アクチュエーションと循環 - パワートレインの動脈 次世代アクチュエータシステム
Mathias Göckler | Peter Biegert | Marco Grethel
パワートレインの効率を向上させるためには、車両走行状況に応じた最適な運転条件の設定が不可欠であり、その点においてインテリジェントなアクチュエータ技術の重要性は増していると言える。個別タスクや分散タスクの実行には電気機械式アクチュエータが最適だが、油圧式アクチュエータは温度制御や潤滑機能など複雑なアーキテクチャ制御に適している。シェフラーは、パワートレインとアーキテクチャに求められる個別機能要件に対応する革新的アクチュエータシステムソリューションを提供している。新しいアプリケーションへの対応を柔軟かつ迅速に、高い費用対効果で実現するため、シェフラーは「スマートハイドロリックアクチュエータキット」を開発している。油圧式アクチュエータを構成するソフトウェアとハードウェア、そして生産技術をキット化し、製品の構想から生産まで付加価値を生み出すバリューチェーンを構築する。電気機械式アクチュエータについても、シェフラーは技術を次の段階へと進化させる開発を行っている。さまざまなアクチュエーションタスクに対応するソリューション拡充に注力し、充実した製品ポートフォリオを提供する。
アクチュエータが担う機能
パワートレインにおけるアクチュエータの主な役割は、走行状況に最適な運転点を設定することにある。例えば、ハイブリッド専用トランスミッションにおいては、パラレルモードとシリーズモードの切り替えであり、電動アクスルでは、車両を安全に停止させるパーキングロックの作動がそれにあたる。一方で、現代の駆動システムの場合、理想的な運転点は走行モードの切り替えだけで達成されるものではない。パワートレインの最適温度管理と潤滑も運転点を左右する重要要素である。現代のパワートレインは高効率で、熱損失も少ない。言い換えれば、利用できる熱エネルギーが限られており、これを最大限回収し、車両全体に効果的に分配する必要がある。駆動システムの冷却と加熱を行い、そして車両の必要とされる場所に熱を届けることで、最適な温度環境を確保する。
油圧式アクチュエータに求められるのはスレーブ機器の作動と、オイルによる冷却と潤滑だ。油圧式アクチュエータ開発では、シンプルな構造と消費電力の最小化、そして高い費用対効果が求められる。また、車両全体の効率性と運転の快適性を確保するためには、スレーブ機器作動の協調を開発段階で入念に確認することが重要だ。シェフラーは、単純なタスクを実行するアクチュエータから複雑な制御を処理する高性能タイプまで取り揃えた油圧式アクチュエータモジュールを提供しており、幅広いパワートレインアーキテクチャの要件に対応している。
油圧式アクチュエータの代わりに電気機械式アクチュエータを使用することも可能だ。シェフラーは電気機械式アクチュエータについても幅広い要件に応えるソリューションを提供する。トランスミッションで多様なタスク処理を行うアクチュエータでは、圧力制御と各スレーブ機器への動力分配を1つの油圧システムに集約することで、より多くのメリットを得ることができる。
アクチュエータ技術への影響
油圧式アクチュエータ要件や機能は、パワートレインによって異なる[1]。電動アクスルのシンプルなトランスミッションでは、油潤滑と冷却の他に求められるのは、1つの機能のみである。例えば駆動輪側電動アクスルに搭載されるパーキングロック機能や、二次駆動側電動アクスルのディスコネクトユニットなどが該当する(図1)。シェフラーの「マルチモードハイブリッドトランスミッション」[2, 3]などハイブリッド専用トランスミッションの場合は、これにクラッチ断接などスレーブ機器の作動も含まれる。パワーシフト式多段変速機構やトルクベクタリング機能を備えた電動アクスルのような特に複雑なパワートレインの場合には、複数の異なるスレーブ機器を同時に制御する必要がある[4]。
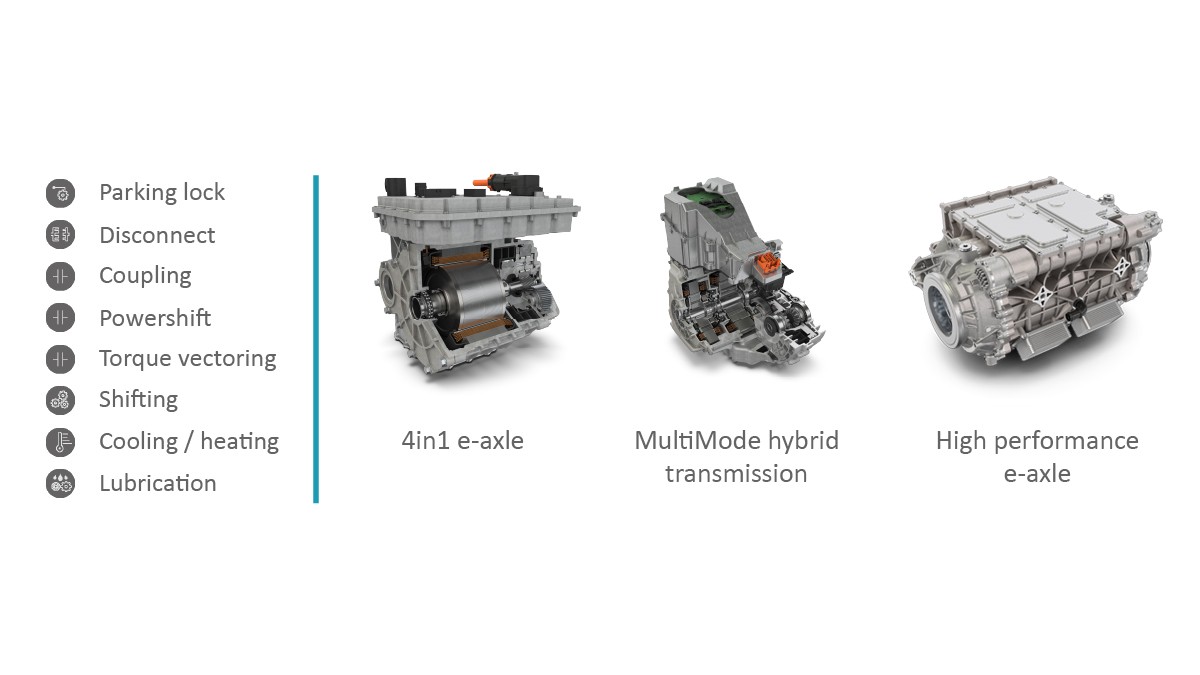
油圧アクチュエータの機能
パワートレイン形式にかかわらず、スレーブ機器の作動と温度制御/潤滑用のオイル循環はアクチュエーションシステムの必須機能である。図2が示す通りアクチュエータへの要求は増大している。図は左から右へ順に、1つの機能追加(Cooling+1)、2つの機能追加(Cooling+2)、そしてより多くの機能(Cooling+x)の同時制御へとアクチュエータに対する要件が拡大していることを示す。トランスミッションの潤滑および冷却/加熱用オイル循環機能には連続運転が必要である。アクチュエーションシステムに必要な連続出力レベルは、これら機能の要件によって決定される。一方、作動制御機能においてアクチュエータ出力は短時間定格(ピーク出力)となる。従って、例えば巡航走行時にスレーブ機器を連続して動作させるシステムは好ましくない。
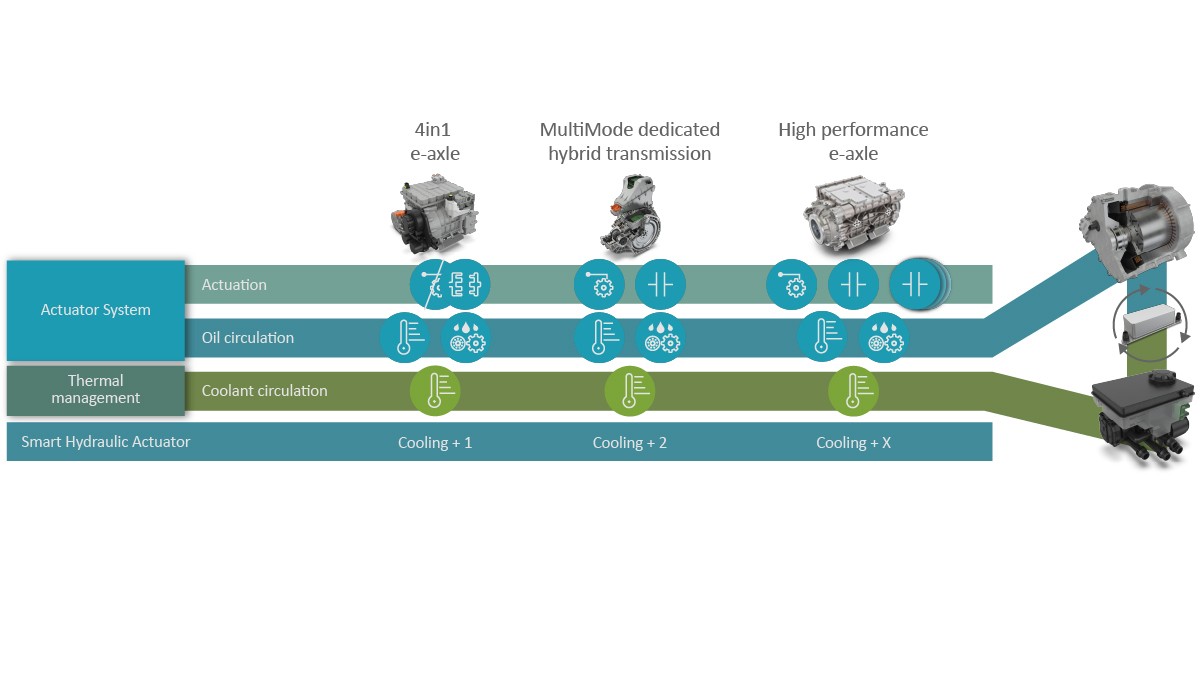
- オンデマンド式流量制御:冷却油供給を完全なオンデマンド式とすることで効率性を高め、サーマルマネージメントシステムとの連携で最適な温度制御を実行する。
- オンデマンド式油圧制御:巡航走行時にはスレーブ機器と断接し消費電力を抑え、それぞれの走行サイクルに最適な効率性を確保する。
- 作動要件のバランス:費用対効果を最大限高めたアクチェータシステム設計とするために、機器それぞれの作動点における最大電力消費と機器作動の協調を見極め、最適なポンプ駆動ユニットを選択する。
- シンプルな構造:構造をシンプル化することで部品点数やインターフェースを削減し、開発・システムコストを低減する。
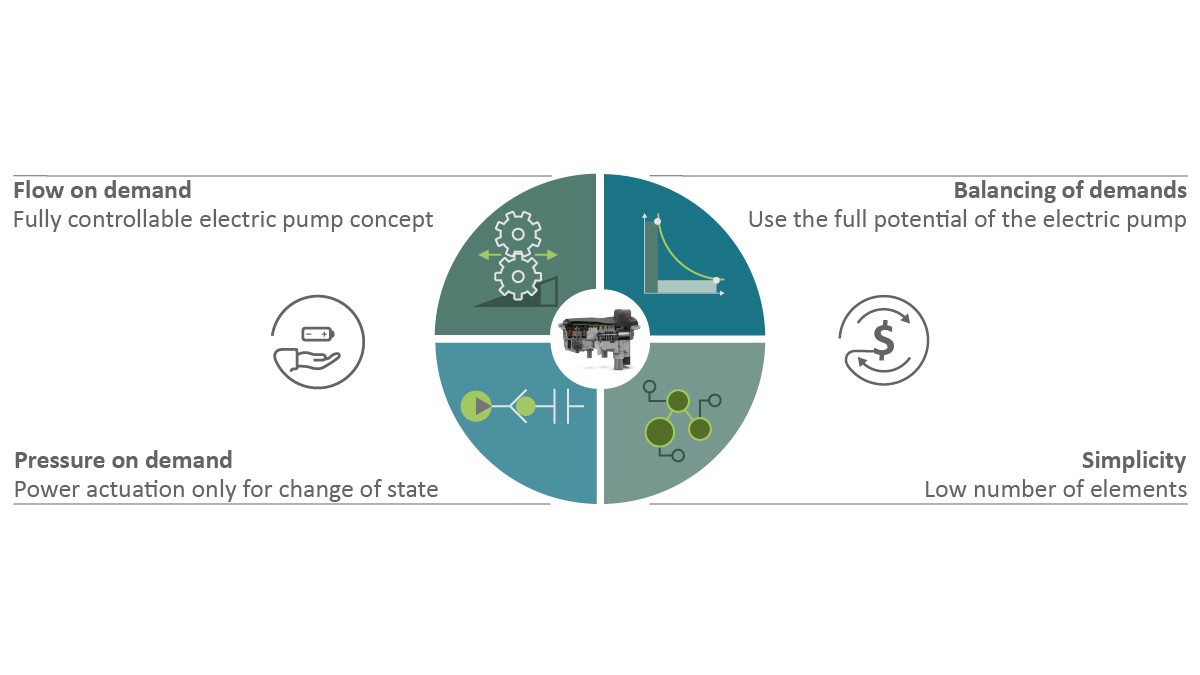
Electric pump actuator(EPA)に採用されているポンプ逆転原理については、前回2018年に開催されたシェフラーシンポジウムで紹介した[1, 5]。シェフラーは近年この技術を進化させ、Smart Hydraulic Actuator(SHA)シリーズに採用している。モジュールシステムをベースとすることで、幅広いタイプの油圧アクチュエータとさまざまな拡張機能を迅速に、そして容易に提供することができる。最もシンプルなトランスミッションコンセプトである「Cooling+1」では、ポンプ逆転原理を用いることで、アクティブバルブの追加なく熱循環とスレーブ機器の動作という2つのタスクを処理することが可能だ(図4)。EPAには2方向バルブが組み込まれており、ポンプは両方向から吸入し、吸入側とは反対側のポートを閉じる。ポンプは両方向に回転し、例えば正転時に冷却機能、逆転時にスレーブ機器の作動制御を行う。ピストンの終端位置もしくは特定の位置に保持する機構を追加している。そのため、ピストンの作動が完了すれば、ポンプは再び冷却に使用することが可能になる。
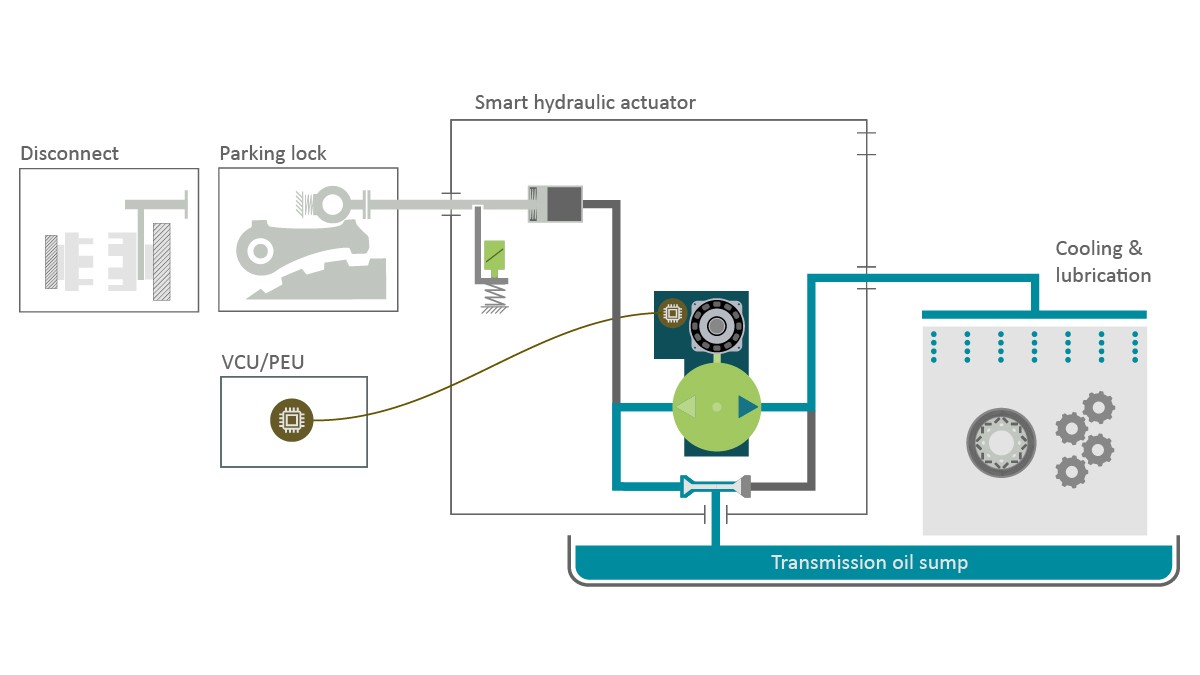
第3のアクチュエーション機能を追加した「Cooling +2」では、システムの複雑性がやや高くなる。図5に示すSmart Hydraulic Actuator (SHA)は、複雑性を最小限に抑えるソリューションであるが、逆転時に片方のスレーブ機器に油圧を送るためのアクティブバルブが追加で必要となる。
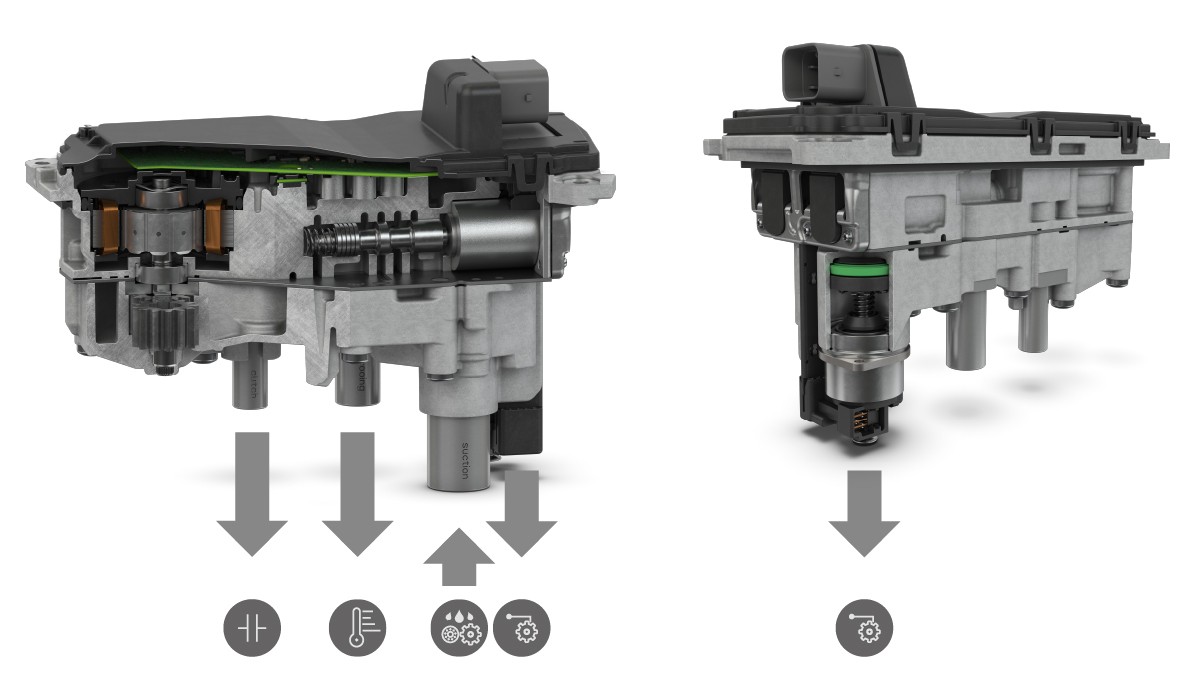
このSHAには吸入側にパッシブタイプの2方向バルブ1基、もしくはチェックバルブ(逆止弁)2基を装備し、接続する2つのポート双方に圧力を連続して供給する。ポンプ正転時にはクラッチなどの駆動デバイスに圧力供給する。クラッチの場合、この圧力供給により締結する。図6が示す通り、ポンプ逆転時にはチェックバルブがクラッチ側圧力を維持しつつ、反対側ポートに圧力を供給し冷却を実行する。クラッチ側圧力が閾値を下回ると、冷却機能は一時的に停止し、同時にポンプが再び正転し、クラッチ側圧力を増加させる。クラッチ開放はドレンバルブが制御する。この際、ポンプを回転させる必要はない。クラッチをアキュムレータとして利用するこの方法は、アクチュエータ開発時の前提条件に挙げた「オンデマンド式油圧制御」の1例と言える。アプリケーションによっては、終端位置の保持を保障する必要がある。例えば、パッシブに作動する電気自動車のパーキングロック機構がこれに該当する。この場合、一定の電力供給を継続が必要となる電磁石を用いるか、もしくは油圧制御による保持機能、いずれかの技術を検討することになる。
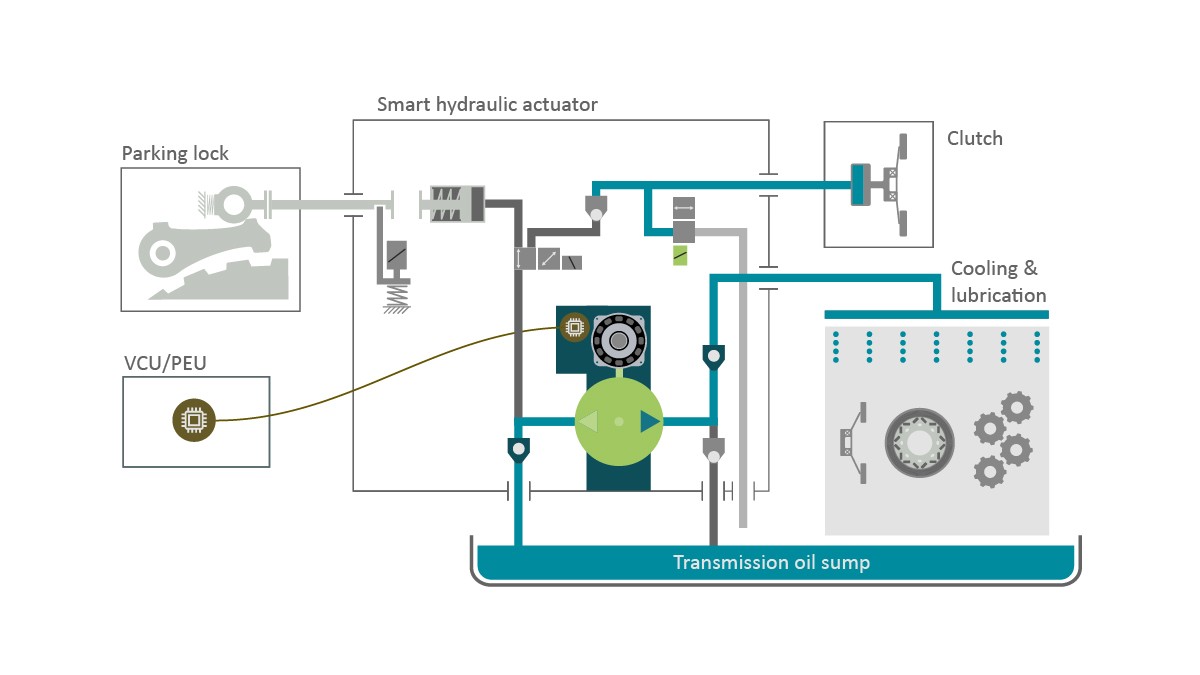
クラッチのように緻密な制御を必要とする機能を同時に動作させる「Cooling+X」システム(図7)を実現するには、また別のコンセプトを必要とするが、いずれにしても前述した設計上の前提条件となる4つの要素に変わりはない。基本となるアーキテクチャは図示するアプリケーションに限られるものではなく、モジュールベースで拡張することができるので多くのパワートレインへの適応が可能だ。
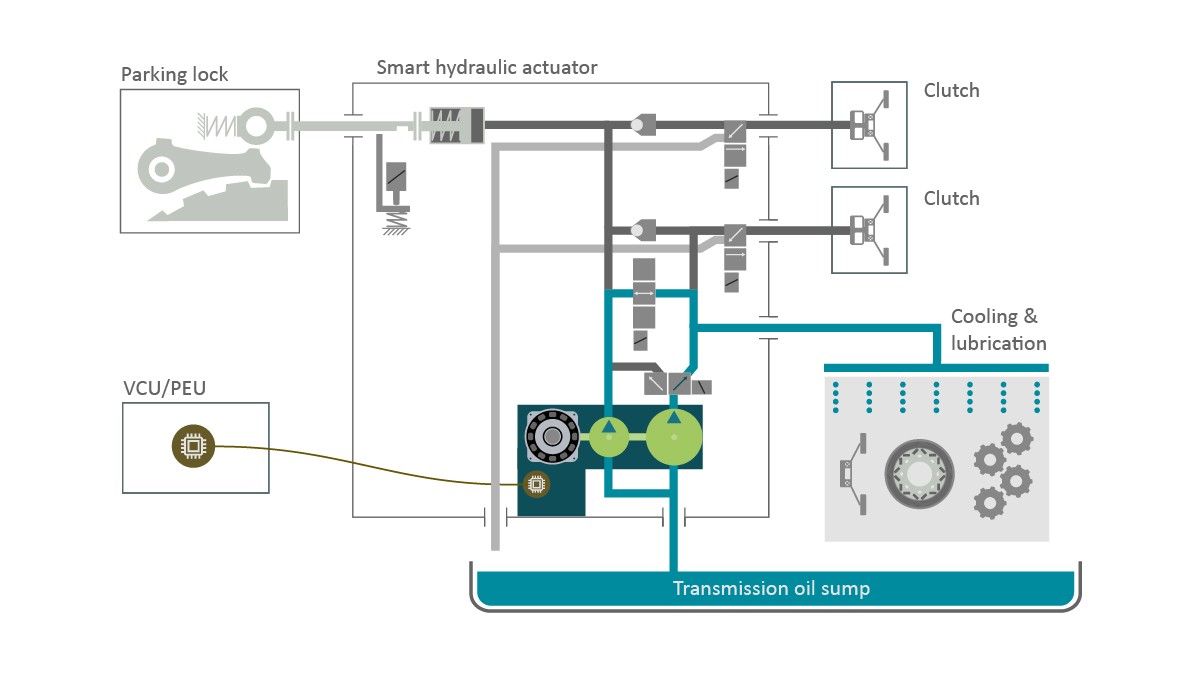
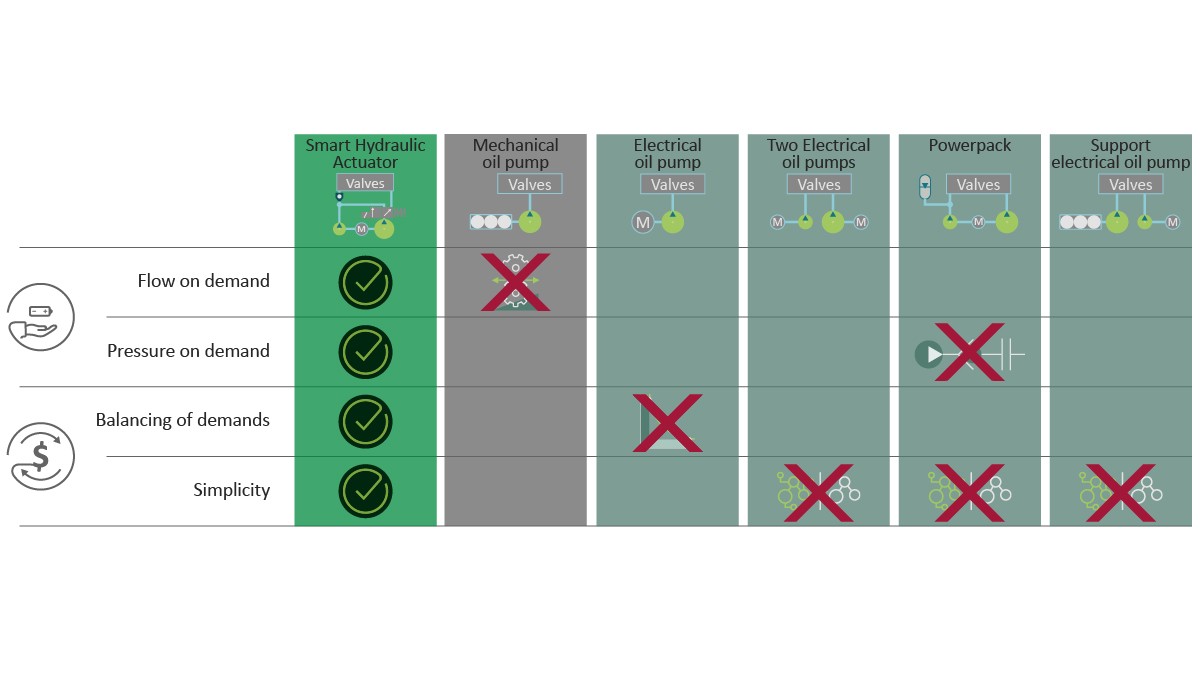
パワーシフト式電動アクスルに必要とされるアクチュエーションシステムでは、電動もしくは非電動の機械式ポンプか、電動ポンプ単体もしくは電動ポンプと油圧アキュムレータを組み合わせたソリューションが考えられる。いずれの場合もポンプは1基もしくは2基とし、それぞれに専用のモータを配備するか、もしくは1つのモータで2基を駆動するタンデムシステムも可能だ(図8)。上記比較表が示す通り、シェフラーはタンデムポンプシステムと電動バルブの組み合わせで開発を進めており、アクチュエーションシステムの設計に求められる4つの要素もすべて満足することができる。その他のソリューションと比較して、シェフラーのシステムはよりシンプルな設計で高い効率性を達成し、低コストで提供することが可能だ。鍵となっているのは、タンデムポンプとブーストバルブの最適設計、そして革新的な制御システムである。当設計では、アクチュエータの油圧ポンプの吐出量は、スレーブ機器の作動に必要最低限のレベルとなるよう設計されている。これにより、システムプレッシャレギュレータを介して冷却排出されるオイル吐出量を最低限とすることが可能になる。一方で、クラッチなどの作動制御に流量を短時間増加させる必要がある場合には、ブーストバルブを介し追加の流量を供給する。この際、冷却油ポンプにも極めて短時間ではあるが圧力が増加する。ブーストバルブとポンプ駆動を適切に制御することで、走行中の電力消費を最低限に抑えながら必要な応答性を達成することが可能になる。
消費電力解析
シリーズパラレル式ハイブリッド車をWLTP(Worldwide harmonized Light vehicles Test Procedure)で評価した際の「Cooling+2」SHAの消費電力計測結果を図9に示す。全走行モードを通して、油圧ポンプの電力消費量はパワートレインの冷却油量(青線)に大きく左右される。走行開始時にパーキングロックが解除されると、パーキングロックの作動消費電力はゼロとなる(黄緑線)。走行中はクラッチの接続を行うたびにピーク電力が短時間発生する(緑線)。クラッチ作動時にはトランスミッション冷却が短時間停止するが、サーマルシステムそのものへの影響は限定的であり、むしろ過負荷を防止するというメリットをもたらす。総消費電力(黄線)にもそれが表れている。過負荷は油圧システムにも悪影響を及ぼす可能性があり、設計時には考慮すべき特性の1つである。
これらの相互作用を明確化するために、左図の灰色部詳細を右図に示す。詳細図でわかる通り、クラッチ作動時には確かに電力消費量が短時間増加する。また、同時に冷却油供給が減少する。このスレーブ機器作動に電力が供給されるのはごく短時間であり、つまり、システム全体の電力消費量に与える影響は少なく、また、WLTPにおけるCO2排出量にも大きな変化は見られない。走行サイクル全体におけるアクチュエータシステムの平均消費電力わずか12Wであった。この値は市場でオンデマンド式と言われる多くのアクチュエータの電力量を下回っている。
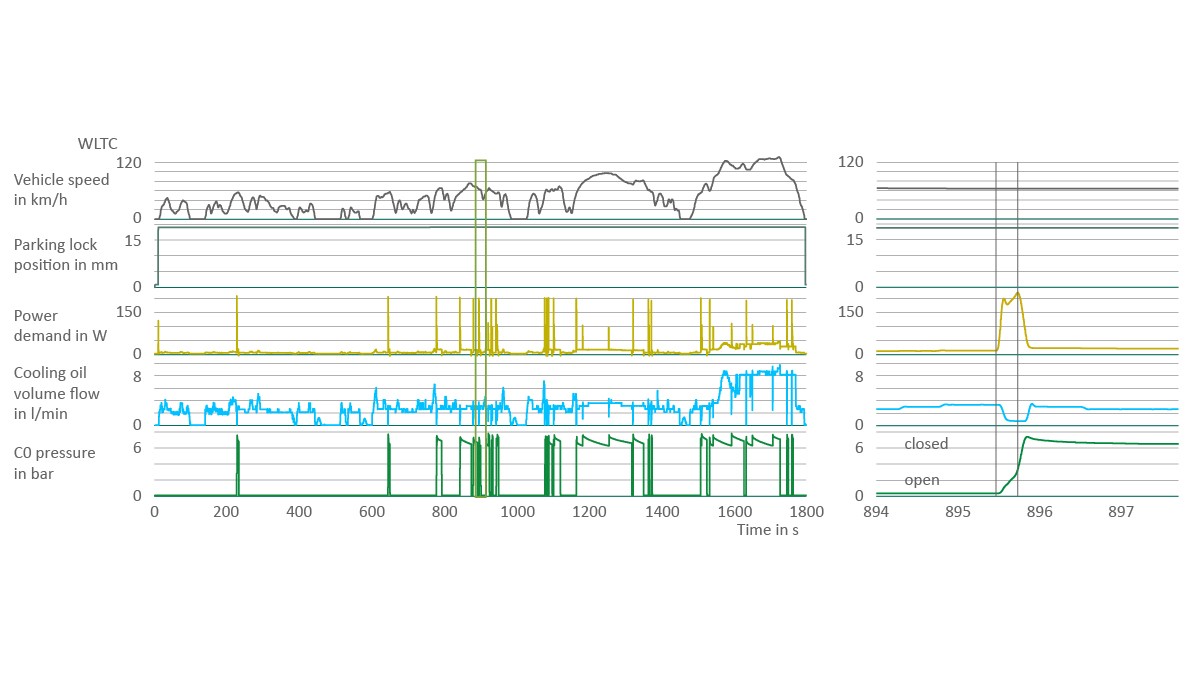
ソフトウェアとハードウェアのキット化
アクチュエータのコストパフォーマンスを判断する際には、設計、試験、製造コストの他に、全体システムへの実装費用、さらにはオペレーションコストまで考慮する必要がある。これらコストを削減するには、次の3つの方法がある。1つ目は標準化されたソフトウェアコンポーネントの再利用。2つ目は既に開発済みのハードウェアの利用。そして3つ目は生産プロセスの共有だ。新たなアプリケーションへの対応を柔軟かつ迅速に、そして高い費用対効果で実現するために、シェフラーはソフトウェアとハードウェアの標準的なソリューションをモジュール化し、SHAを開発している(図10)。異なるプロジェクトやお客さまに提供するソリューションを横断的にプラットフォーム化することで、ソフトウェア/ハードウェアの再利用率を高め、バリエーション数を抑え、部品の生産効率を高めている。
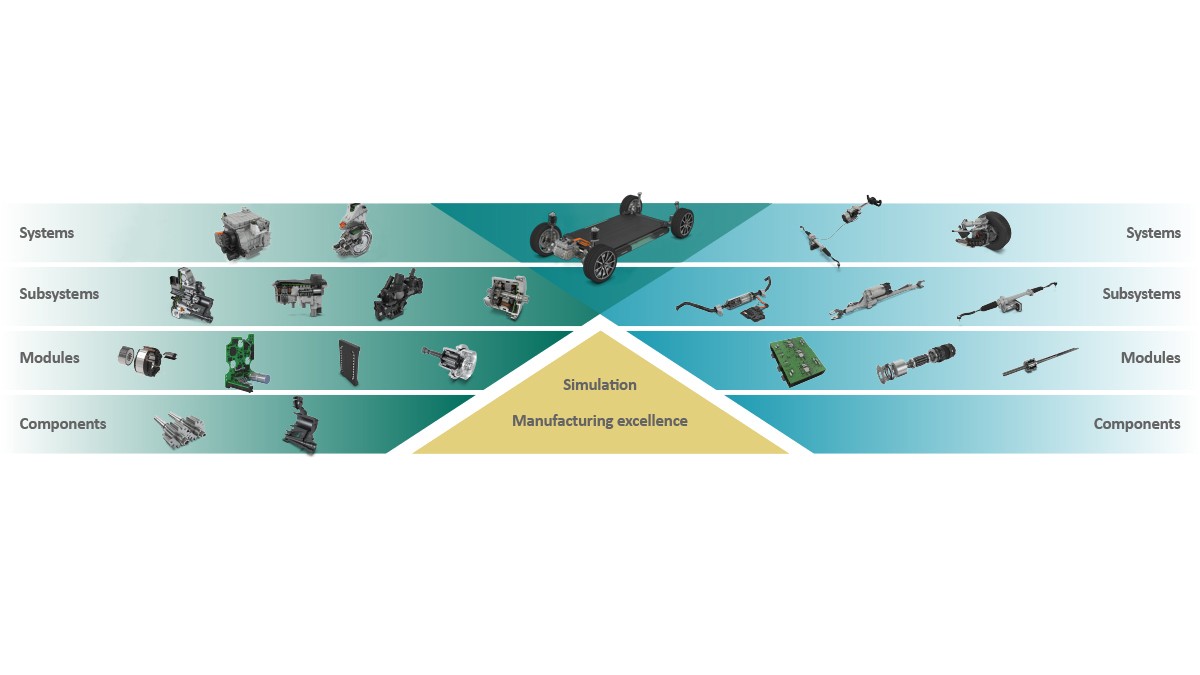
量産ソフトウェアの開発がシェフラーでもこの数十年増加しており、開発業務全体に占めるソフトウェア開発の割合が非常に大きくなっている。機能安全やサイバーセキュリティ需要の急速な拡大とソフトウェアへの要求の複雑化により、広範なドキュメンテーション作業が必要となり、開発負荷が増加している。
ソフトウェアは、システム全体から個々のコンポーネントにいたるまで、あらゆる機能レベルを制御するものであり、アクチュエーション技術に不可欠な要素だ。そのため、ソフトウェアは階層別に機能分解しモジュール化している。特定アプリケーション向け機能を担うソフトウェアモジュールを上位層で追加することで、幅広いSHA機能を実現することができる。
モジュール化ソフトウェアを利用するには、ハードウェア技術基盤の統一が必要だ。モータや各機器の動的挙動、センサなどは複数のアクチュエータで同一、もしくは少なくとも同等のコンセプトで設計されていなければ、ソフトウェアの再利用促進によるプログラミングコストの大幅削減は難しい。
シェフラーは、生産の垂直統合およびプロセス開発が企業の発展を支える重要な要素であると考えている。新技術の迅速な量産化や柔軟な生産能力の確立には、モジュール生産方式の導入や、試作部門と量産部門の緊密な連携が必要だ。こうした生産基盤を整備することで、変化する市場に迅速に対応することが可能になる。
こうしたノウハウを支えるのがエレクトロニクスおよびパワートレインシステム全般を網羅する知見だ。シェフラーはこの分野に関する技術力を、何十年にもわたって拡大し、積み上げてきた。場合によっては戦略的買収を実行し必要な能力を補完してきた。その結果、シェフラーはアクチュエータ駆動用の小型モータから電気自動車向けの大型トラクションモータまで、あらゆるサイズのモータを自社で開発・生産することが可能な技術力を完備することができた。垂直統合生産の一例として、アクチュエータ向けブラシレスモータを紹介する。ステータ用鋼板のプレス加工からワインディング、そして最終工程のオーバーモールドまで、すべて社内で統合生産を行っている。
パワートレイン全体に対する総合的な理解に基づき、機能統合を図っている。このように包括的な知見によって、お客さまの要件に最適なアクチュエータシステムを把握することが可能となり、SHAモジュールシステムを活用したソフトウェアおよびハードウェアの設計が実現する(図11)。
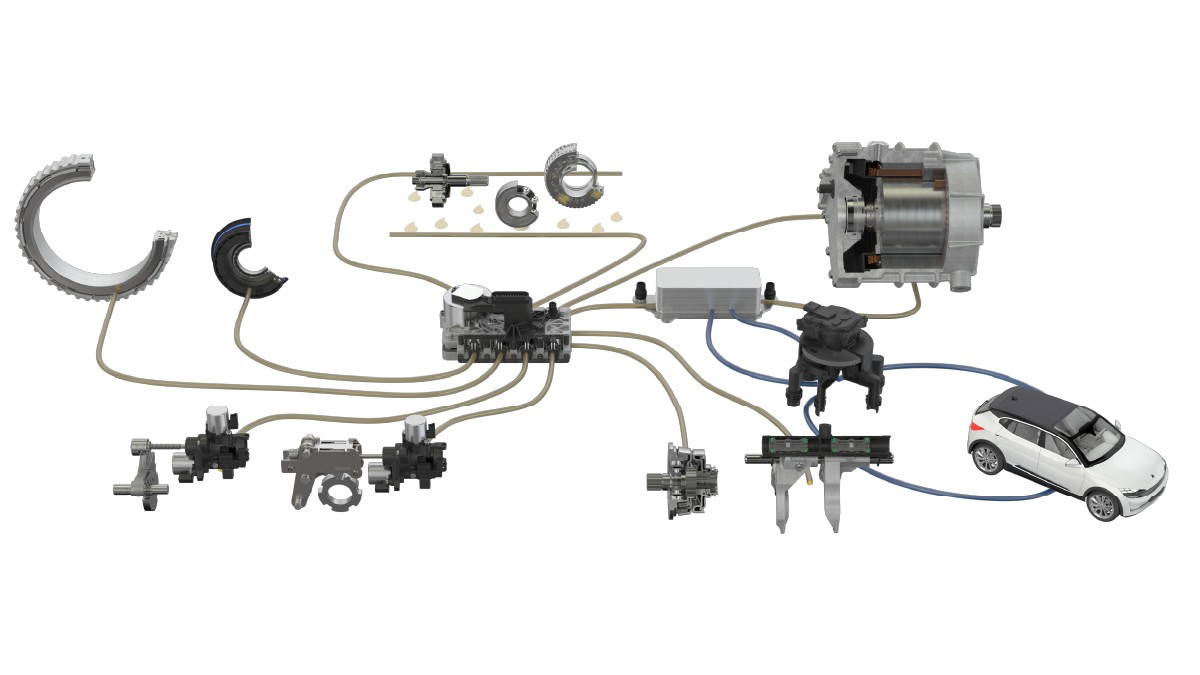
設計例 - 電動アクスルディスコネクトモジュール
シェフラーのシステム全体に関する詳細な理解、そしてSHAモジュールシステムの幅広いオプションが活かされた好例として、ディスコネクトモジュールを一体化した電動アクスルを紹介する[6]。ディスコネクト機能を採用するオプションは、電動アクスルが4WD車のセカンダリ駆動として採用されている場合に限ってその有効性が発揮される。ハイブリッド車(P4ハイブリッド)、電気自動車のいずれにも採用可能な技術だ。ディスコネクトモジュールの適用を決定するにあたって主に考慮されるのは、追加のトラクションが不要な際の逆起と摩擦損失である。これらはモータコンセプトを適切に選択することによって低減することが可能だが、ギヤによる摩擦損失および潤滑油の攪拌損失は避けることができない。
出力150kWの電動アクスル2基を搭載した60kWhバッテリの中型電気自動車の場合、WLTPサイクルの83%以上はセカンダリ駆動が有効に使用されていない。仮に搭載する電動アクスルの内、非駆動輪側のセカンダリ駆動を使用しない間断接すれば、およそ4.5%の省電力化が可能だ。スポーツカーなどの大型電気駆動車の場合、セカンダリ駆動の利用はさらに減少するため、断接により最大10%の省電力化が可能だ。
最適なディスコネクトモジュールを検討する際の出発点となるのが、パワートレインのどこに配置するかを決定する作業である。また、電動アクスルに最適なディスコネクトユニットのコンセプトを検討する際には、システム全体の構成を念頭に置く必要がある。端的に言えば、モータとの切り離しが最も大きな効果を得る鍵となる。切り離しポイントがホイールに近いほど、ディスコネクト時にホイールが駆動するギヤなどのコンポーネント数が少なくなり、摩擦損失を低減する効果が大きくなるが、その一方で、より大きなトルクレベルとなり、システム適用の労力と費用が増加する。
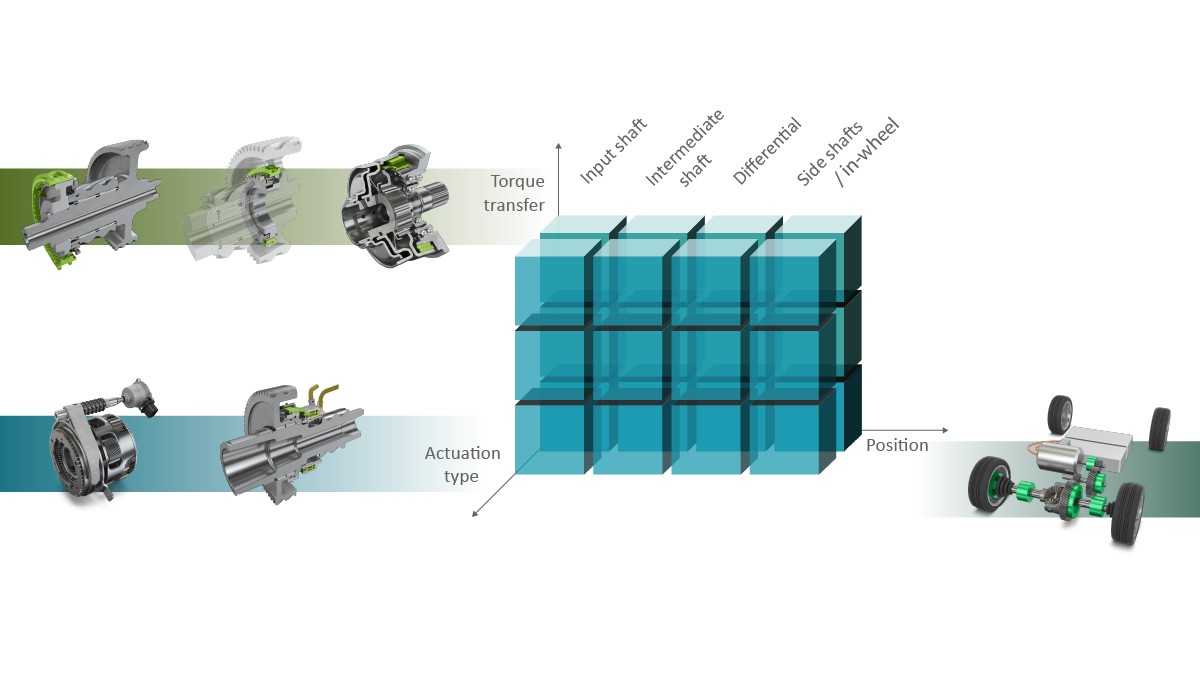
電気機械式アクチュエータ
トランスミッションの温度管理や潤滑のための油循環を油圧システムで制御する必要がない場合、もしくは分散型作動制御のコンセプトを取り入れたシステムなど、複雑なタスクを集中制御する必要がない場合は、電気機械式アクチュエータの採用も選択肢の1つとなる。シェフラーは当技術に関する開発も継続して行っており、モジュールシステムの拡充にも注力している。2018年に開催した前回のシェフラーシンポジウム[1, 7]で紹介したモジュラー式クラッチアクチュエータ(以下、MCA)を図13に示す。
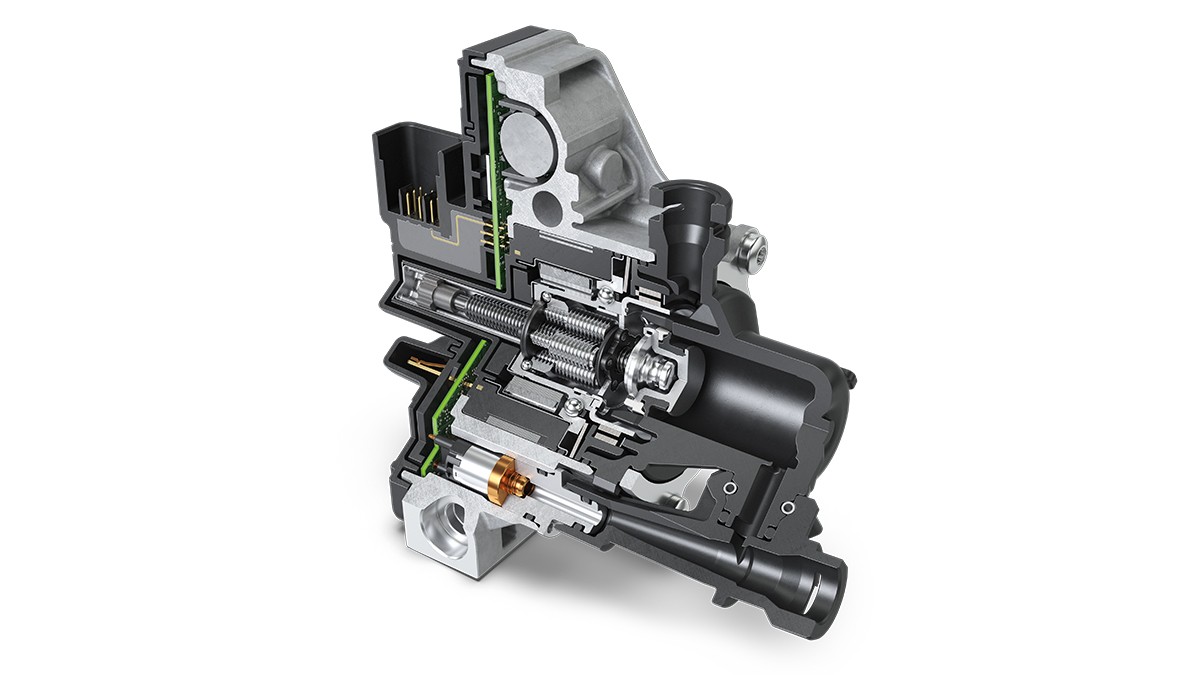
アクチュエータ開発では、モジュール性とシステムへの統合性に焦点が当てられた。従って、MCAは例えばハイブリッドマニュアルトランスミッション(MT)車向けにクラッチを完全自動化したエレクトロニッククラッチマネージメント(以下、ECM)やクラッチバイワイヤシステムなどに最適なソリューションである。このアクチュエータの中核を構成するのが、ブラシレスモータ、コントローラ、遊星ねじである。絶対位置センサを使用した高コストなシステムと違い、MCAは専用メモリ内蔵の角度位置センサを採用している。MCAはラップスプリングを利用することで前進および後退で発生する摩擦により、自己保持機能を発揮することが可能であり、優れたダイナミック性を維持しながらパワーオンデマンドを実現している。また、MCAには油圧もしくはメカニカルなインターフェースのいずれも適用することができるので、多様なシステムへの適用が可能だ。高い計算能力を有するコントロールユニットを内蔵し、複雑な制御タスクや外部センサの入力にも対応する。「オールインワン」型のMCAは、システムへの統合が簡易でロバスト性に優れた、高効率・高パフォーマンスアクチュエータだ。2018年に開催された前回のシンポジウムで紹介したMCAの設計コンセプトは、2020年に量産化された。シェフラーは2021年初頭からBMWのM4 GT3をはじめとするモータースポーツプロジェクトにも参画しており、MCAの優れた柔軟性やパフォーマンス性、信頼性は、こうしたモータースポーツ車両でも遺憾なく発揮されている。
マイクロモビリティ向けペダル駆動式ジェネレータ
シェフラーの革新的アクチュエータ技術の先進の採用例として、都市部のマイクロモビリティ向けアプリケーションを紹介する。eバイクやカーゴバイクなどの小型車両でこれまで使用されてきたチェーンを不要とし、ペダル動作を駆動輪に「シリーズ運転」で伝達するシステムだ(図14)。このシステムは、これまでのチェーン式駆動と比べ信頼性が高く、異物混入の耐性にも優れ、無摩耗でメンテナンスも不要だ。シェフラーはこのシリーズドライブ向けにアクチュエータシステムキットをベースとしたペダル駆動式ジェネレータを開発している[8]。このジェネレータは、ペダル動作を電力に変換し、モータに供給する。同時に、ペダルハウジングに抵抗をかけるので、運転者は従来の自転車と同様の運転感覚を得ることができる。高い効率性と優れたペダルレスポンスを実現するためには、トランスミッションとモータ、コントロールユニット、そしてソフトウェア制御が完璧に連携する必要がある。
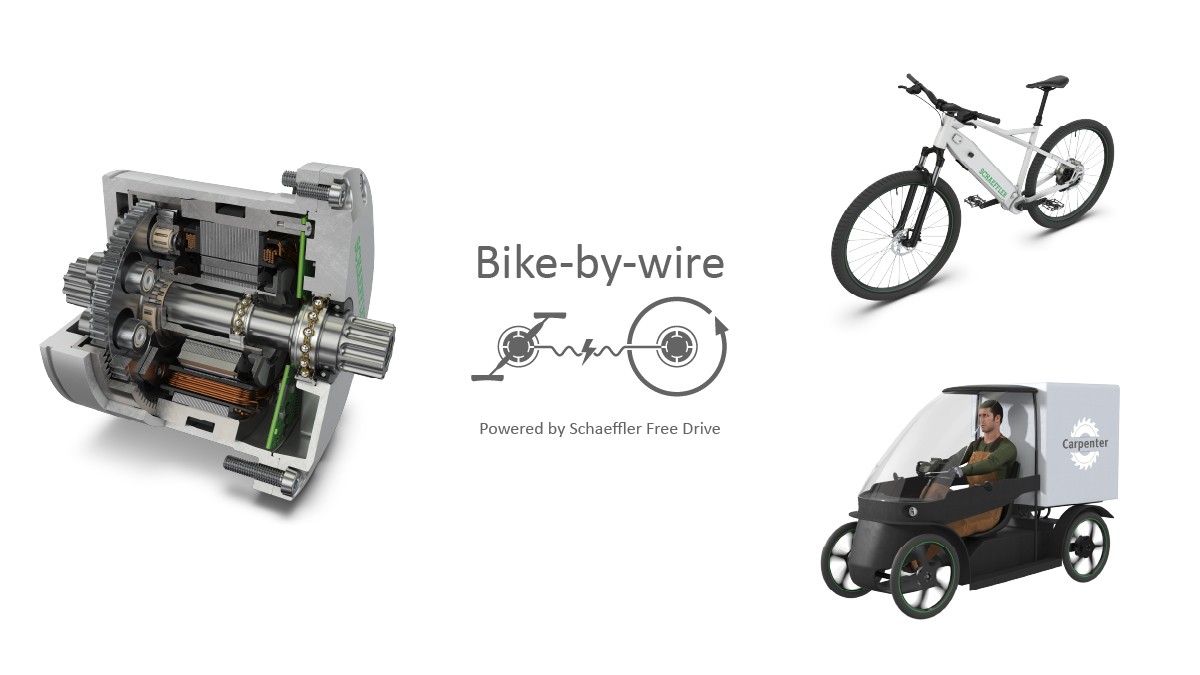
まとめ
現代のドライブシステムにおいてアクチュエータ機能に特に求められているのは、高いエネルギー効率と優れたコストパフォーマンスを実現する最適な動作条件を設定することだ。個別のタスクや分散したタスクの実行には電気機械式アクチュエータが最適だが、油圧式アクチュエータは温度制御や潤滑機能などを含んだ複雑なアーキテクチャ制御の実現が可能だ。シェフラーは、パワートレインとそのアーキテクチャに求められる個別の機能要件に対応する革新的なアクチュエータシステムソリューションを提供している。アクチュエータのコストパフォーマンスを判断する際には、設計、試験、製造コストの他に、全体システムへの実装費用、さらにはオペレーションコストまで考慮する必要がある。これらコストを削減するには、次の3つの方法が考えられる。1つ目は標準化されたソフトウェアコンポーネントの再利用。2つ目は既に開発済みのハードウェアの利用。そして3つ目は生産プロセスの共有だ。新たなアプリケーションへの対応を柔軟かつ迅速に、そして高い費用対効果で実現するために、シェフラーは「スマートハイドロリックアクチュエータキット」を開発した。油圧式アクチュエータを構成するソフトウェアとハードウェア、そして生産技術をキット化し、製品の構想から生産まで付加価値を生み出すバリューチェーンを構築する。
電気機械式アクチュエータについても、シェフラーは技術を次の段階へと進化させる開発を行っている。例として先進の「ペダル駆動式ジェネレータ」を紹介する。これは電動バイクやカーゴバイクに搭載される発電機で、従来のチェーン式に代わる新しい技術だ。このように、当社はマイクロモビリティの新たな道筋を切り開き、特に都市部における自動車排ガスの削減に貢献している。
[1] Müller, B.; Grethel, M.; Göckler, M.: Innovative Power on Demand Concepts for Transmission Actuation. Baden-Baden: Schaeffler Kolloquium, 2018
[2] Englisch, A.; Pfund, T.: Schaeffler E-Mobility – With Creativity and System Competence in the Field of Endless Opportunities. Baden-Baden: Schaeffler Kolloquium, 2018
[3] Pfund, T.: The Schaeffler eDrive Plattform – Modular and Highly Integrated. Baden-Baden: Schaeffler Kolloquium, 2018
[4] Biermann, T.: The Innovative Schaeffler Modular E-Axle. Baden-Baden: Schaeffler Kolloquium, 2018
[5] Faust, H.: The Transmission – Now and in Future the Most Efficient Connection Between the Powertrain and the Road. Baden-Baden: Schaeffler Kolloquium, 2018
[6] Homm, M.: Fascination Electric Powertrain. Baden-Baden: Schaeffler Kolloquium, 2022
[7] Hör, S.; Stehr, R.: Highly Integrated and Efficient Actuators for E-Mobility. Berlin: 18th International CTI Symposium, 2019
[8] Dumiak, M.: Electric Motor Enables Chain-Free Bike-by-Wire – New pedal-powered drive moves hybrid, cargo e-bike. https://spectrum.ieee.org/emotor-chain-free-cargo-bike, retrieved 28 September 2021