメント方式(hairpin winding)や連続波巻(continuous hairpin winding)など、他の確立された方法への対応も必要である。2018年後半、シェフラーは巻線機メーカーElmotec Statomat社を買収し、巻線技術の専門知識を大きく拡大した。シェフラーでは、永久磁石モータ用ロータ製造にトランスファーモールディングを採用している。トランスファーモールディングは、射出された熱硬化性樹脂で磁石をカプセルのように包み込んで硬化する。磁性材料を完全にカプセル封入することで環境による影響を回避でき、表面安定化処理や複雑な表面処理が不要となる。非同期モータ製造に必要なプロセスも、技術プラットフォームの対象である。かご型ロータのアルミダイカストなどが代表例である。
シェフラーは長年にわたって、「地域に根ざし、地域のために」をモットーとする価値創造戦略を推進してきた。技術プラットフォームはグローバルな展開が可能で、技術と生産設備は世界各国で標準化されている。この戦略によって、各地域での生産量変動に対して柔軟に対応できる。シェフラーは2026年度までに総額5億ユーロを超える資金を投じて、ビュール(ドイツ)、ソンバトヘイ(ハンガリー)、太倉(中国)、ウースター(アメリカ)、プエブラ(メキシコ)の各工場で生産体制を構築する。ビュール工場はパイロットプラントの役割を担い、モータのアジャイル生産向けの新技術の開発を行う。ビュール工場で少量生産技術試験を実施、その後、各国の工場に展開する。
多様なアプリケーション
シェフラーが現在製造しているモータと、今後製造するモータは、種類だけでなく設計や仕様においても大きく異なる(図3)。モータの製品ラインナップが多い理由は、車両とパワートレインの種類が多様であるからである。電動パワートレインは、電動アクスル、ハイブリッド専用トランスミッション、ハイブリッドモジュールなどに分類できる。
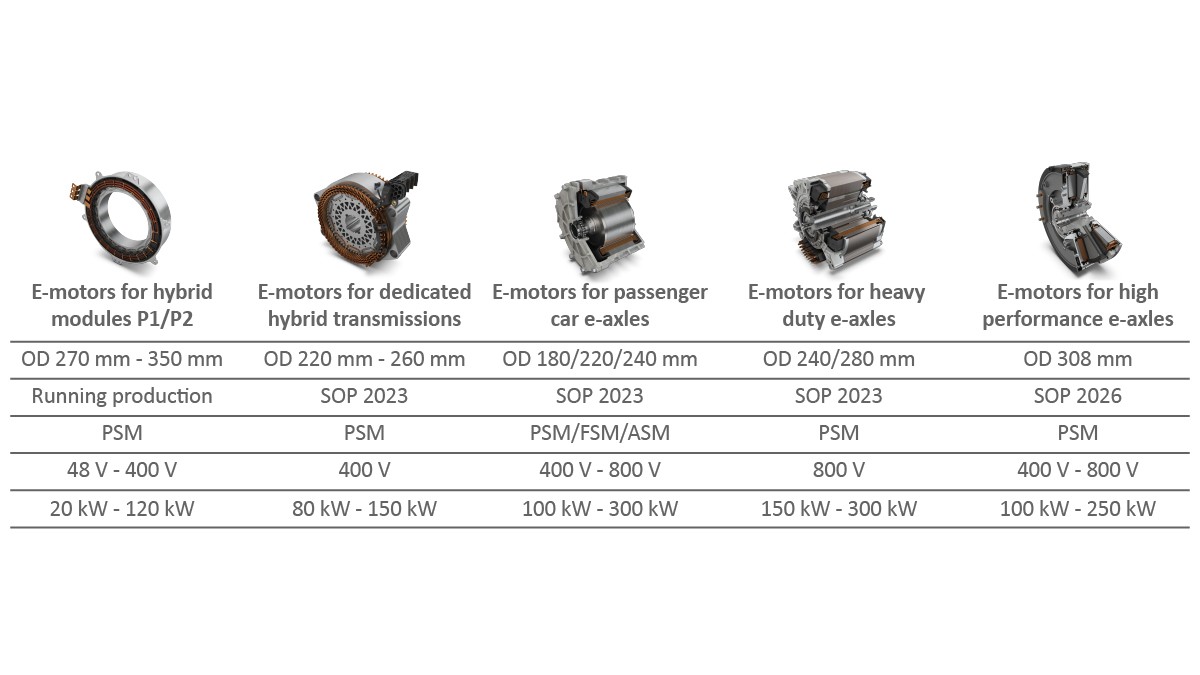
モータ種類や選定は、システムレベルの必要条件によって決まる。ハイブリッドモジュールの場合、搭載スペースが重要となる。モータだけでなく、1つ(または複数)のクラッチを内燃エンジンとトランスミッション間の狭い空間に配置する必要があるからである。軸長は概して小さいが、直径は比較的大きい。これは巻線が集中巻であることを示す。シェフラーが開発した巻線は、圧縮成形により、高占積率の達成が可能である。特殊なモータ設計、巻線工程とその後の圧縮により軸長34 mmのモータで97.3%の効率を実現している。従来モータでは実現は不可能である。軸長が長いモータは、分布巻(distributed windings)を使用している。分布巻は従来のセグメント方式や連続波巻として実施できる。
個別技術は、システム全体に基づいて選定する。例えば、電動アクスルに永久磁石同期モータ(PSM)を使用するか非同期モータを使用するか判断する必要がある。永久磁石モータは出力密度が高く、メインドライブアクスルにとって魅力的な選択肢である。状況によって切替え可能な四輪駆動を実現するために、2本目の電動アクスルを追加搭載することが必要である。この場合は非同期モータが有利といえる。理由は、引きずりトルクがなくパワートレインの全体効率が向上するからである。磁石を使用せずに高出力密度を達成する必要がある場合は、巻線界磁形モータが選択肢となる。シェフラーの技術プラットフォームでは、同ステータを用いて、異なるタイプのロータを組み合わせることで当該モータを使用することが可能となる。
パワートレインのコンセプトによっては、使用トルク・速度特性マップ領域が大きく異なる場合がある(図4)。P1またはP2のハイブリッドモジュールは、発電モードで稼働することが多い。ハイブリッド専用トランスミッションにおいてクランクシャフト側モータとして動作する第1モータ等である。一方、第2モータは主にトラクションドライブに使用される。電動アクスルは、一般に運転サイクル全体、高速走行を含む実際の運転状況に対応している。
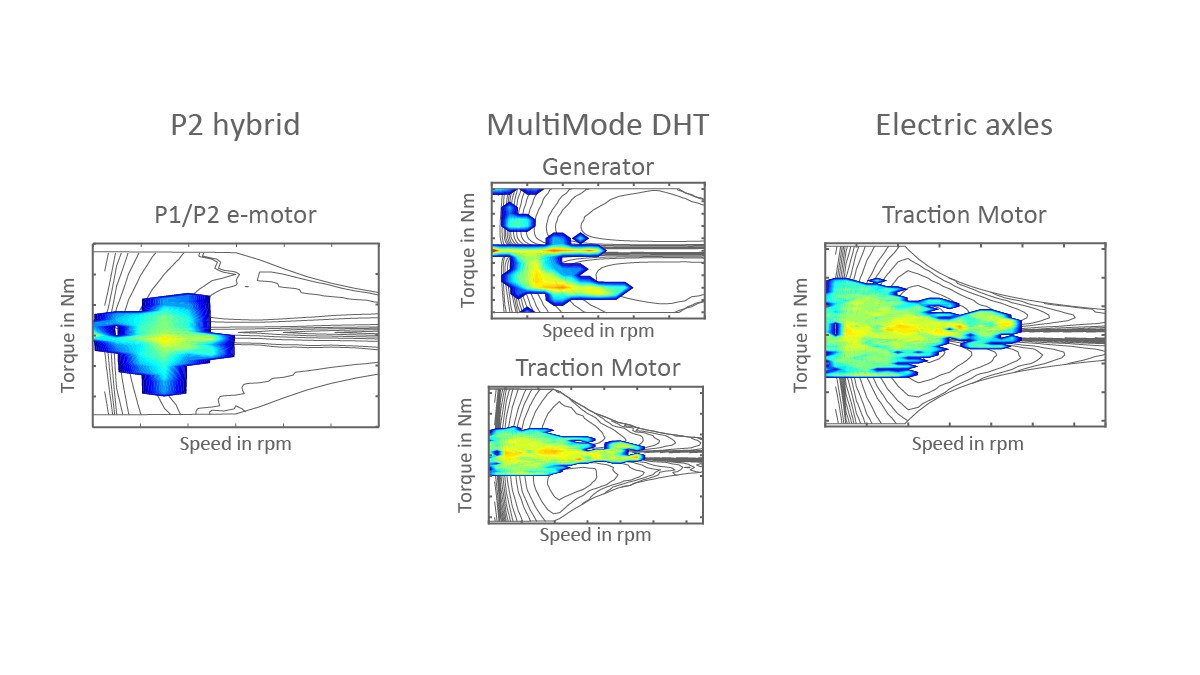
特定用途に最適なモータサイズの選定には、多くの基準を検討する必要がある。性能、NVH、使用運転領域での効率、搭載スペース、重量、コストなどである。各基準の目的は異なり、製品レベルでの標準化ソリューションでは解決できず、生産レベルでの標準化によってのみ解決できる。製品レベルでは、調整可能因子は多く、それらの調整によって積厚、エアギャップ、磁石配置などが最適化されるが、一人の設計エンジニアが、短時間で最適条件を発見することは困難である。シェフラーが開発した自動最適化プロセスを使えば、限られた開発期間内にほぼ無限の組み合わせから少数の有望な組み合わせを発見できる。
多次元的プロセスの使用に際して重要なことは、パラメータの変動可能限界をあらかじめ明確にしておくことである。これら限界のほか、使用可能搭載スペースは、主として生産プラットフォームにより規定される。プロセスで生ずる形状・配置の変化を示す簡単な例を図5に示す。制約条件があるため、得られた関数は標準的なパレートフロントには対応していない。
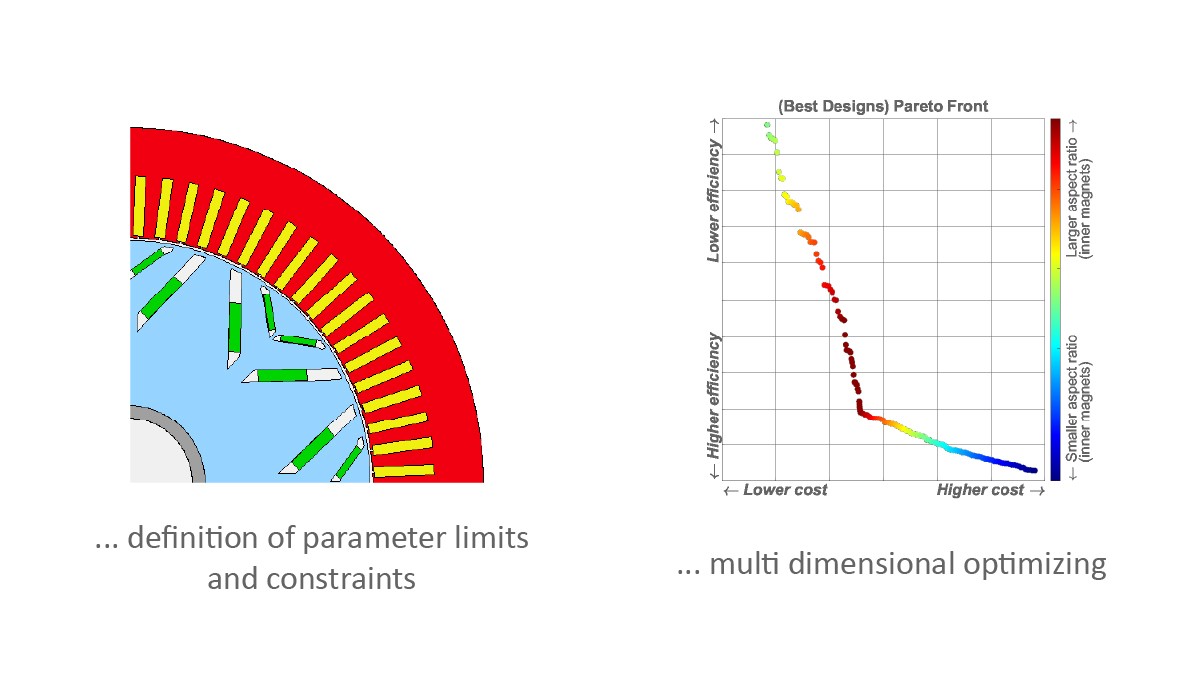
アジャイル量産システム
本稿で述べる最適化プロセスとは、開発プロセス終了時点で、確実にモータ設計を達成するものである。製品側からみれば最善ソリューションであり、シェフラーの技術プラットフォーム範囲内で製造可能なモータ設計である。ここで、量産に向けた生産規模拡大に関して問題が生ずる。顧客が望むトルク、効率、NVHなどの特性を決定するのは、製造パラメータだということである。製造パラメータは、供給材料やプロセスステップのばらつきによってわずかに変動するが(図6)、目標と実際の偏差はモータ特性にとってプラスにも、マイナスにも作用する。ばらつきが相殺し合い、組立後の製品が正確に所定の特性をもつこともあり得る。
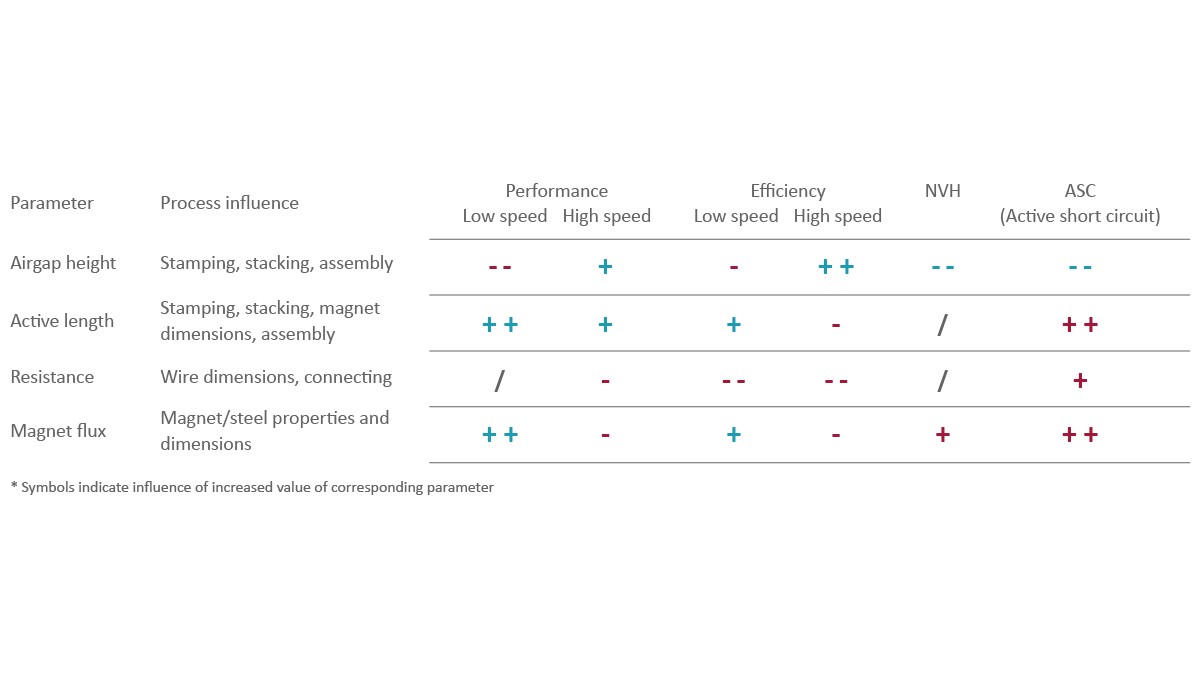
インダストリー4.0の中核をなす継続的プロセスモニタリングによって、製造中の各部品のばらつきを検知することができる。その結果、製造中の各ワーク(工作物)に合わせてツール設定の精密調整が可能である。組立時に相殺するばらつきを持つ部品同士をペアにすることもできる。シェフラーの生産モジュール化は、こうした目的の実現を目指すものである。
“オンライン”上での製造モジュールは、新規アジャイル生産コンセプトの基礎となっている。最短サイクルタイムと高スループットを実現するための統合化製造モジュールが、相殺可能なばらつきの管理・調整に必要な条件を提供する。
少・中量でのモータ複合生産には、図7に示す無人搬送車(AGV)を使って各プロセスモジュールをリンクすることが可能である。プロセスシーケンスと段取り作業は、AIベースのプロセス制御技術「オンデマンド」で制御する。「アジャイル生産」においては、いくつかのプロセスステップに代替技術(異なる巻線仕様など)を導入しつつ、他ステップ(ワニス含浸など)には同様の技術を維持することができる。ネックとなるリソースにモジュールを追加することで、生産能力の増強を図ることが可能である。
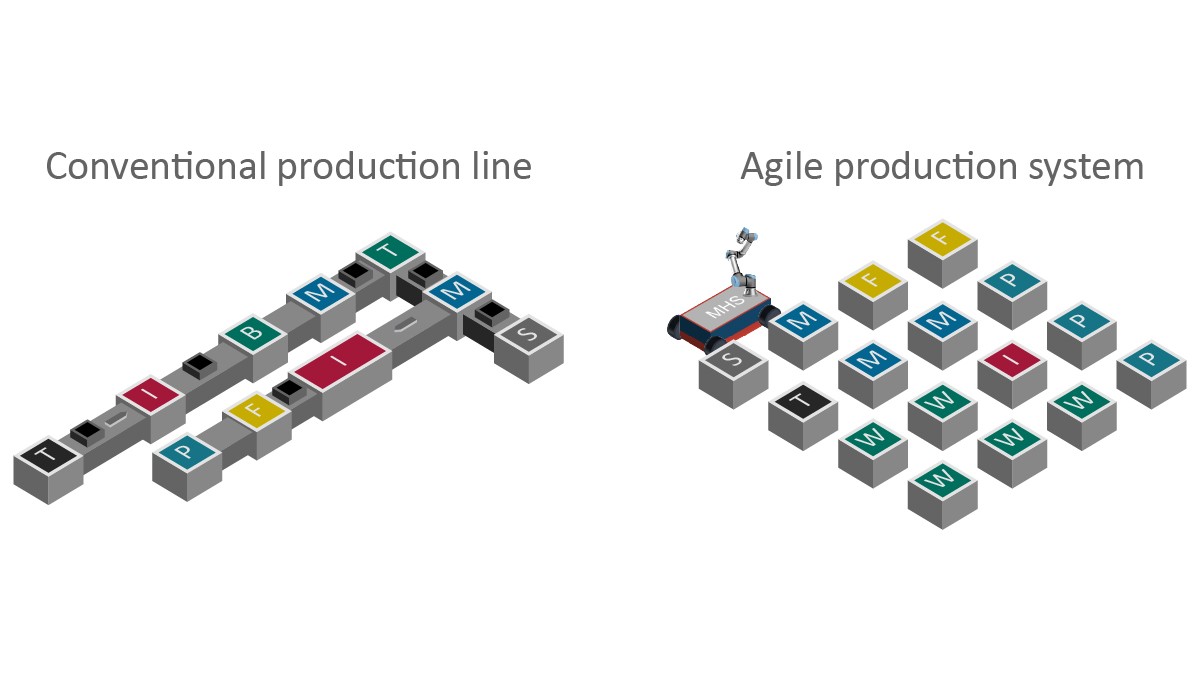
- オフライン:製品開発時点で、特定の設計が既存モジュールや計画されたモジュールで製造可能かどうかチェックできる。ツール/ワーク(工作物)レベルで比較し、重点を絞った迅速な開発プロセスが可能となる。
- オンライン:製品のデジタルツインは、製造工程を通過する製品自体の製造関連データを保存する。データは、次製造工程でプロセスモジュールのデジタルツインにより呼び出すことができ、個々のプロセスパラメータの変更、組立時の機能指向プロセス制御の実行ができる。
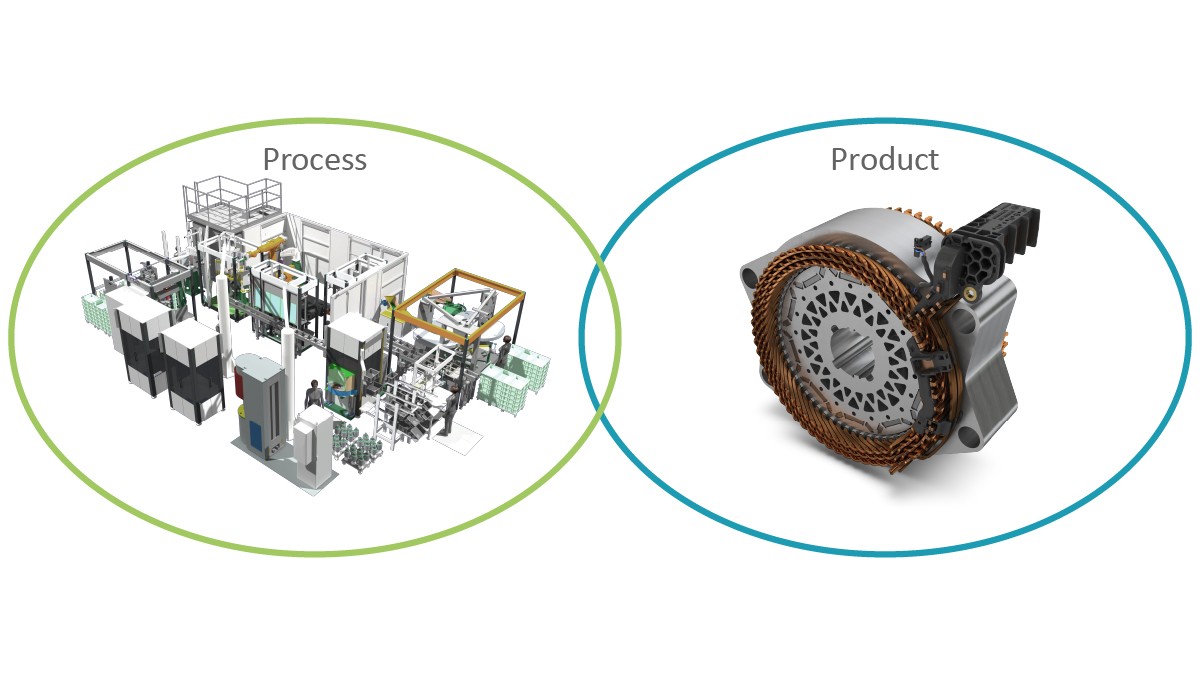
プロセスと製品のイノベーション
革新的技術の導入は、プロセスと製品の緊密な連携による強力な相互作用をもたらす。いくつかの新規開発を例にとって説明しよう。プロセスイノベーションは、主として製品設計の限界を拡げる。一方、製品イノベーションは、主として拡張された限界内で顧客向けモータ特性をさらに向上させる。
プロセスイノベーションの例
連続波巻にはいくつかのメリットがあり、すでにいくつかの報告がある[1]。注目すべき点は、コイルエンドの溶接をなくしたことでセグメント方式に比較して軸方向の搭載スペースが小さくなる。さらに、連続波巻は比較的細い平角線を容易に処理できるので周波数損失が改善する。
シェフラーは、ステータヨークとスロット部を別々の部品として設計する第2世代の連続波巻技術を開発中である(図9)。この設計では、ヨークを端部に取り付けるだけなので、外径側から巻線が可能となり、ステータ径に関する制約がなくなる。接合時のばらつきが小さいことと巻線を前圧縮することで、占積率が高まる。クローズドスロットによって高調波による励振が減少し、トルクリップルを防止できる。また、スクラップを減らすことができる。最後に、クローズドスロットはスロット冷却にも利用できる。スロット内を冷却することで非常に効果的な熱放散が可能となり、高い連続出力をもつモータを実現できる[2]。
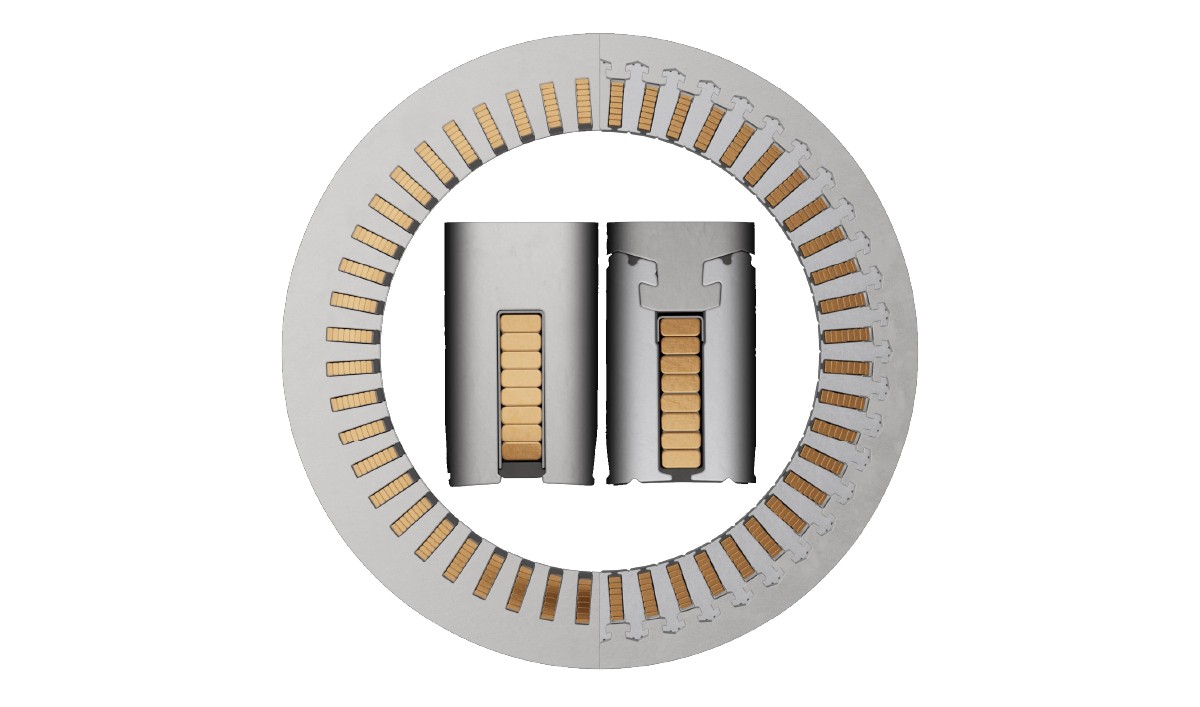
ステータコアの焼鈍もプロセスイノベーションのひとつである。焼鈍により、加工中に生じたミクロ組織の欠陥を修復することができる。材料の均質性が向上し、励磁における出力損失が低減する。焼鈍の効果は、電磁鋼板の薄型化よりも効果が大きい。測定結果を図10 に示す。
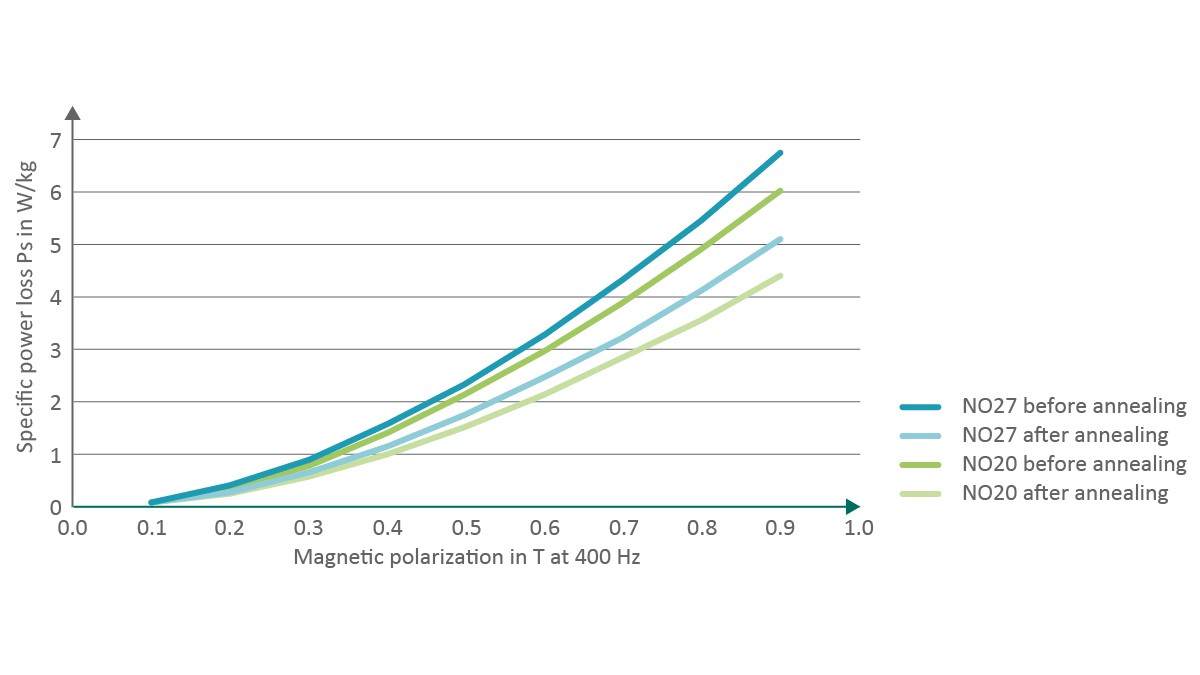
つぎに、ステータコアの固定がある。量産時の一般的製造プロセスは機械的接合であるカシメである。単層コーティングの電磁鋼板を使用でき、プレスダイ中で積層し、その後に溶接を行うので低コストではあるが、固定部材による積層板間の導電接続が渦電流損失につながる。積層は接着コアを用いることことも可能である(全面ボンディング)。きわめて正確な積層板の配置が可能となる。ただし、このプロセスでは2層コーティングのシートを使用し、エナメル焼き付けの硬化プロセスも必要となるので製造コストが上昇する。
この問題を解決するために、シェフラーはトランスファーモールディングプロセスを開発した。このプロセスでは、ステータコアは速硬性ポリマー注入によって機械的に結合される。両プロセスの利点を生かし、単層絶縁コーティングの電磁鋼板により、精密位置合わせをしたステータとロータの積層を実現できる。積層板間に導電接続はなく、出力損失への悪影響もない(図11)。
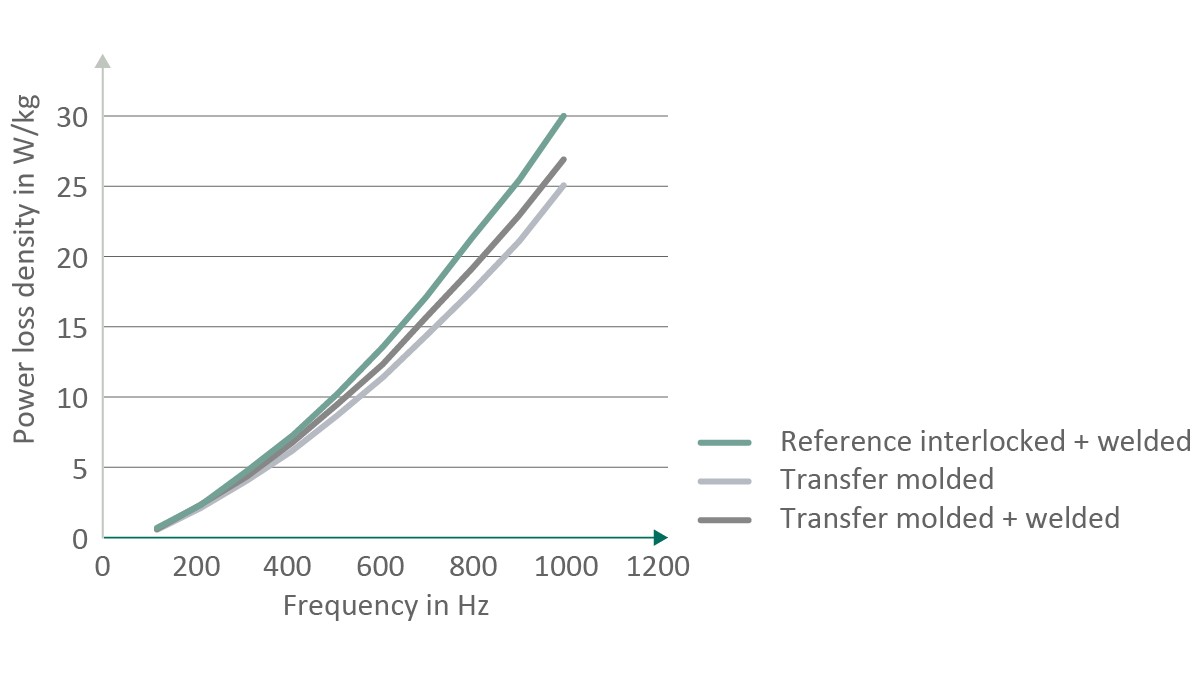
製品イノベーションの例
現在のラジアル型モータの効率は、すでに非常に高い。図12 に、アクスル用の最先端のモータについて、実運転条件に関連する運転ポイントでの効率を示す。発生出力損失には、運転ポイントごとに原因がある。簡単にいうと次のようになる。市街地走行など低出力時ではステータの鉄損が大部分を占める。損失割合は、負荷が増すにつれて減少する。一方、出力が増すと銅損の割合が増大する。高負荷時は、この損失が総出力損失の4分の3を占めることもある。
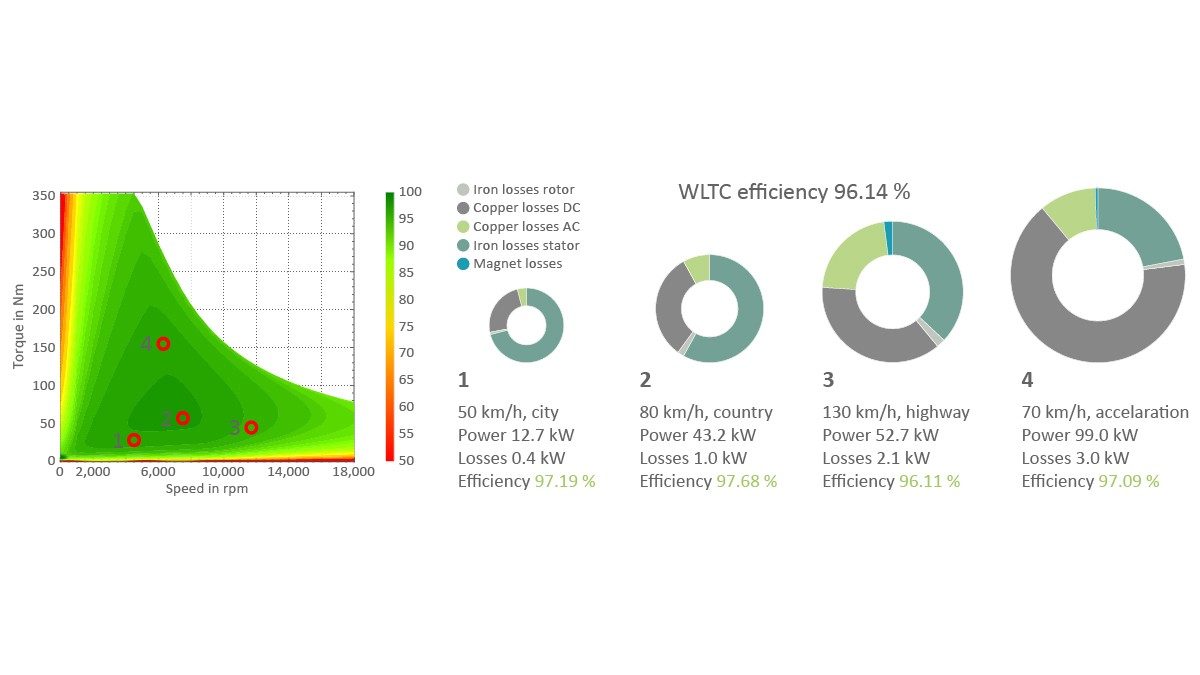
上記技術をWLTC平均効率96.05%のモータに適用すれば、各運転ポイントでの出力損失を顕著に改善できる。図13 は、一般的な周辺道路運転時の運転ポイント2での効率を示している。連続波巻とステータコアの焼鈍が最大の効果を発揮している。結果として、WLTC効率が1パーセント以上改善した。この例から、シェフラーの探求する製品開発とプロセス開発の緊密な連携が、最終顧客の電動パワートレイン特性の向上につながっていることが理解できる。
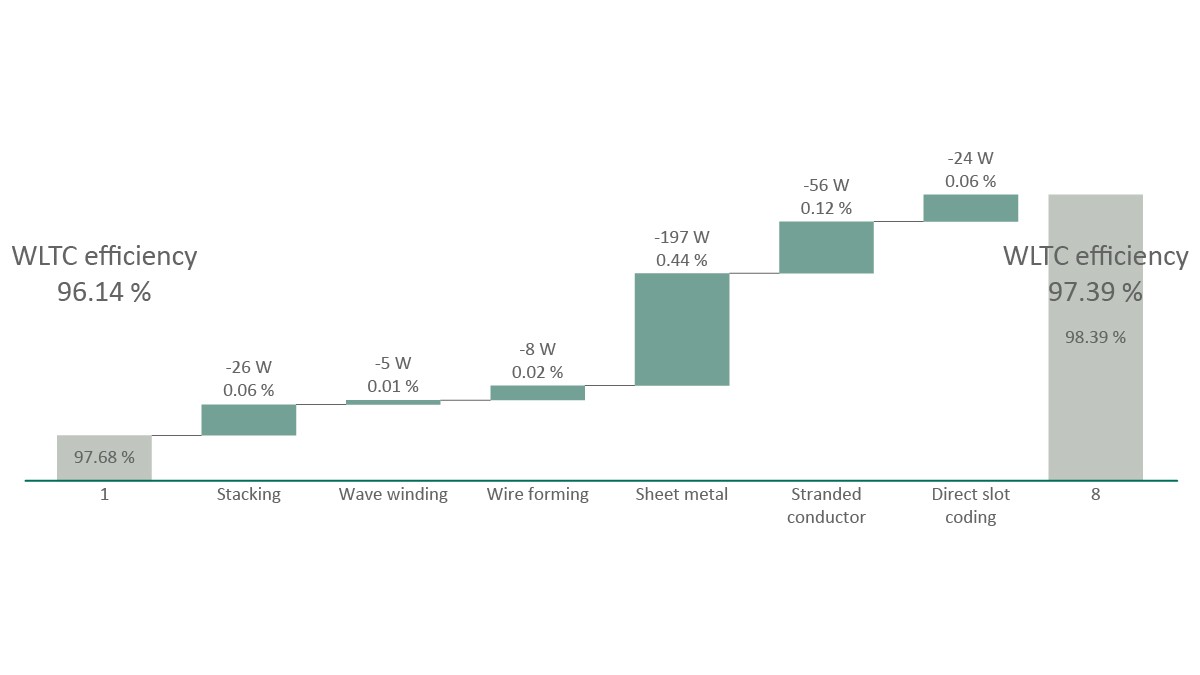
- ドライブシャフト上のロータのI型構造。ロータは、ステータ上の2枚のディスクに挟まれて回転する。
- ヨークのないロータ設計。軽量化ロータ構造によって、トランスミッションインプット側の慣性モーメントが最小限となる。
- スロット内を冷却。
シェフラーの開発・試験したアキシャル型モータの試作品(図14)は、わずか85 mmの軸方向長さと308 mmの外径でありながら、250 kWのピーク出力をもつ。連続出力は190 kW以上で、ピーク出力に比較的近い。最大トルクは480 Nm。質量は33 kgで、13.5 kW/kgという非常に高い出力密度を実現している。シェフラーがこの数値を達成できたのは、2017年にシェフラーの完全子会社となったCompact Dynamics社のレース参戦経験によるところが大きい。
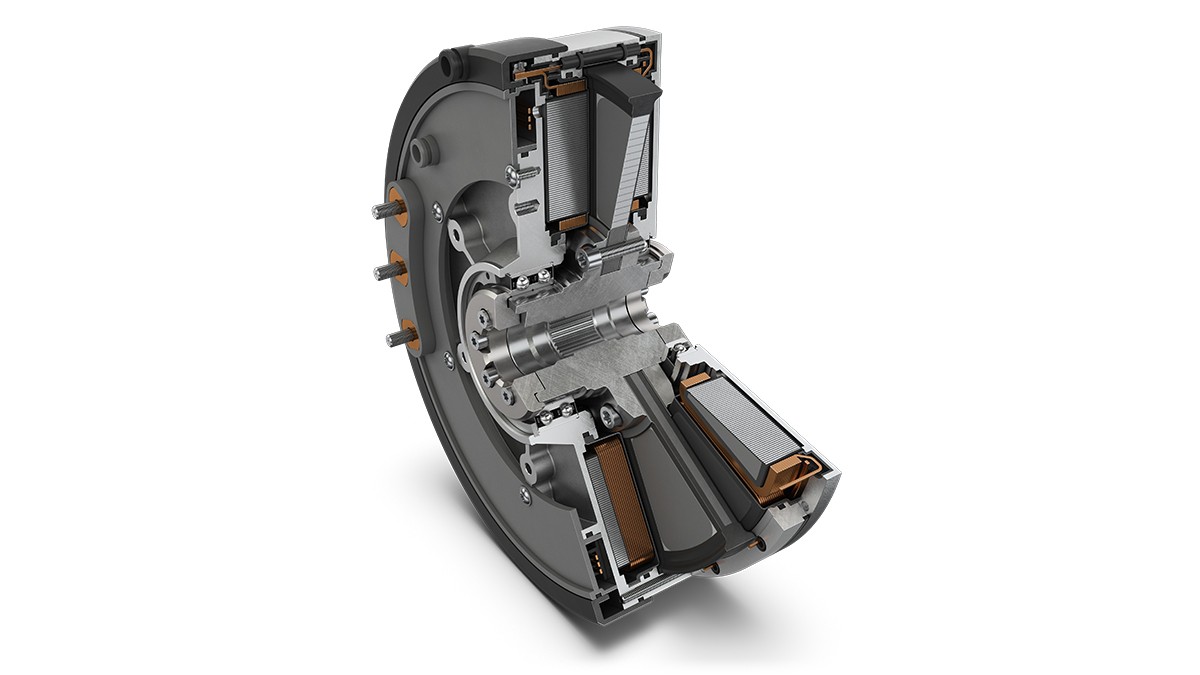
アキシャル型モータは、乗用車用パワートレインには使用されてこなかったが、それには理由がある。量産コンセプトが開発されておらず、NVHの技術的課題が解決できなかったからだ。運転条件と製造のばらつきに対して、軸方向エアギャップの確保も課題だった。さらに重要な理由としては、トランスミッションインプットシャフトの軸方向動作が不要な励磁を引き起こすという問題があった。
シェフラーは、上記デメリットを解消するモータ構造を採用した。図15 に示すI型構造では、ロータを2つのステータ内面に挟んで支持する。。エアギャップは固定可能である。ステータ/ロータユニットは、電動アクスルなどのハウジング内に小径ねじで固定することで、外径とドライブトレイン間に導電路が発生しないようにできる。採用した設計では、トランスミッションインプットシャフトが軸方向に自由移動し、静的公差と動的公差が最適状態で均衡する。
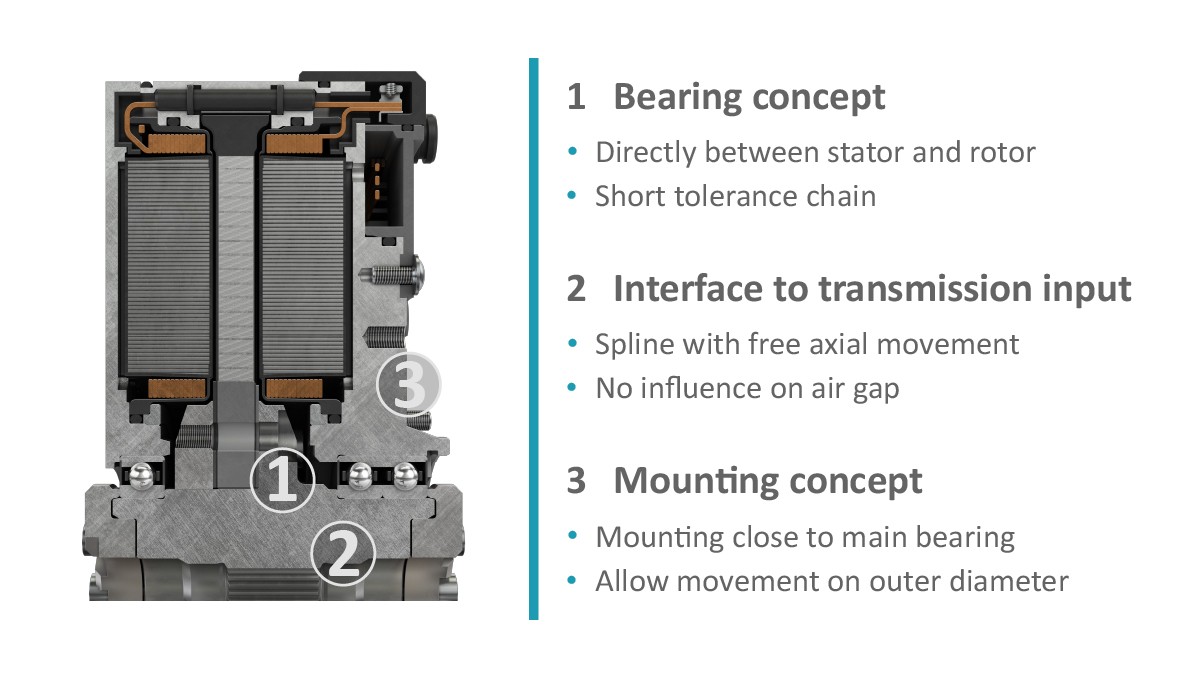
磁束が軸方向であれ半径方向であれ、永久磁石同期モータ(ESM)にとって課題となるのはロータの磁石の安定調達であり、唯一のソリューションは、巻線界磁形モータである。ESMのデメリットは、ロータに電流が連続的に流れ、特に低速レンジでは、比較的高い銅損が生じることである。シェフラーは、この問題を回避できるモータを開発中である。ロータにはスロット内冷却が採用された(図16)。巻線付近をオイル冷却することで、温度上昇が大幅に抑制される。
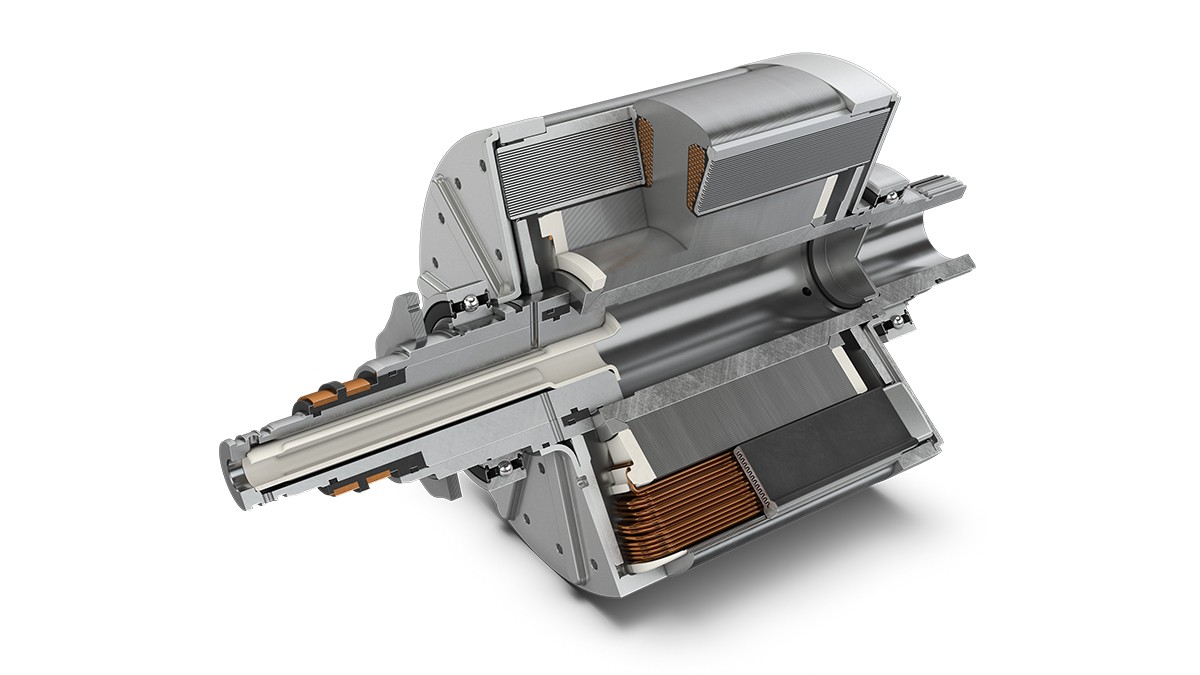
パワーエレクトロニクス
モータの効率だけを向上させても、モータ動作品質と効率向上が伴わなければ意味がない。シェフラーは、外部パートナー企業からパワーエレクトロニクス統合ノウハウを獲得し、400Vで動作するパワートレインを実現した。これは、ハードウェア(Homm等[2]が記述する最大4in1対応の電動アクスル)とパワートレイン制御用ソフトウェアの融合から生まれたものである。800Vアーキテクチャについては、シェフラーは乗用車と商用車に使用できる独自SiC(炭化ケイ素)半導体ベースのパワーエレクトロニクス技術を開発した(図17)。ソフトウェアとハードウェアの統合化知識はサーマルマネージメントを含むパワートレイン全体に及ぶ。ソフトウェア統合の基礎は、パワーエレクトロニクスの副次機能をカバーするシェフラー独自のプラットフォームである。モデルベース設計により、顧客など外部パートナー企業からのソフトウェア機能を統合できる。

シェフラーは、パワーエレクトロニクス戦略として、共同設計アプローチを採用したプロセスイノベーションと製品イノベーションを推進し、最高の電動特性の達成を目指している。インダクタンスについては、サプライヤーやパートナー企業との緊密な協力の下に、ハーフブリッジモジュールでは7%、コンデンサでは15%、リードフレームでは20%の低下を実現した。この結果、高スイッチング周波数では電圧変動低減を大幅に低減できた(図18)。振幅低下、スイッチング周波数上昇、電子部品負荷の大幅な低減などにより寿命の長期化が期待できる。
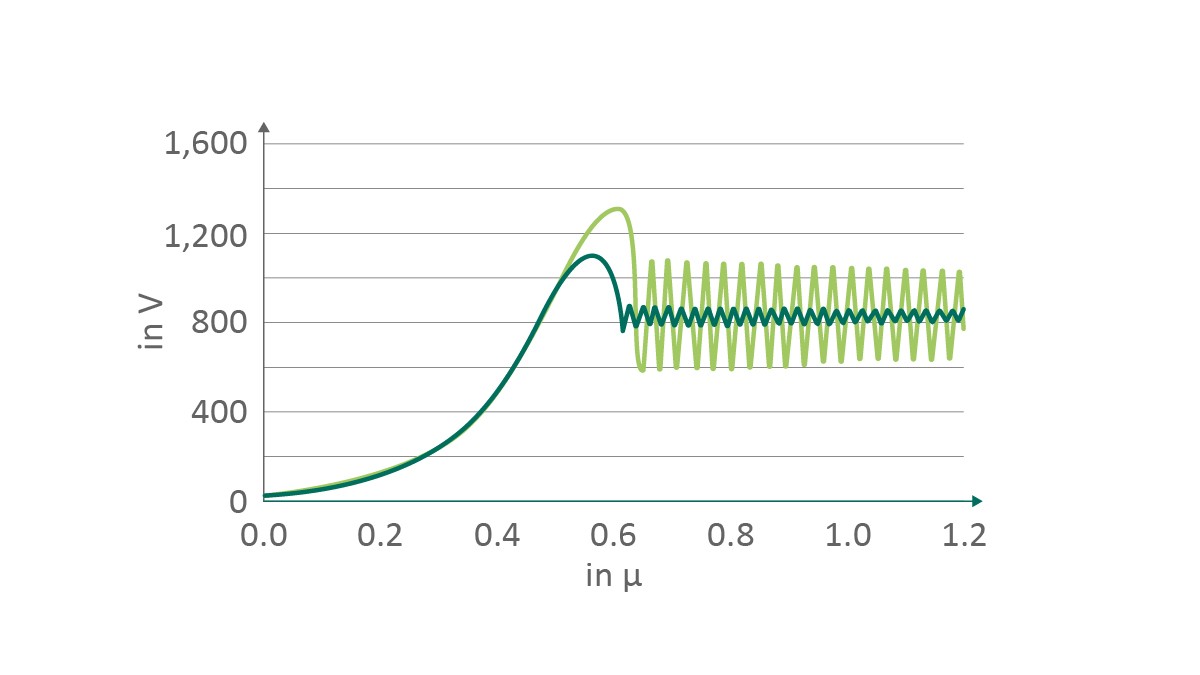
冷却は、パワーエレクトロニクスによって切り替えられる連続出力や電子部品の使用寿命にとって非常に重要である。シェフラーでは、ハウジング一体型の水冷方式を採用している。通電部品(電源スイッチ、リードフレーム、コンデンサ)をヒートシンクに接続し、連続高負荷時の均一な温度分布を得ている(図19)。
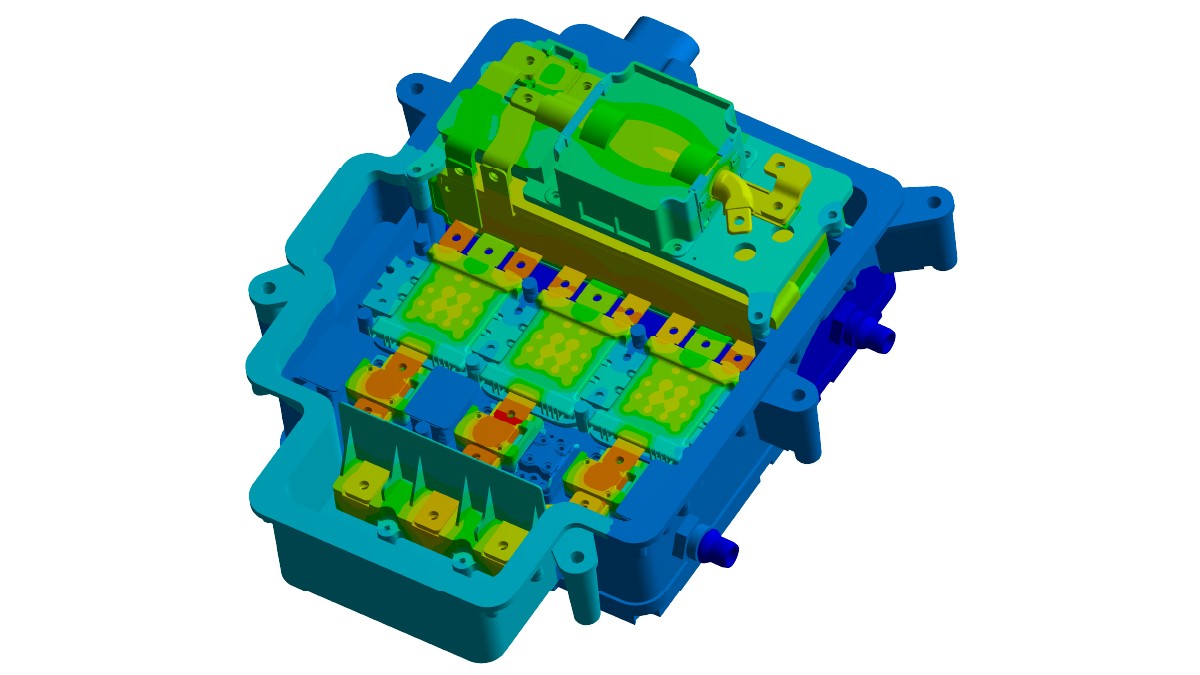
シェフラーのパワーエレクトロニクスは、最大効率が99%を上回る優れた技術である。最適化ハードウェアと各運転領域のフレキシブルで正確な起動プロセスとを組み合わせることによってはじめて実現する(図20)。低速・低負荷時は、スイッチング損失が大部分を占め、NVHに問題がなければスイッチング周波数を下げることで損失を低減できる。追い越し運転時など高トルクが要求される場合は、電流増大で伝導損失が増加する。この領域のスイッチング周波数は劇的に上昇し、電圧リップルの振幅を制限する。停止状態からのフル加速は、全損失の70%を占めるほどに伝導損失を増大させることがある。NVHを考慮した上で、スイッチング周波数をさらに低下させて熱負荷を低減することができる。高速運転の場合(モータが効率マップの弱電流領域で動作時)、電圧を選択的に過変調してモータトルクをできるだけ高く維持する。スイッチング損失と伝導損失は均衡する。
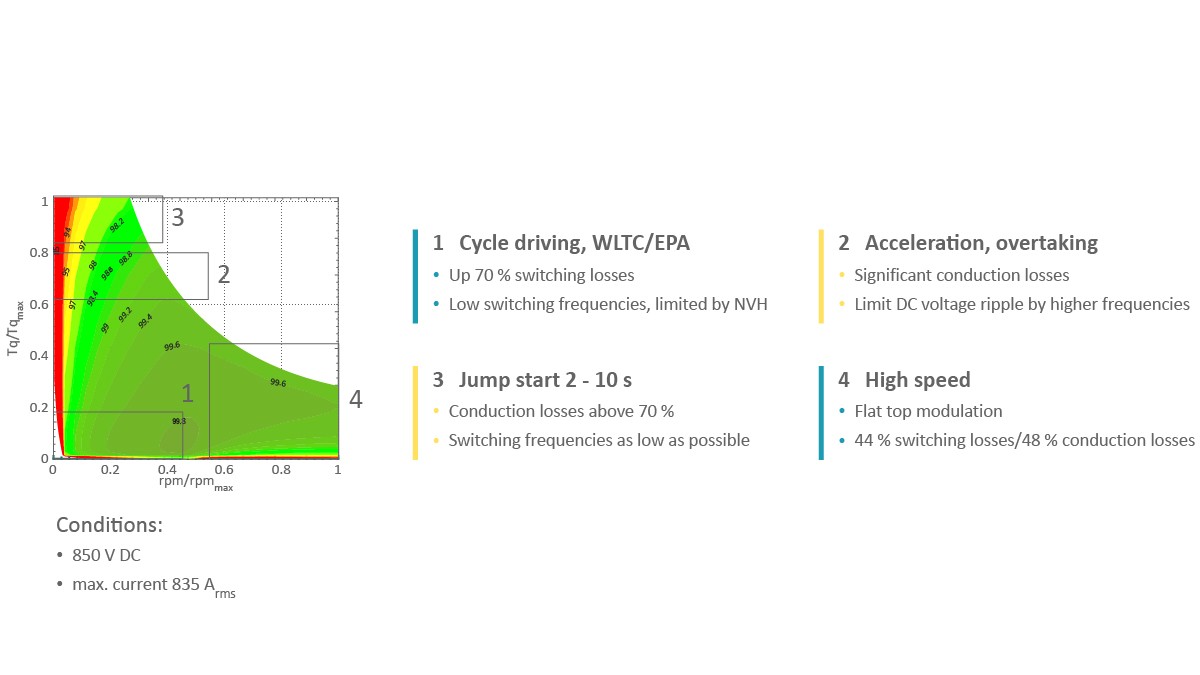
追加コンポーネント制御も統合できることがシェフラーのパワーエレクトロニクスの特長である。追加コンポーネントとしては、冷却用または潤滑用ポンプ、パーキングブレーキ、デカップリングユニット、エアコン・コンプレッサなどがある。自動車メーカーには追加制御装置のインテグレーションに費用負担は生じない。
70 kW/Lという高体積出力密度であり、パワーエレクトロニクスの搭載スペースはほとんど必要ない。実現したいシステムレベルで、きわめてコンパクトなパワートレインの構築が可能である。
次世代型の800Vパワーエレクトロニクスは、顧客関連機能すべてのさらなる向上を特長とする。基本的に3つのイノベーション領域がある。第一に、現在はまだリードフレームを介して個別に電気接続されている電流センサ、コンデンサ、EMIフィルタなどのコンポーネントをハウジング内に収納できる(図21)。搭載スペースの削減だけでなく、銅の使用量も削減できる。これは伝導損失の13%の低下につながる。第二に、一部のハウジングを樹脂製として重量とコストの低減を図っている。コンポーネントは非導電性樹脂製クーラに直接配置することが可能である。必要な電磁シールドは、ハウジングに塗装を施すことで達成できる。第三に、電力段スイッチ用の電力半導体をSiC(炭化ケイ素)からGaN(窒化ガリウム)に変更可能なことだ。GaN材料のメリットは超高速スイッチングにあり、モータの円滑制御、20%程度の出力損失低減につながる。シリコン基板GaN半導体の市場成長は、コスト面でもSiCにまさる優位性をもたらす。
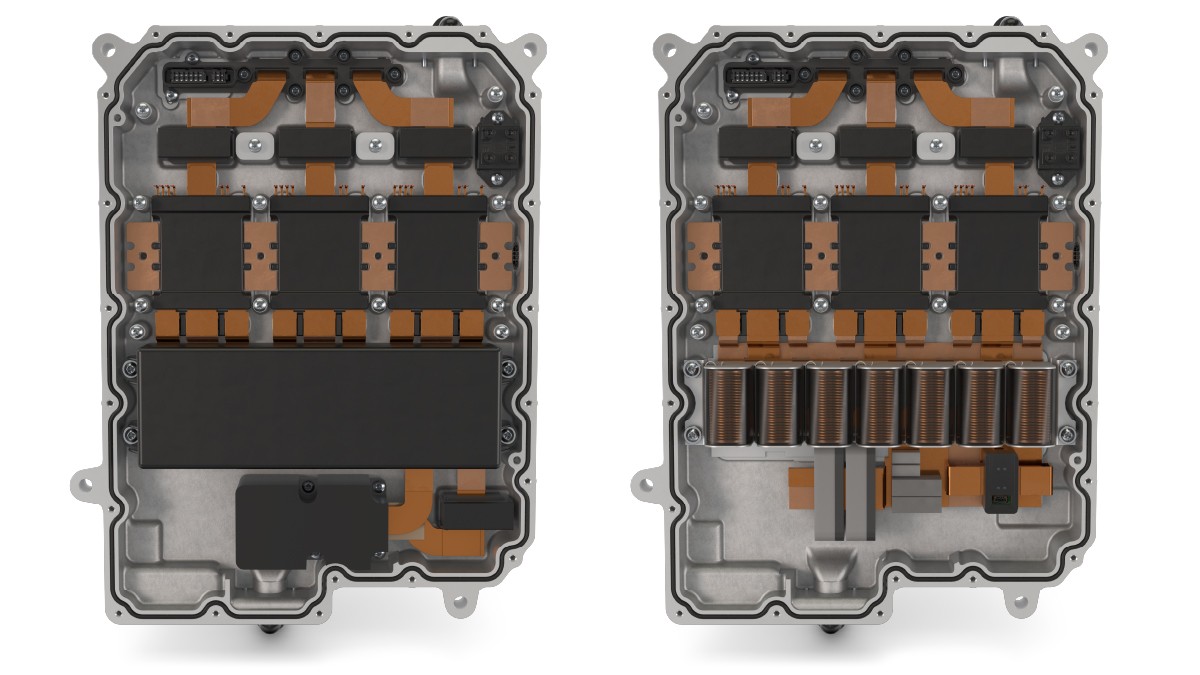
まとめ
電気自動車の登録台数が急増している。したがって、モータとパワーエレクトロニクスを迅速かつ低コストで量産化することが急務である。各種パワートレインに対応する柔軟性をもつ広範な製品ラインナップをカバーする必要がある。シェフラーは、あらゆる種類、サイズ、性能のモータについて、生産ステップを明確化し、グローバルに標準化する生産技術プラットフォームを通じて、時代が要求するモータの生産基盤を提供している。総額5億ユーロ超の資金を投じて、2029年には年間400万台の電動モータ生産能力を達成する見通しである。
自動最適化プロセスにより、技術プラットフォームの枠内でアプリケーションごとのソリューションを発見し、生産することも可能となる。製品と生産モジュールのデジタルツインに基づくリアルタイム生産管理により、材料と製造のばらつき補正やアジャイル生産プロセスを用いた少量製品の低コスト生産が可能となる。
ステータコアの焼鈍、高度な連続波巻などのプロセスイノベーションにより、現在のラジアル型モータの効率をさらに向上させることができる。新型アキシャル型モータを開発したシェフラーは、きわめて高い体積出力密度の電動パワートレインの実現を可能にした。これと並行して、巻線界磁形モータのコンセプトも出現している。これは、ロータのスロット冷却によって低速レンジでの銅損を低減するモータである。
800Vアーキテクチャについては、シェフラーは自社でSiC半導体ベースのパワーエレクトロニクスを開発済みである。このパワーエレクトロニクスは、乗用車にも商用車にも使用でき、高効率と高体積出力密度の両方を実現する。将来的には、GaN電力半導体の採用によって、さらなる改良を加える予定である。
[1] Pfund, T.: The Schaeffler E-Drive Platform: Modular and Flexible. Baden-Baden: Schaeffler Kolloquium, 2018
[2] Homm, M.: Fascination Electric Powertrain. Bühl: Schaeffler Kolloquium, 2022
[3] Eireiner, D.; Völkel, F.; von Petery, G.: Bearings Reinvented – Contribution of Rolling Bearings to Improving Ranges and Charging Times of Electric Vehicles. Bühl: Schaeffler Kolloquium, 2022