未来のパワートレイン、モビリティを見据えたベアリング技術 転がり軸受が実現する電気自動車の航続距離延長
Dr. Dieter Eireiner | Georg von Petery | Dr. Franz Völkel
電気自動車(BEV)向けパワートレインの分野では、航続距離の延長と充電時間の短縮が開発の焦点となっている。そのパワートレインには、軽量化や動力損失の低減、電動モータの最高回転速度の増加、システム電圧の800Vへの引き上げなど、さまざまな性能が求められている。ここでも、転がり軸受はパワートレインの機能を向上し、新しい技術ソリューションを実現するために重要な役割を果たす。シェフラーは、軸受をシステム全体の中の一つの要素と捉え、複数のシミュレーションツールを使用することにより、さまざまな要求に対し最適なソリューションを提供している。例えば、軸受内に流入するオイル量を制限する遠心ディスクを備えて攪拌損失を低減する高速モータ用玉軸受や、高い耐荷重性を備えた高速モータ用円筒ころ軸受などがある。さらに、最大電圧が800Vの場合、つまりパワーエレクトロニクスにシリコンカーバイド(SiC)半導体を搭載している高電圧システムの 場合、放電電流によって軸受や電動パワートレインのギヤ部品が損傷しないように対策を講じた軸受などもある。
未来の転がり軸受に求められること
現在の自動車業界で注目されるのは、パワートレインの電動化の進展である。シェフラーは、電動アクスルやハイブリッドトランスミッションなどの開発を通じて、こうしたトレンドを促進している。システムと構成部品に関するシェフラーの広範なノウハウが、そのための基礎となる。このノウハウによって、個別部品を開発・調整してシステムの機能向上を図ったり、新たな技術ソリューションを実現したりすることができる。シェフラーでの電動システム部品開発において中核をなす要素は、転がり軸受である(図1)。転がり軸受を最適化するには、軸受技術と電動パワートレインシステムの両面から、システム全体を包括的に理解することが要求される。シェフラーは、いずれの分野でも長年にわたり成功をおさめており、豊富な専門知識を活用することができる。
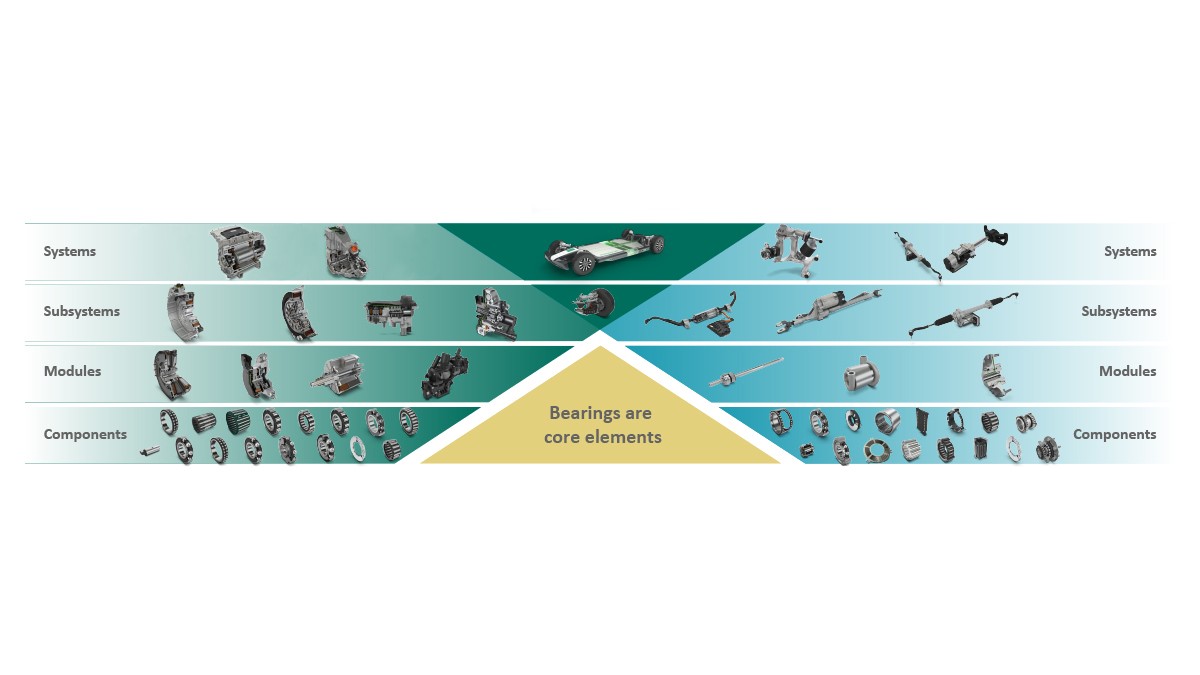
電気自動車(BEV)向けパワートレインの分野では、航続距離の延長と充電時間の短縮が開発の焦点となっている。これらの要件を電動パワートレインの開発という視点からみた場合、以下のようなさらなる具体的開発課題がみえてくる。
- 電動モータの軽量化を実現するモータ速度の高速化[1]
- 電動モータからホイールまでパワートレイン全体の効率最適化
- 部品の軽量化による質量低減
- 電力損失低減、充電速度向上、充電ケーブル径縮小のための高電圧化(~800V)
- ホイール軸受の摩擦低減による航続距離の延長
上記のすべてを実現するうえで、軸受開発は重要な意味を持つ。
高速モータ用軸受
電気自動車用の電動モータは、軽量化を求めて最大速度25,000 rpm、用途によってはそれ以上の速度に設計される場合が増えている。こうした高速電動モータは、図2(ギヤ図左上)のように高速モータ軸受(HSMB)で支持される。トランスミッション入力軸も高速モータ軸受で支持されるが、これは入力軸がロータ軸の回転と同じく高速で回転するためである(図2、ギヤ図の上段中央)
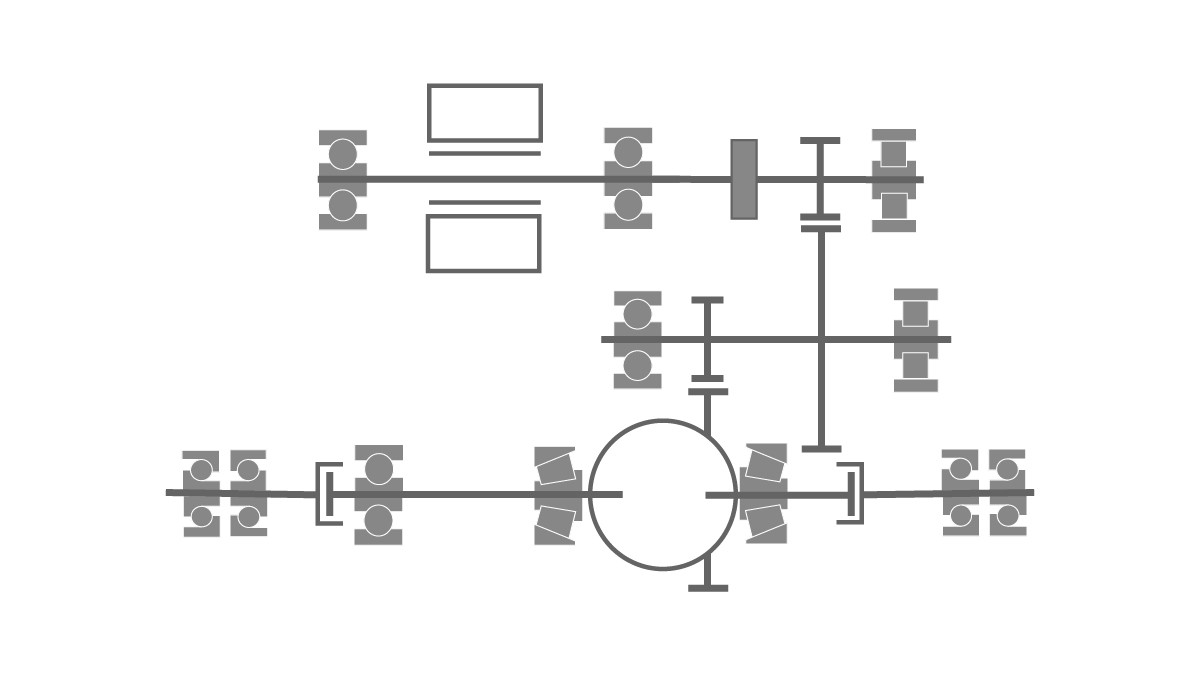
HSMBは、ほとんどの場合、発生負荷に対して十分な耐荷重性を有している。ただし、特に高トルクの場合や、トランスミッション入力軸にパーキングロックを使用する場合は、玉軸受の静荷重容量では不十分なこともあり得る。このような場合には、高速円筒ころ軸受を採用することで、搭載スペースの制約と耐荷重性の間で最適な妥協点が得られる(図3)。
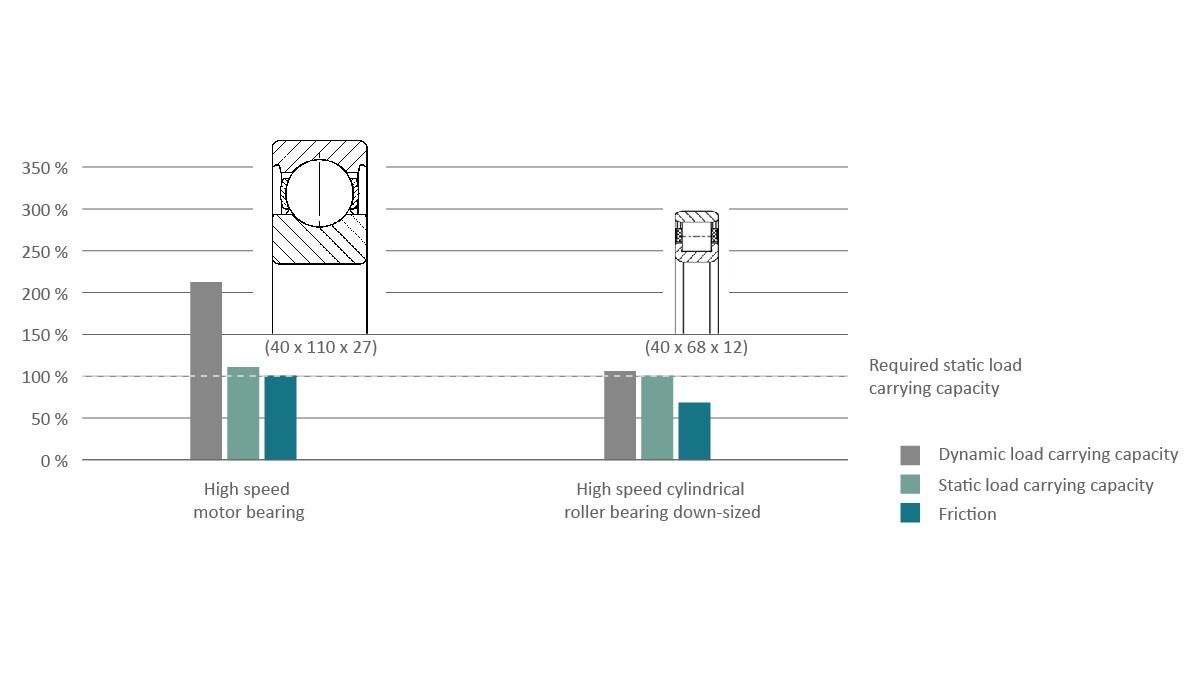
高速円筒ころ軸受は、従来の円筒ころ軸受とは異なり、内部形状、転動体数、寸法のほか、保持器の案内部や形状も最適化されている[2]。特殊なホーニング加工を施した転動体を使用することで、低騒音化を実現している。外輪にはつばがなく、内輪の両側につばを持つN形を採用することにより、軸受内の撹拌損失を最小限に抑え、HSMBと同等の速度パラメータを達成することも可能となる(図4)。
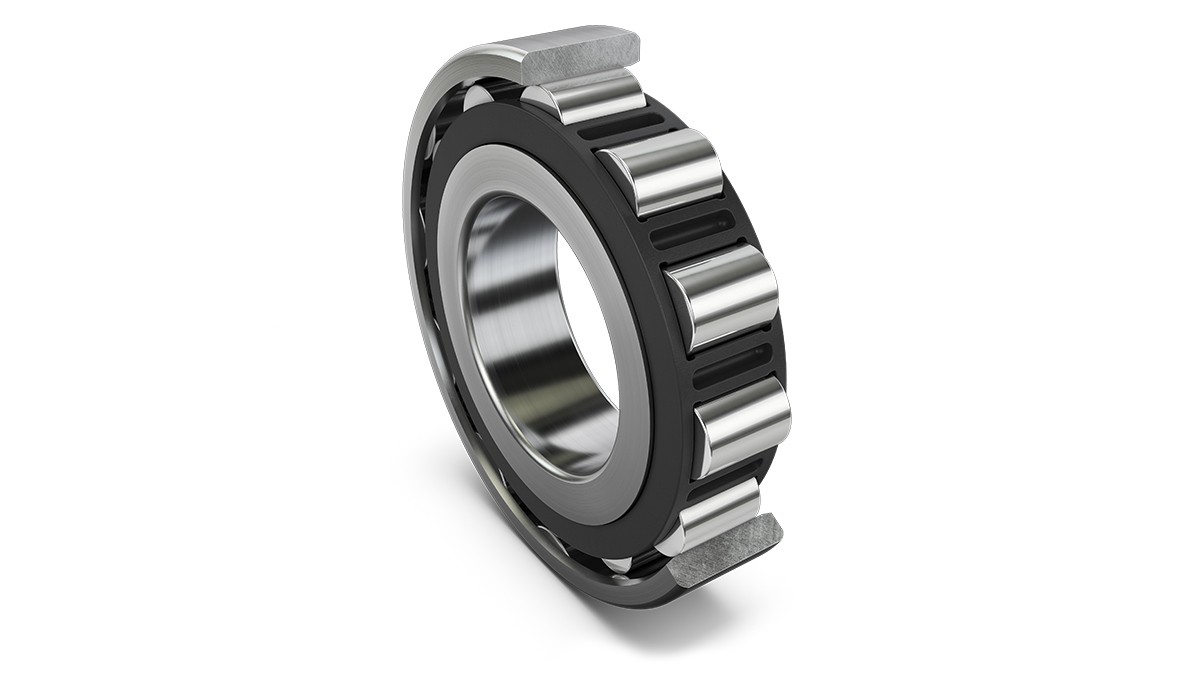
将来の電動パワートレイン開発に、新たな可能性が生まれている。例えば、電動アクスルのトランスミッション入力軸には、高速円筒ころ軸受の採用が進んでいる。図2の中間ギヤ軸(ギヤ図中段)では、玉軸受と組み合わせて固定側/自由側軸受として使用し、軸受の配列調整で起きる予圧による摩擦損失を回避することができる。ロータとトランスミッション入力軸が一体となっている場合、高速円筒ころ軸受の出現によって、今後は固定側/自由側軸受の構成で電動モータを支持することも考えられる。この場合は、現在のように3つあるいは4つの軸受を使用するのではなく、1つの玉軸受と1つの円筒ころ軸受のみの構成となる。
軸受製造技術の点でも、機械加工外輪を用いていた円筒ころ軸受が、外輪を鋼板からプレス加工するシェル形円筒ころ軸受へと技術シフトすることで、さらなるコストダウンの可能性が生まれる。シェフラーはこうした技術進歩に基づき、将来の高性能電動アクスル向けに、コスト面でも魅力的な軸受構成を提案することができる(図5)。
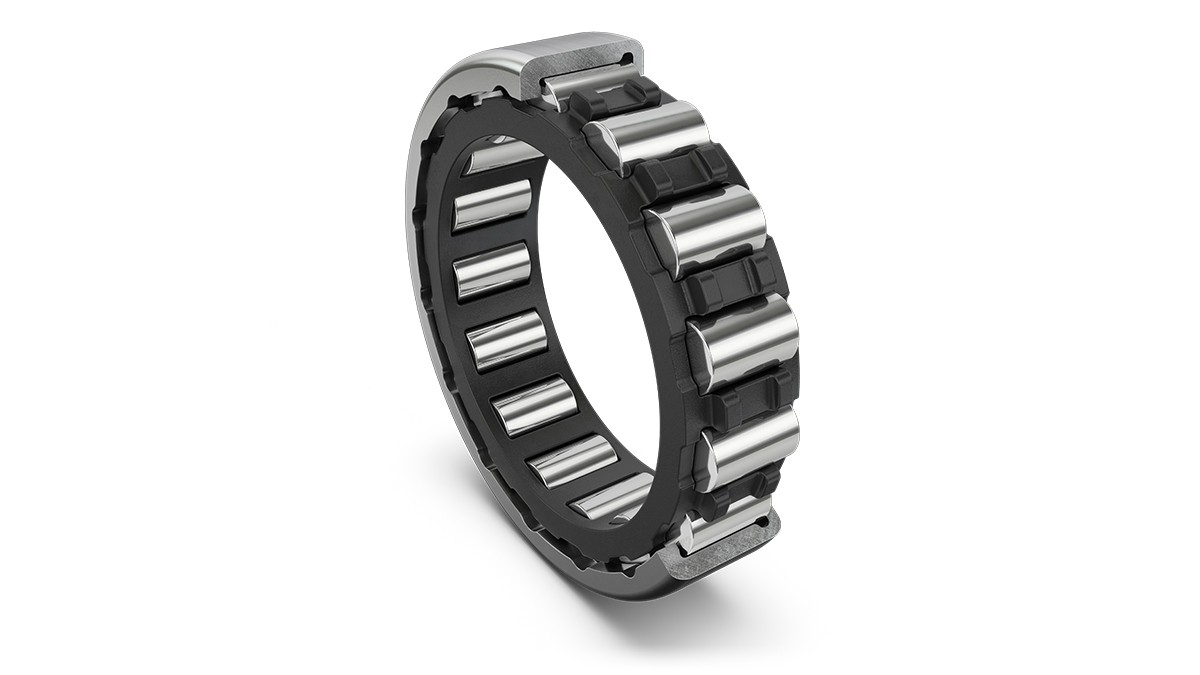
最適効率の軸受
シェフラーは、トランスミッション軸や中間軸用として、自社特許の遠心ディスクを一体化した高効率玉軸受を開発した。この技術は、開放形軸受と密閉形軸受の両方の利点を兼ね備えている。遠心ディスクは内輪とともに回転し、軸受内に流入するオイル量を制限して撹拌損失を低減する(図6)。
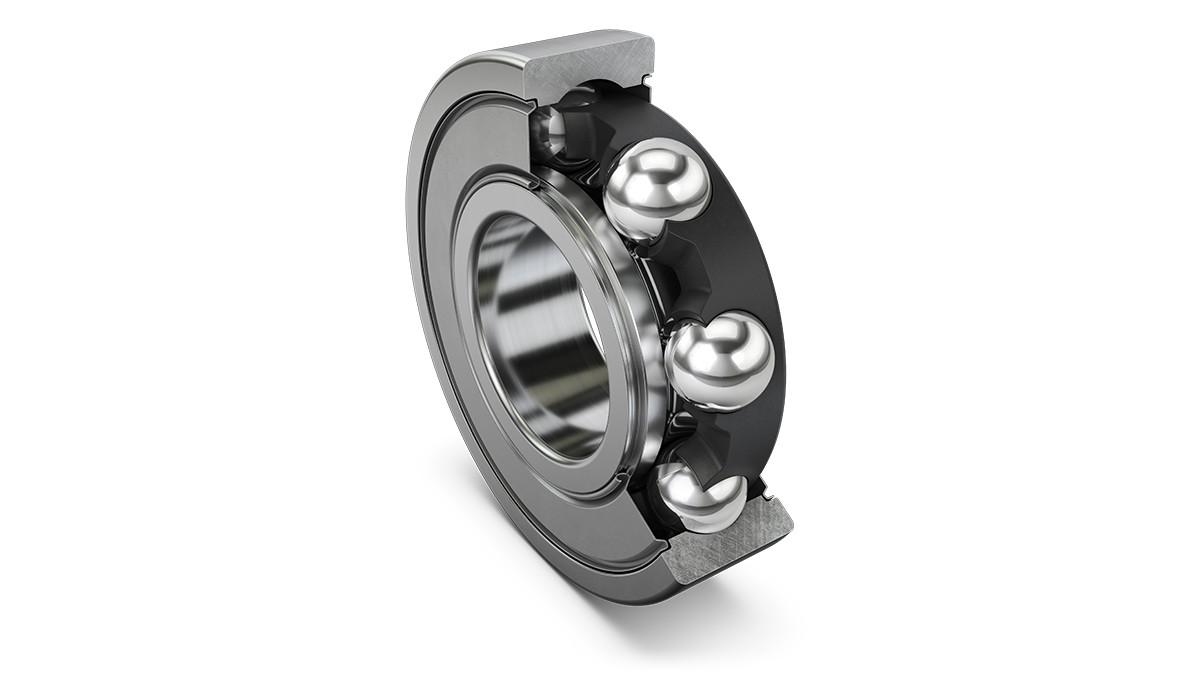
ディスクは、シール摩擦を生じることなく軸受内部への異物混入を効果的に防止する。遠心ディスクを搭載した玉軸受は、密閉形玉軸受と比べて最大70%、開放形玉軸受と比べても最大54%の摩擦低減を実現している(図7)。
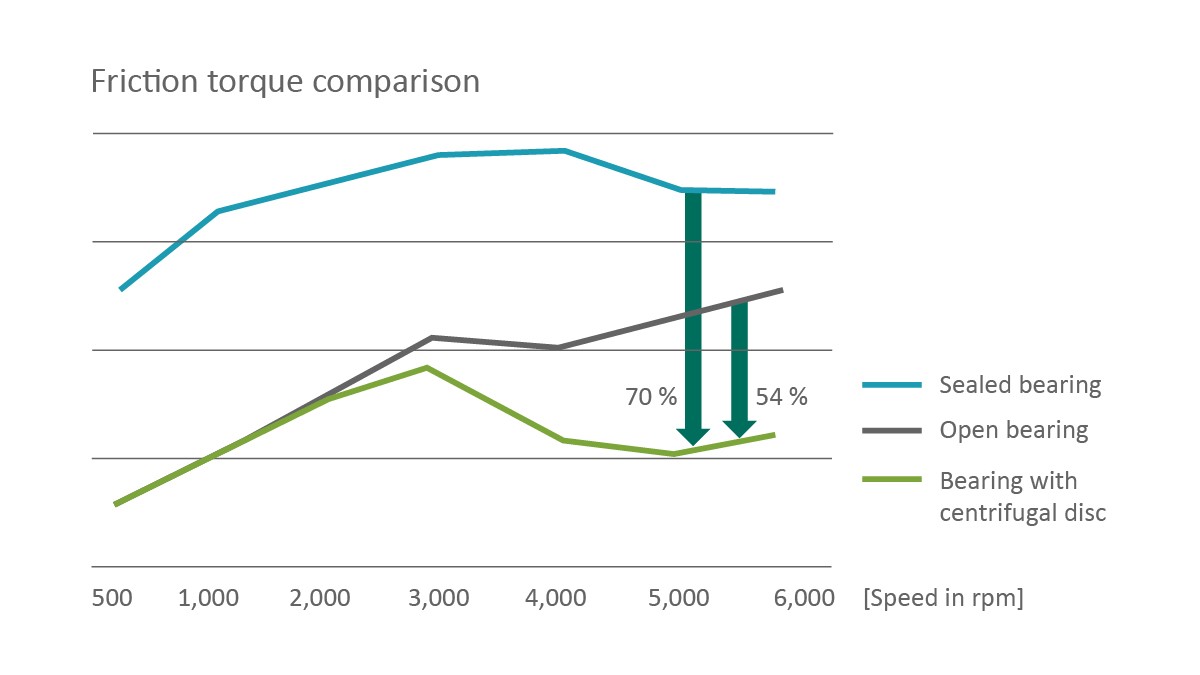
シェフラーの円すいころ軸受は、数十年にわたりトランスミッション出力軸やディファレンシャルに使用されている。円すいころ軸受は耐荷重性が高く、広い出力帯域に対応する。また作用点間距離が大きいため、高荷重を支持できる。円すいころ軸受を使用すれば、クリアランスフリーで高剛性のシャフトガイドシステムも実現可能である。シェフラーは、長年にわたる軸受設計と材料の継続的改善によって、円すいころ軸受の摩擦を一貫して低減させることに成功している(図8)。
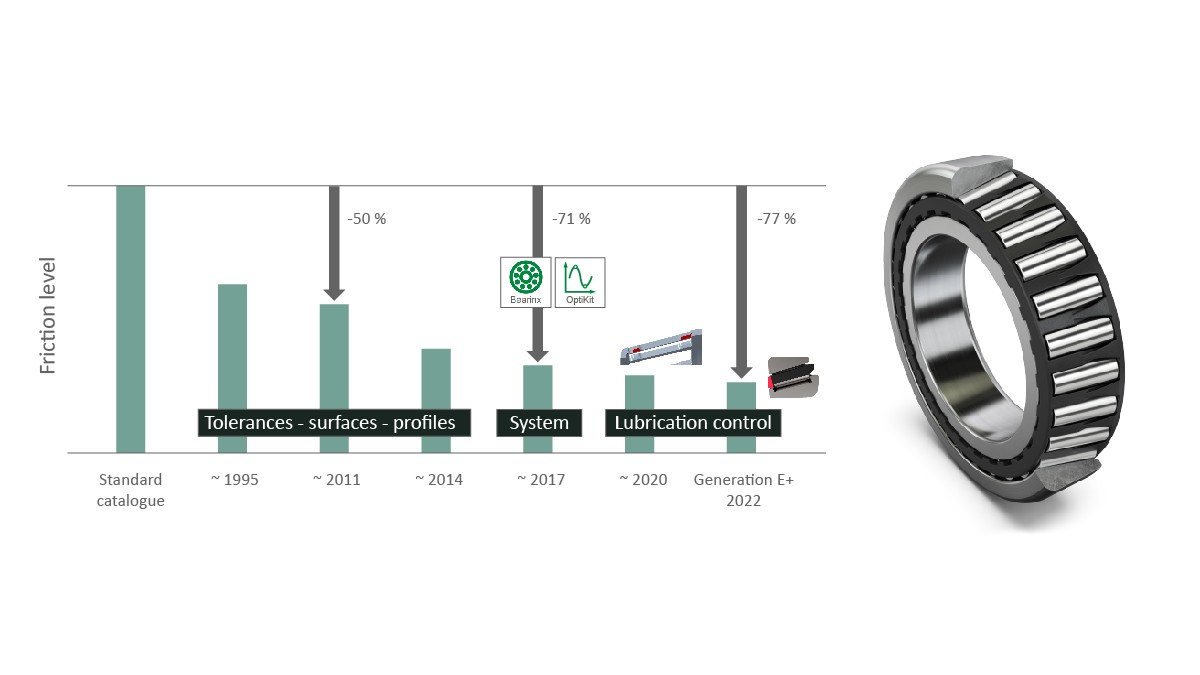
X-life品質を実現したジェネレーションCの円すいころ軸受は、現在広く普及している。X-lifeの要件を満たすために、形状、表面、寸法精度と回転精度、材料と熱処理のすべてを最適化した。ジェネレーションCの円すいころ軸受は、それまでより格段に滑らかな回転と低騒音が特長である。さらに改良を加えたジェネレーションDでは、大つばの接触角度、ころと大つばの接触を最適化した。ジェネレーションD+では、自社開発のOptiKit計算ツールを用いて使用個所ごとに最適化を行い、さらなる大幅な摩擦低減を実現した。ジェネレーションEとジェネレーションE+では、一層の効率改善を目指して保持器の設計を最適化している。ジェネレーションEでは保持器柱ところとの接触を改良し、ジェネレーションE+ではオイルの軸受内部通過量を制御した。ジェネレーションE+の円すいころ軸受は、標準品と比べて摩擦が77%低減される。加えて、Durotect Bによる化学的表面処理を施すことで、円すいころ軸受の世代を問わず、さらに摩擦を低減できる。
高電圧用途
高電圧の電動モータに転がり軸受を使用する場合、使用条件を機械的に検討するだけではシステム設計の観点から十分ではない。このような場合は、軸受の電気的特性も評価しなければならない(図9)。軸受の動作原理は、コンデンサと抵抗の等価回路図を用いると分かりやすい(図10)。
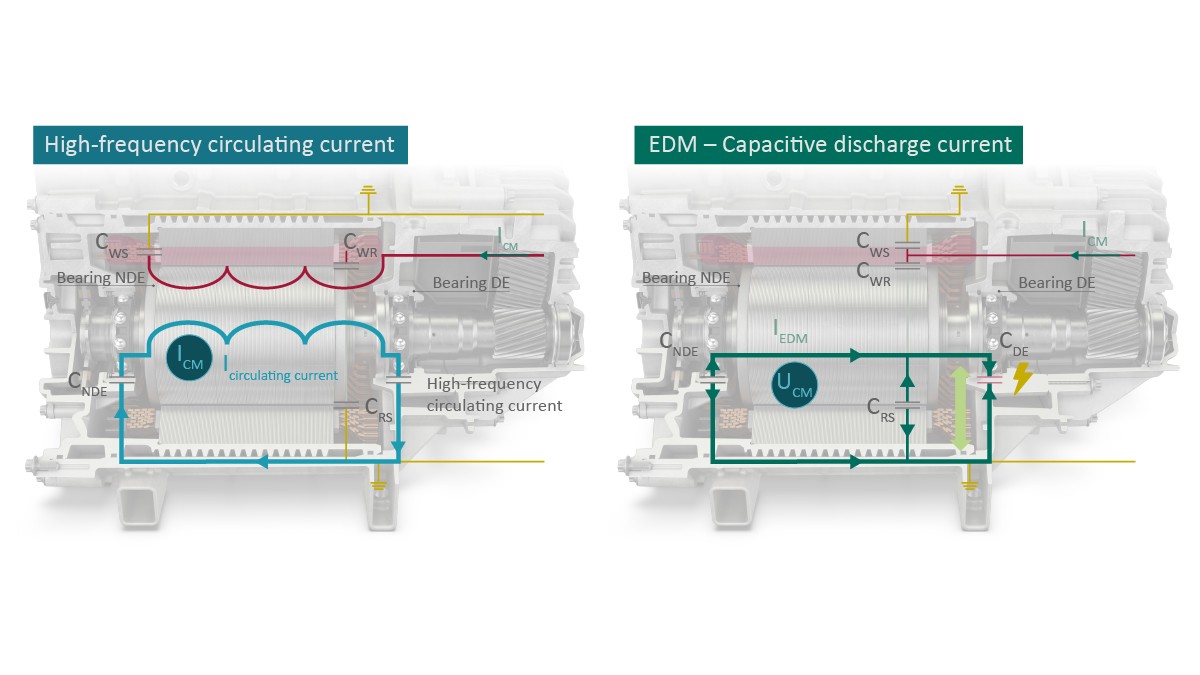
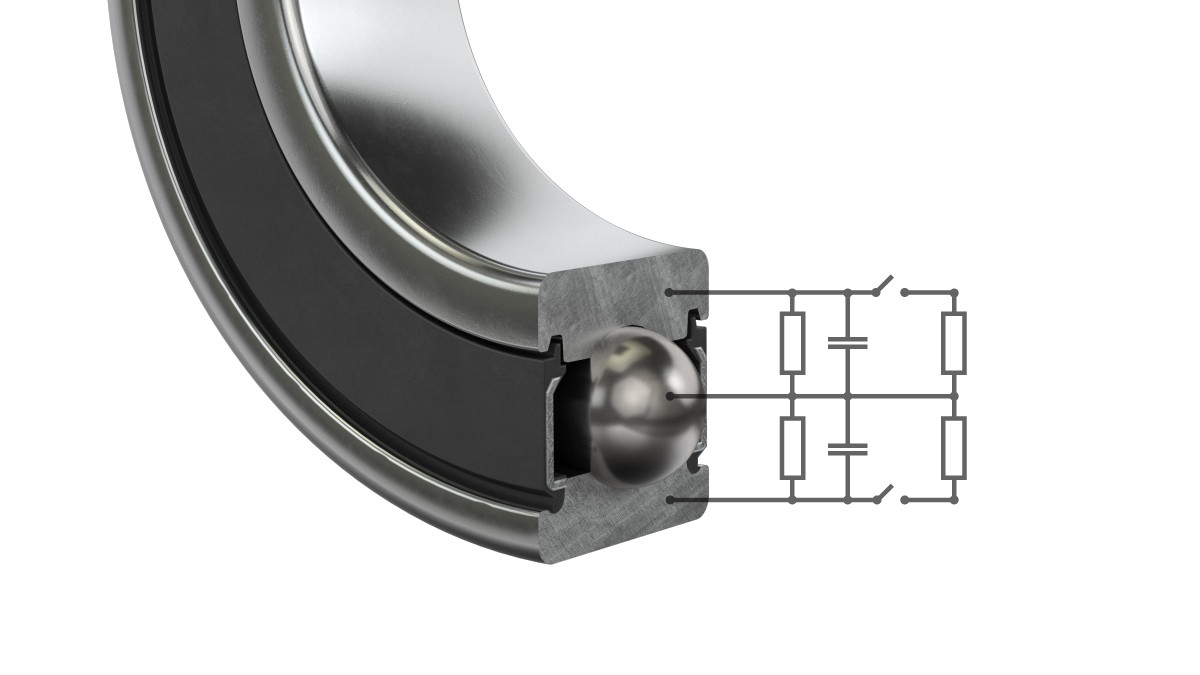
抵抗は、潤滑条件によって決まる。流体潤滑の場合は高抵抗となり、混合潤滑の場合はほぼゼロとなる。無制御の放電電流は、軸受不具合の原因となる。典型的な損傷として、金属表面の電食、軸受軌道面のフルーティング(リッジマーク)、潤滑剤の劣化、軸受鋼のミクロ組織に生じる亀裂(WEC:ホワイトエイッチングクラック)などがある(図11)。放電電流による電磁妨害のリスクも問題である。パワートレインの電気的特性が分かれば、軸受にかかる電気的負荷を計算し、軸受の開発段階で設計上の対策を講じることができる。各用途に応じて、電流のシャント、絶縁、またはその両方を併用した対策が可能である(図9)。
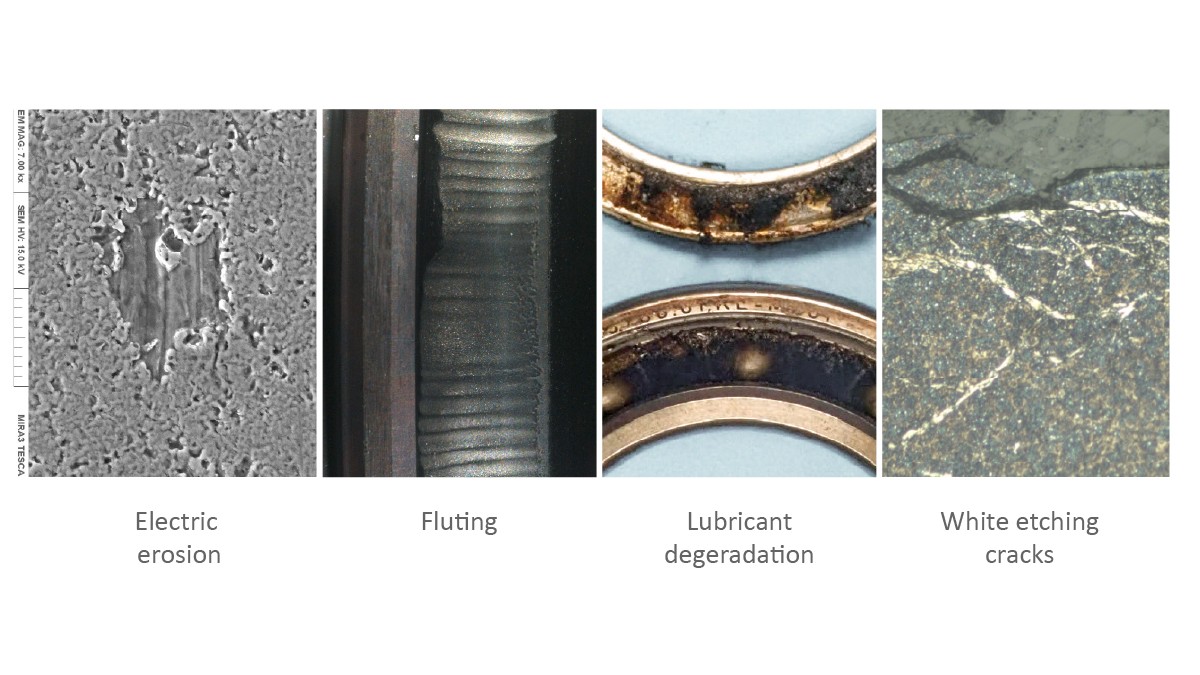
電流シャント
所定の放電電流(電流通過)を生じさせるためには、軸受の内輪と外輪の間、または軸と軸受ハウジングの間に継続的で確実な電気的接続が保証されていなければならない。現在の電流シャントとしては、スリップリング(シャントリング)のほか、カーボンピンやブラシなどのピックアップを使用する方法がある(図12)。ただし、いずれの方法も、モータ設計にアドオン部品として組み込み、パワートレイン組立時に取り付けなければならないというデメリットがある。また、乾燥した環境でのみ有効で、オイル環境では使用不可なものもある。軸受に特殊な導電性グリースを使用する方法もあるが、軸受の摩擦に悪影響を及ぼし、グリースが流出する際に導電性材料がモータ内に拡散する恐れがある。
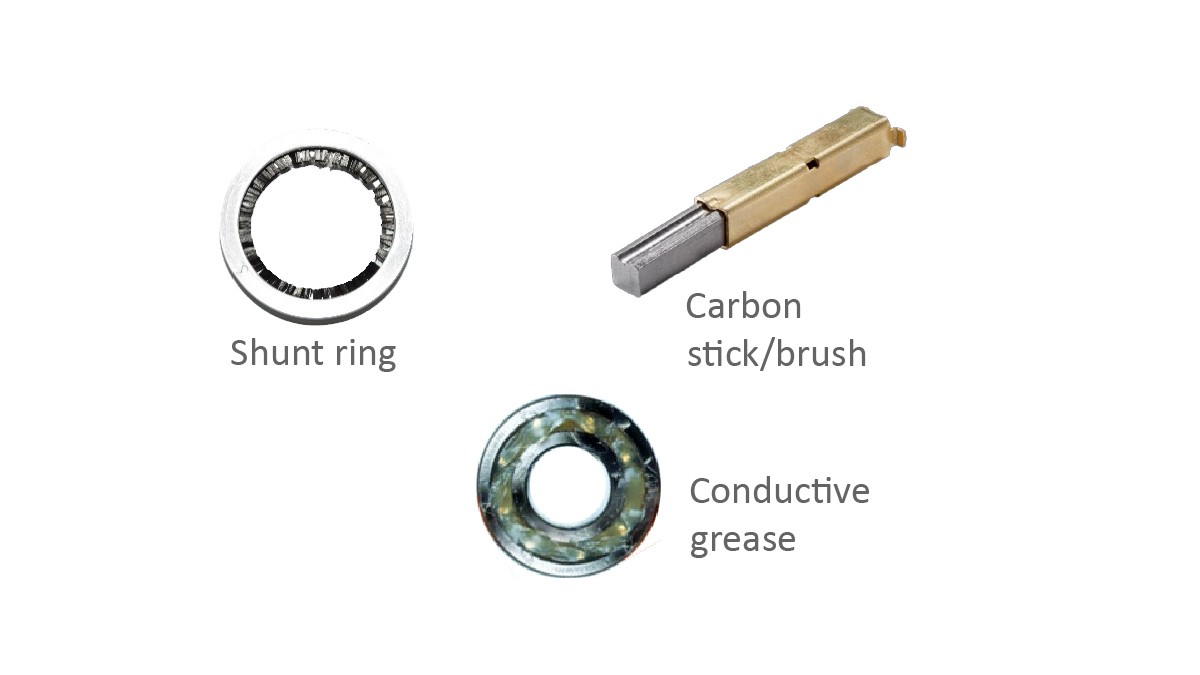
シェフラーは現在、シャント要素を内蔵した高速モータ用軸受を開発中である(図13)。ベースとなっているのは高速モータ用軸受である。軸受内輪のスリーブにコーティングを施し、このスリーブにシャント要素が接触する。ロータ軸受にシャント機能を統合することで、電流による損傷が発生しうる部位への電流を回避させることができる。電気的すべり接点の設計においては、摩擦・摩耗の増大と、あらゆる運転条件下での確実な導通とのバランスを確保しなければならない。現在、軸受のわずか5 mmの軸方向延長で、20,000 rpmの高速安定性を実現している。パワートレイン組立時には、軸受1点のみ取り付ければよいため、モータ製造工程の簡素化が可能となる。
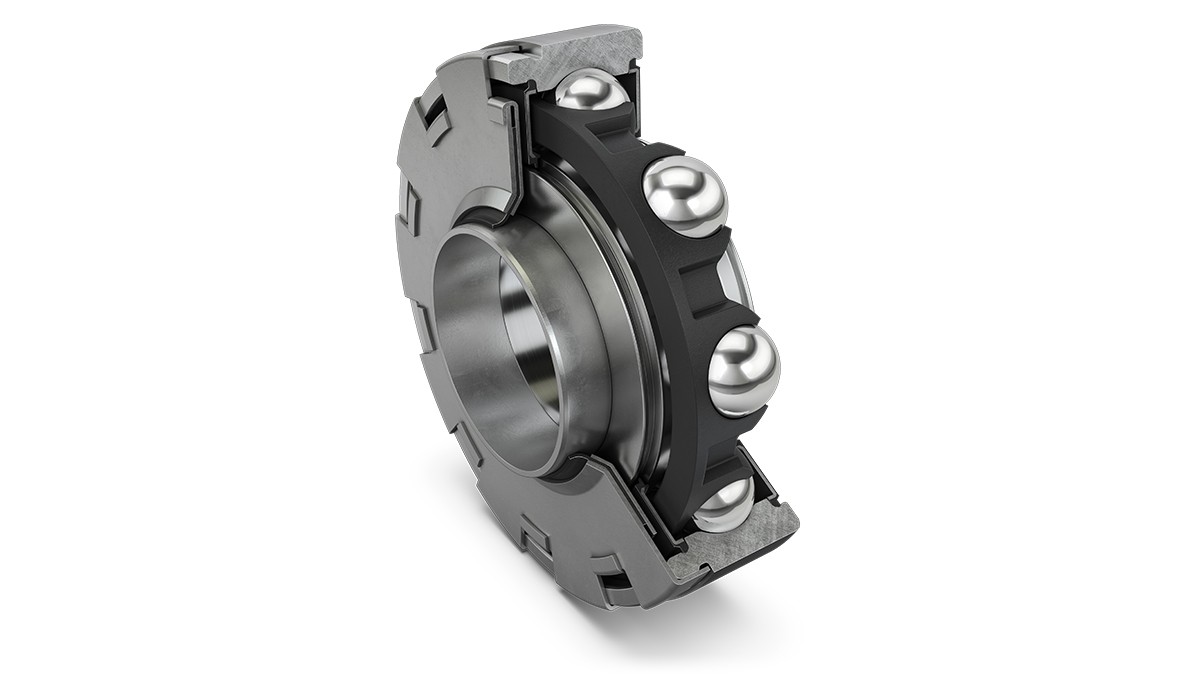
絶縁
電気的絶縁特性(電流遮断)を持つ軸受は、セラミックボールを用いたハイブリッド軸受か、セラミックコーティングを施した軸受として設計されるのが一般的である(図14)。
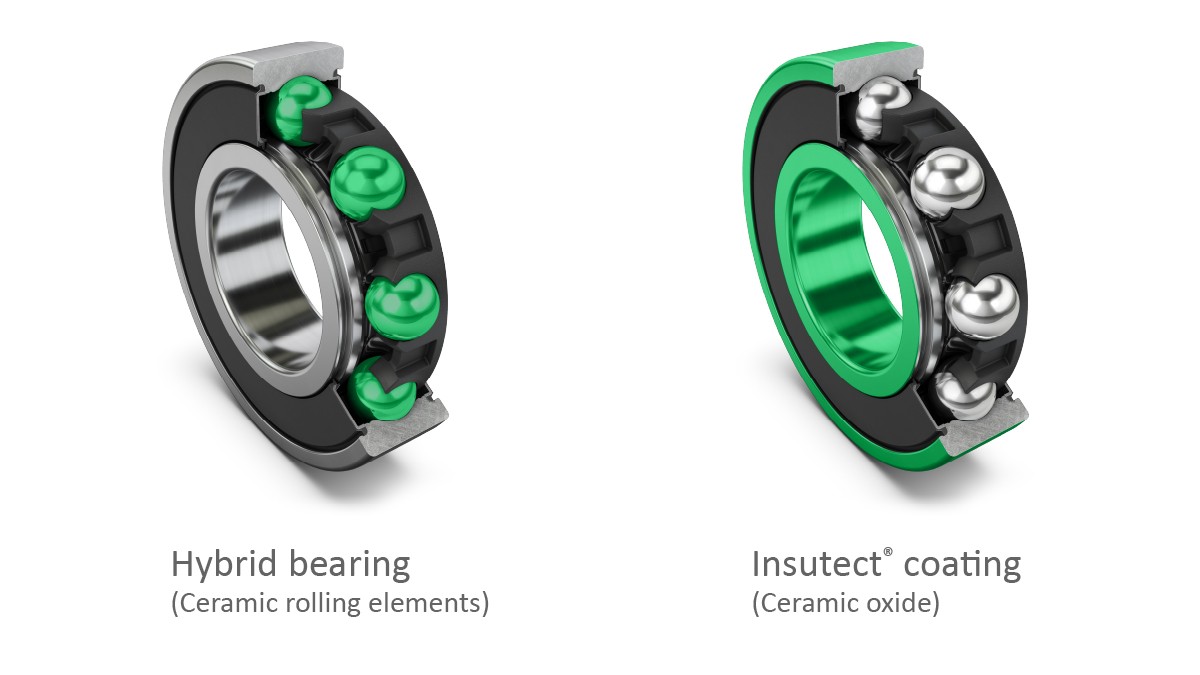
上記の軸受はいずれも、製造コストの上昇を伴う。高価なセラミック製転動体を使用するため、ハイブリッド軸受のコストは従来の高速モータ用軸受の5倍になることもある。同時に、ヤング率はセラミックボールの方が高いため、外部荷重が同じでも軌道接触部の接触応力は高くなる。外輪のセラミックコーティングは、コンマ数ミリの厚さにプラズマ溶射するので、コーティング後に外輪直径を研削し直す必要がある。
シェフラーの新しい絶縁方式は、同等の絶縁特性をはるかに低コストで実現する。外輪は外側を樹脂で被覆(オーバーモールド)する(図15)。採用した熱硬化性樹脂は、最高150°Cまでの高い機械的耐性と耐薬品性を備えている。この絶縁軸受は、従来の転がり軸受と同等の機械的特性(剛性、寸法精度、耐荷重性、速度安定性など)を持つほか、乾燥環境にもオイル潤滑環境にも対応している。通常の軸受を使用している軸やハウジングの設計を変更する必要なく、絶縁軸受と容易に交換できる場合が多い。
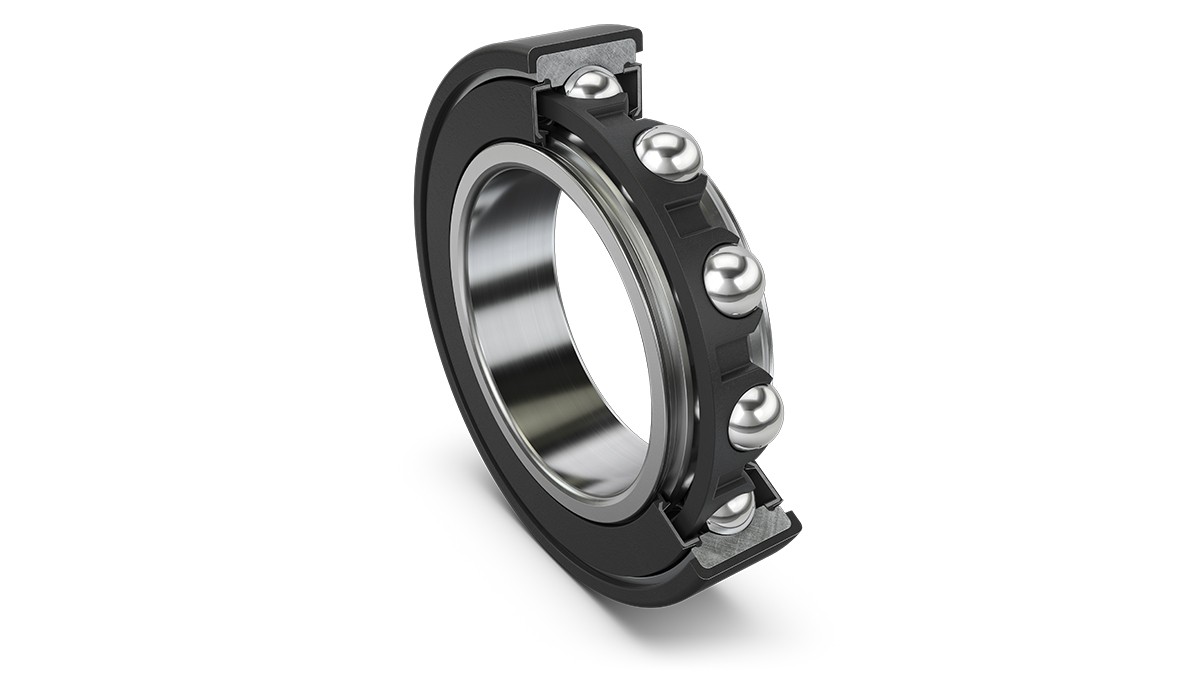
ホイール軸受の軽量化と摩擦低減
ホイール軸受には、質量と摩擦をさらに低減できる可能性がある。用途に応じて、いずれかのパラメータに設計上の重点を置けばよい。さまざまな要件を満たすため、シェフラーはホイール軸受の開発プロセスを次の3つのセグメントに分類した(図16)。
- 低摩擦を実現する複列ホイール軸受
- 高トルク伝達を実現するフェイススプライン搭載ホイール軸受
- 耐荷重性の高い3列軸受
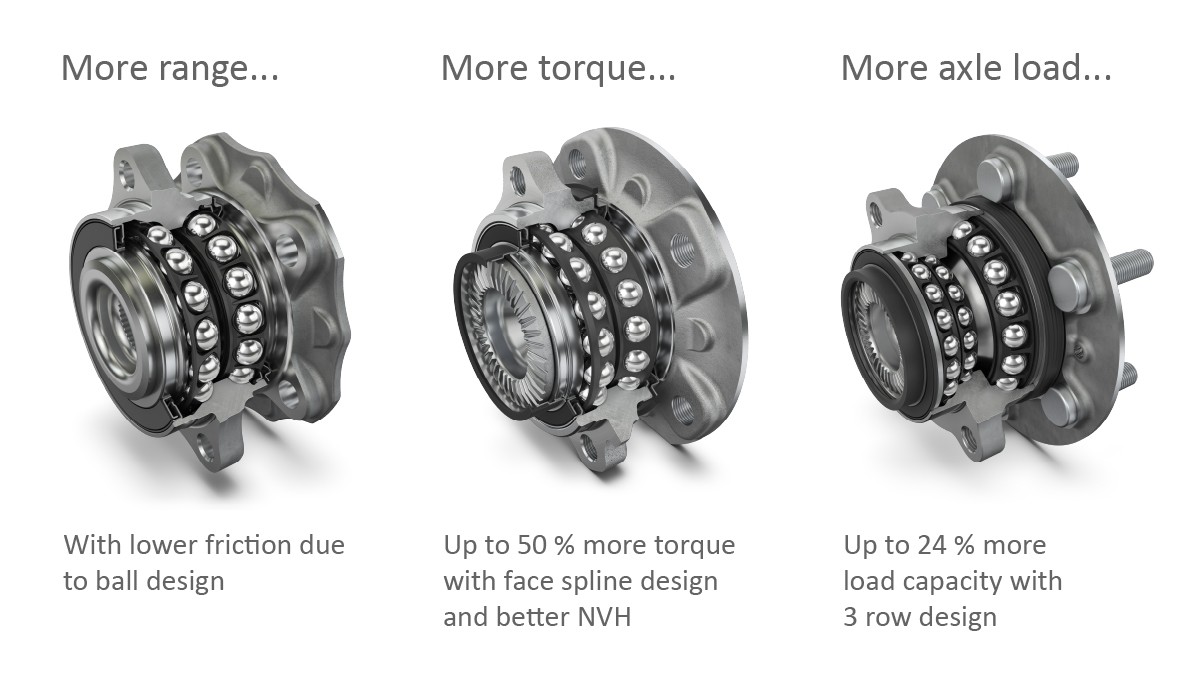
図16(左)の摩擦を低減したホイール軸受は、標準品と比べて摩擦を最大50%低減できる。エンジン車に使用した場合は、0.44 g/kmのCO2 削減が実現される。電動パワートレインの場合は、必要電気エネルギー量を0.6%削減することができる。これらは、シール設計の最適化、革新的な軸受グリースの採用、そして軸受内部設計の改良によって達成されたものである。
図16(中)に図示したクリアランスフリーのフェイススプライン搭載ホイール軸受は、同一寸法でありながら、駆動トルクの伝達を最大50%増大させることができる。同時に、軽量化、低騒音化を実現し、取り付けも容易となった。これらの改善点は電気自動車においては特に重要である。
シェフラーは、電動パワートレイン用に、図16(右)の3列ホイール軸受「TriFinity」を提供している。標準的な複列玉軸受と比較して、TriFinity軸受は、軸受寸法を変えることなく大幅な長寿命化と高剛性化を実現しながら、より大きな軸方向荷重に耐えることができる。この革新的な玉軸受は、予圧を与えた円すいころ軸受の代わりに使用することが可能である。円すいころ軸受を玉軸受に切り替えることで、摩擦トルクが大幅に向上し、FTP75サイクルで1車両あたり0.7%のエネルギー削減が実現される。さらに、シェフラーのフェイススプライン設計と TriFinity軸受を組み合わせた小型化ソリューションにより、ホイール軸受の小径化を実現できる。その結果、軸受とシールの摩擦が減少し、軸受重量が最適化され、CO2 エミッションが一層削減される。
軽量化のもう1つの方法は、ギヤホイールと一体化された軸受を使用することである(図17)。転がり軸受の外輪を圧入するのではなく、外輪軌道はギヤ内径に直接形成される。このため、軸受外輪は不要となり、材料が節約され、取り付けの手間も省ける。同時に、ピッチ円径や転動体サイズを大型化することで定格荷重を上げることができ、その結果、軸受全体の小型化も可能である。ギヤ軸受の量産は2022年の開始予定である。
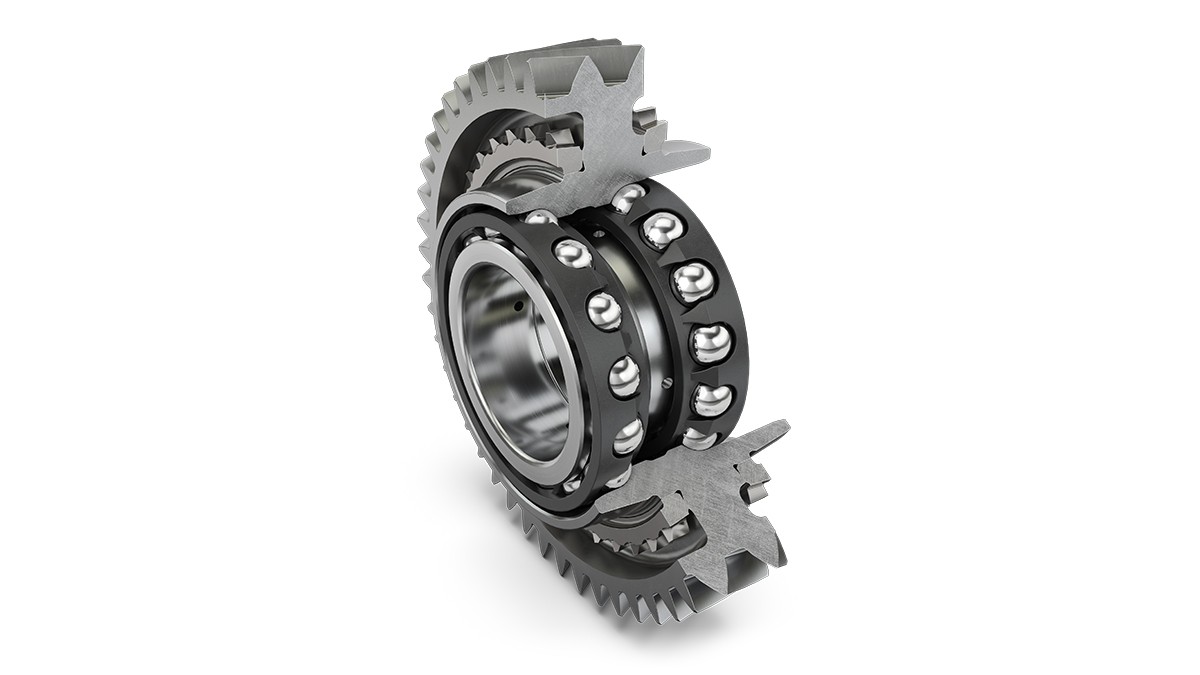
シミュレーションベースの開発
個々の使用条件に合った軸受を正しく設計する作業は、システム全体のコンセプト段階から始まる。周辺部品の設計と寸法決めを始める時点から、あらゆる荷重と使用条件を含めて軸受を検討しておくことで、あとになって時間と経費をともなう設計変更が生じるリスクを低減することができる。この考え方は、設計の初期段階に労力をかける「フロントローディング」と呼ばれ、その根幹となるのがシミュレーション技術である。シェフラーは、開発プロセス全体をサポートする一連の包括的シミュレーションツールを提供している。
シェフラーが開発しているBearinx Simulation Suiteは、Simpla、Bearinx、 Caba3D、Telosのプログラムモジュールで構成される。Simplaは、非線形多次元連成軸受モデルとのハイブリッドマルチボディシミュレーション(MBS)を用いて、システム全体の動的挙動を再現する。MBSモデルは、既存のBearinxモデルから導出可能である。Bearinxにより、 あらゆる形式の軸受、複雑なシャフト形状、ならびにトランスミッション全体のシャフトシステムまでをモデル化し、計算することができる。軸受寿命の計算には、軸受の剛性、シャフトの弾性、シャフトおよびハウジングとの接続状態、軸受の運転すきまや予圧、ころおよび軌道面のプロファイル形状、軌道面の潤滑、実際の接触応力などが考慮される。Caba3Dは、転がり軸受の動解析ツールで、例えば、転動体や内外輪に生じる力やその運動、保持器の動的挙動、摩擦による動力損失、転動体の加速挙動を計算する。Telosは、転がり接触に特化したシミュレーションプログラムで、一般的な潤滑条件下のほか、準静的荷重下や、荷重変動時における接触点の詳細解析を行う。Telosは、コーティングのある表面にも対応している。
Bearinxの最初のバージョンがリリースされたのは1997年で、このとき初めて個別の転動体の接触にいたるまでの正確な軸受計算が可能となった。それ以降、シェフラーは絶えずBearinxを進化させ続け、最新のBearinx Simulation Suiteはすべての軸受開発の標準として使用されている。
まとめ
現在の自動車業界で注目されるのは、パワートレインの電動化の進展である。電気自動車(BEV)向けパワートレインの分野では、航続距離の延長と充電時間の短縮が開発の焦点となっている。そのパワートレインには、軽量化や動力損失の低減、電動モータの最高回転速度の増加、システム電圧の800Vへの引き上げなど、さまざまな性能が求められている。ここで、転がり軸受はパワートレインの機能を向上し、新しい技術ソリューションを実現するために重要な役割を果たす。シェフラーは、軸受をシステムの中の一つの要素と捉え、複数のシミュレーションツールを使用することにより、さまざまな要求に対し最適なソリューションを提供している。
例えば、従来のころ軸受の耐荷重性に、高速モータ用軸受の特性を組み合わせた新しいころ軸受を開発した。また、遠心ディスクを備えた革新的な玉軸受は、さらなる効率向上を実現する。ディスクは、軸受内に流入するオイル量を制限し撹拌損失を低減するとともに、シール摩擦を生じることなく軸受内部への異物混入を効果的に防止する。さらに、ホイール軸受においては、内部設計の最適化によって軽量化を図り、システムの小型化を実現した。軽量化と低摩擦化により、電気自動車の航続距離が延長する。加えて、最大電圧800Vの高電圧システム、つまりシリコンカーバイド(SiC)半導体を使用したパワーエレクトロニクスの登場により、電動モータ用軸受には特別な性能が要求されている。モータ稼働中に放電電流が発生すると不具合の原因になる。この放電の課題に対し、シェフラーは、放電電流による軸受やギヤ部品の損傷を防止するため、短絡して電流を逃がすシャント機能や、逆に確実に電流を遮断する絶縁機能などのソリューションを提供している。こうしたイノベーションや革新的な改良によって、シェフラーの転がり軸受は常に最先端を維持し、そして進化し続ける。
[1] Homm, M.: Fascination Electric Powertrain. Bühl: Schaeffler Kolloquium, 2022
[2] Völkel, F., et al.: Rolling into the Future – Bearing Solutions for Electric Mobility. 20th International VDI Congress “Dritev – Drivetrain for Vehicles,” 2020.